5 Common Problems of Pvd Coating Machine Coating
- Uneven Coating Thickness
- Poor Adhesion
- Equipment Overheating
- Coating Contamination
- Short Coating Lifespan
Uneven Coating Thickness
In the PVD coating process, uneven coating thickness is a common issue, mainly caused by uneven distance distribution between the workpiece and the target or evaporation source, uneven gas flow in the vacuum chamber, improper workpiece placement, or poor design of the rotation device. For example, if some areas of the workpiece are too close to the target (e.g., 5cm) while others are too far (e.g., 20cm), the areas closer to the target will receive more material particles, resulting in significant thickness differences. Additionally, unoptimized gas flow can lead to deviations in deposition rates across different areas.
To ensure uniform coating thickness, key factors must be addressed: adjust the position of the target or evaporation source to reduce distance differences; improve workpiece exposure uniformity by adding rotation devices or optimizing fixture design; and optimize gas flow in the vacuum chamber to ensure even distribution of process gas. These measures can directly improve the uniformity issues in the PVD coating process.
Specific Methods:
- Adjust the position of the target or evaporation source
- Ensure the distance between the target and the workpiece remains consistent, recommended to be within 10-15cm, to reduce deposition rate differences.
- When using multiple targets, reasonably allocate the spacing between targets to avoid localized over-deposition, thereby improving the overall quality of PVD coating.
- Optimize workpiece placement
- Evenly distribute workpieces on the fixture, avoiding stacking or blocking, to ensure each workpiece receives deposition particles uniformly.
- For complex-shaped workpieces, use layered or tilted placement to reduce shadow effects and improve coating coverage uniformity.
- Add rotation devices or improve fixture design
- Install rotation devices combining revolution and rotation, continuously changing the orientation of the workpiece during coating, recommended rotation speed of 10-20 rpm, to enhance uniformity.
- Design dedicated fixtures to ensure workpieces are securely fixed and unobstructed, optimizing the efficiency and coating quality of the PVD coating machine.
- Optimize gas flow in the vacuum chamber
- Install baffles in the chamber to guide the uniform distribution of process gas, avoiding localized excessive or insufficient gas flow.
- Adjust the positions of the inlet and outlet to ensure stable gas flow, recommended inlet flow rate of 50-100 sccm (standard cubic centimeters per minute), to reduce unevenness during the PVD coating process.
- Regularly calibrate equipment parameters
- Regularly check parameters such as target power, deposition time, and chamber pressure to ensure they meet process requirements. For example, controlling chamber pressure within 0.1-0.5 Pa can significantly improve deposition uniformity in PVD coating.
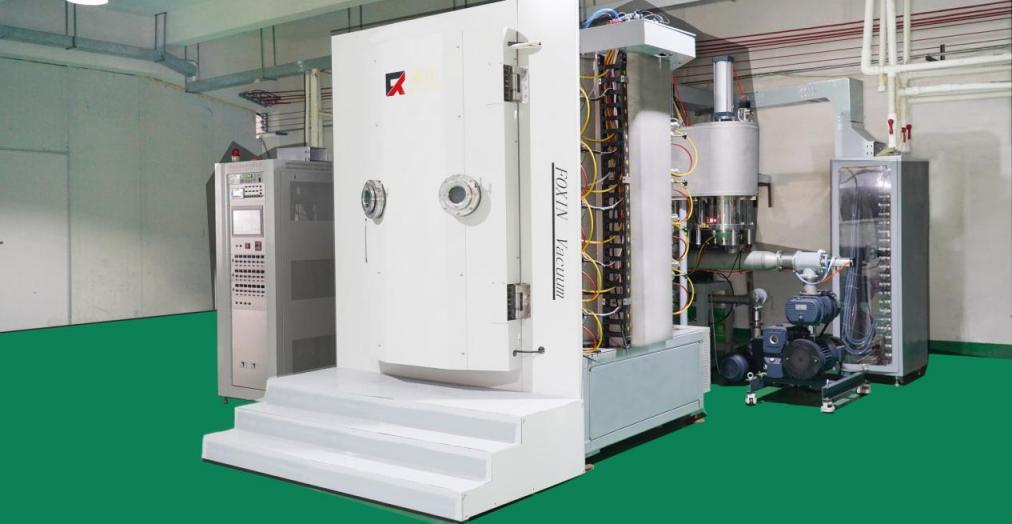
Poor Adhesion
In the PVD coating process, poor adhesion is often caused by insufficient workpiece surface cleanliness, inadequate pre-treatment, excessive thermal expansion coefficient differences between the coating and substrate, or improper process parameter settings. For example, residual oil, oxide layers, or other contaminants on the workpiece surface can hinder the bonding between the coating and substrate; if pre-treatment steps such as ion cleaning or sputter cleaning are not performed, the interfacial bonding strength will also be significantly reduced. Additionally, if the thermal expansion coefficients of the coating material and substrate do not match, stress can be generated during temperature changes, leading to reduced adhesion.
To improve coating adhesion, three aspects must be addressed: surface cleaning, pre-treatment, and process optimization. First, thoroughly clean the workpiece surface to remove oil, oxide layers, and other contaminants; second, add appropriate pre-treatment steps (e.g., ion cleaning or sputter cleaning) to enhance interfacial bonding strength; finally, optimize process parameters (e.g., deposition temperature, pressure, and power) and select coating materials suitable for the substrate to ensure compatibility between the coating and substrate.
Specific Methods:
- Thoroughly clean the workpiece surface
- Perform multi-step cleaning before PVD coating, including ultrasonic cleaning, chemical cleaning, and deionized water rinsing, to ensure the surface is free of oil, oxide layers, or other contaminants.
- Use lint-free cloths or compressed air to dry the workpiece, avoiding secondary contamination, thereby providing a clean substrate surface for PVD coating.
- Add pre-treatment steps
- Perform ion cleaning or sputter cleaning before PVD coating, using high-energy particles to bombard the workpiece surface, removing micro-contaminants and activating surface atoms to enhance adhesion.
- Recommended ion cleaning time is 5-10 minutes, and sputter cleaning power should be controlled within 200-500W to ensure optimal pre-treatment effects.
- Select suitable coating materials
- Choose coating materials with thermal expansion coefficients similar to the substrate based on the substrate material and usage environment, avoiding adhesion reduction due to thermal stress.
- For stainless steel substrates, CrN or TiN coatings can be selected as their thermal expansion coefficients match well with stainless steel, making them suitable for PVD coating processes.
- Optimize process parameters
- Control the deposition temperature within the substrate’s tolerance range, recommended range of 200-400°C, to avoid substrate performance changes due to excessive temperature.
- Adjust chamber pressure to 0.1-0.5 Pa and set the target power to an appropriate value (e.g., 3-6 kW) to improve the density and adhesion of PVD coatings.
- Enhance post-treatment processes
- After PVD coating, heat treatment or protective coating can be applied to further enhance adhesion. For example, low-temperature annealing at 150-200°C for 1-2 hours helps release residual stress.
- For decorative coatings, a transparent protective film can be added to the surface to prevent environmental erosion and extend the lifespan of PVD coatings.
Equipment Overheating
During the operation of PVD coating machines, equipment overheating is often caused by cooling system failures, prolonged high-power operation, inefficient vacuum pumps or exhaust systems, and poor heat dissipation design. For example, insufficient cooling water flow or high temperature can prevent effective heat dissipation from the target and chamber; if the equipment operates at high power for extended periods (e.g., exceeding 80% of rated power), heat accumulation will worsen; additionally, inefficient vacuum pumps or exhaust systems can prevent timely heat removal from the chamber, further exacerbating overheating issues.
To prevent equipment overheating, four aspects must be addressed: cooling system maintenance, operation time control, vacuum pump efficiency improvement, and heat dissipation design optimization. First, regularly check the cooling system to ensure cooling water flow and temperature meet requirements; second, reasonably schedule equipment operation time to avoid prolonged high-power operation; third, maintain vacuum pumps and exhaust systems to ensure efficient operation and timely heat removal; finally, improve the heat dissipation design by adding heat sinks or optimizing airflow channels to enhance overall heat dissipation capability.
Specific Methods:
- Maintain the cooling system
- Regularly check the cooling water circulation system of the PVD coating machine, ensuring sufficient cooling water flow, recommended flow rate of 10-15 L/min, and temperature controlled within 20-25°C.
- Clean scale or impurities in the cooling pipes to avoid blockages that reduce heat dissipation efficiency, ensuring the normal operation of the PVD coating machine.
- Control equipment operation time
- Avoid prolonged high-power operation, recommended continuous operation time not exceeding 4 hours, followed by a 15-30 minute cooling break.
- For high-load tasks, process workpieces in batches to reduce single operation time and extend the lifespan of the PVD coating machine.
- Improve vacuum pump and exhaust system efficiency
- Regularly maintain the vacuum pump, clean internal oil stains, or replace lubricating oil to ensure stable pumping efficiency and avoid affecting PVD coating quality.
- Check if the exhaust pipes are unobstructed to avoid heat retention due to blockages, further optimizing the working environment of the PVD coating machine.
- Optimize equipment heat dissipation design
- Add heat sinks or fans to the equipment exterior to enhance natural heat dissipation and improve the overall heat dissipation performance of the PVD coating machine.
- Optimize airflow channel design to ensure heat is quickly conducted from key components (e.g., target, power module) to the external environment, reducing the risk of equipment overheating.
- Monitor equipment temperature
- Install temperature sensors to monitor real-time temperature changes of key components (e.g., target, chamber wall) of the PVD coating machine, setting alarm thresholds (e.g., 60°C) to detect abnormalities promptly.
- Regularly record equipment operating temperature data, analyze overheating trends, and take preventive maintenance measures to ensure stable operation of the PVD coating machine.
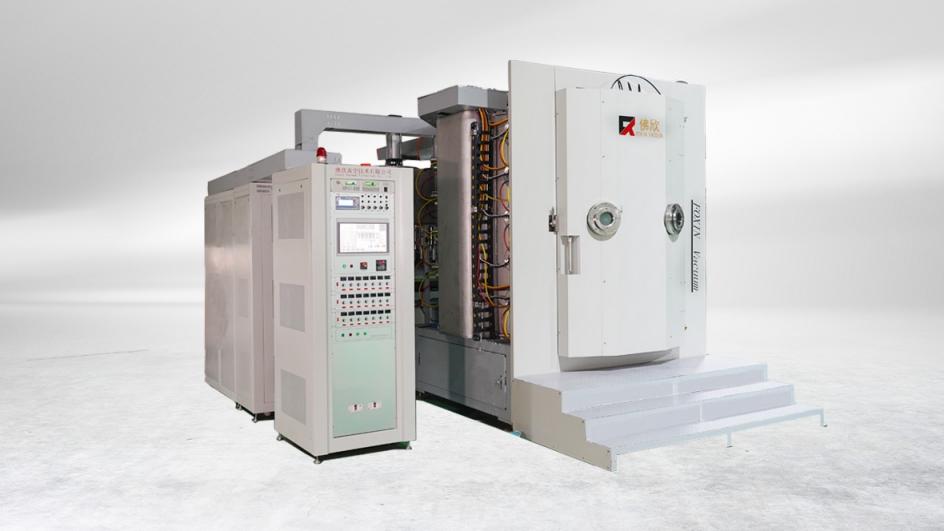
Coating Contamination
In the PVD coating process, coating contamination is often caused by residues in the vacuum chamber, insufficient purity of target or evaporation source materials, impurities in the process gas, or inadequate workpiece surface cleanliness. For example, uncleaned residues in the chamber may volatilize and mix into the coating during the process; using low-purity targets (e.g., below 99.5% purity) can introduce unnecessary elements into the coating; if the process gas contains moisture or oxygen, it may react with the deposition material, forming oxides or other contaminants; additionally, insufficient cleaning of the workpiece surface can introduce oil or particles into the coating.
To reduce coating contamination, four aspects must be addressed: chamber cleaning, material selection, gas purity, and workpiece pre-treatment. First, regularly clean the vacuum chamber to ensure no residues; second, use high-purity target or evaporation source materials and strictly control their quality; third, ensure the purity of process gas and install filtration devices to remove impurities; finally, strengthen the pre-treatment process to ensure the workpiece surface is contamination-free.
Specific Methods:
- Regularly clean the vacuum chamber
- Thoroughly clean the chamber walls, target holders, and other key components before each target replacement or different material PVD coating to avoid residue volatilization contaminating the coating.
- Use lint-free cloths and specialized cleaning agents to wipe the chamber surface, and perform high-temperature baking (e.g., 150-200°C) if necessary to remove adsorbed moisture or gas.
- Use high-purity target or evaporation source materials
- Select target or evaporation source materials with purity above 99.9% to avoid coating performance degradation due to material impurities.
- Regularly check the target surface for oxide layers or contamination, and replace degraded materials promptly to ensure PVD coating quality.
- Ensure process gas purity
- Use high-purity process gas (e.g., 99.999% argon) and install gas filters to remove moisture, oxygen, or other impurities.
- Control the inlet flow rate and pressure, recommended flow rate of 50-100 sccm, and chamber pressure maintained within 0.1-0.5 Pa, to reduce the possibility of gas contamination.
- Strengthen workpiece pre-treatment
- Perform multi-step cleaning before PVD coating, including ultrasonic cleaning, chemical cleaning, and deionized water rinsing, to ensure the surface is free of oil, particles, or other contaminants.
- Use compressed air to dry the workpiece and store it in a dust-free environment to avoid secondary contamination, providing a clean substrate surface for PVD coating.
- Optimize coating environment
- Evacuate the chamber to below 10⁻⁵ Pa before PVD coating to ensure no residual gas or moisture in the chamber.
- Add ion cleaning steps, using high-energy particles to bombard the chamber walls and workpiece surface, further removing micro-contaminants and improving the purity of PVD coatings.
Short Coating Lifespan
In PVD coating applications, short coating lifespan is often caused by improper coating material selection, unreasonable process parameter settings, harsh workpiece usage environments, or insufficient post-treatment. For example, if the coating material does not match the actual usage environment of the workpiece (e.g., using ordinary wear-resistant coatings in highly corrosive environments), the coating will fail quickly; improper process parameters (e.g., deposition temperature, pressure, and power) can reduce coating density and bonding strength, making it more prone to wear or peeling; additionally, excessive wear, corrosion, or high temperatures during workpiece usage can significantly shorten the coating lifespan.
To extend the coating lifespan, four aspects must be addressed: material selection, process optimization, usage environment improvement, and post-treatment enhancement. First, select suitable coating materials based on the actual usage environment of the workpiece to ensure performance meets requirements; second, optimize coating process parameters to improve coating density and adhesion; third, improve the usage conditions of the workpiece to reduce unnecessary wear or corrosion; finally, enhance coating performance through appropriate post-treatment processes.
Specific Methods:
- Select suitable coating materials
- Choose high-performance coating materials based on the workpiece’s usage environment. For example, CrN or TiAlN coatings can be used in highly corrosive environments, and TiSiN or Al2O3 coatings can be used in high-temperature environments, suitable for PVD coating processes.
- Ensure the thermal expansion coefficients of the coating material and substrate match to avoid coating cracking or peeling due to thermal stress, extending the lifespan of PVD coatings.
- Optimize coating process parameters
- Control the deposition temperature within the substrate’s tolerance range, recommended range of 200-400°C, to improve coating density and bonding strength.
- Adjust chamber pressure to 0.1-0.5 Pa and set the target power to an appropriate value (e.g., 3-6 kW) to ensure uniform and defect-free PVD coatings.
- Improve workpiece usage environment
- Where possible, reduce direct contact between the workpiece and hard particles, corrosive media, or high-temperature environments to minimize external factors affecting PVD coatings.
- Perform surface lubrication or add protective covers to the workpiece to reduce friction and corrosion effects on the coating, extending the lifespan of PVD coatings.
- Enhance post-treatment processes
- Perform low-temperature annealing (e.g., 150-200°C for 1-2 hours) after PVD coating to release residual stress and improve coating stability.
- For decorative coatings, apply a transparent protective film to the surface to prevent environmental erosion and enhance the durability of PVD coatings.
- Regular maintenance and inspection
- Regularly inspect coating wear and promptly repair or replace damaged coatings to avoid issue escalation, ensuring long-term performance of PVD coatings.
- Use microscopes or hardness testers to inspect the microstructure and performance of coatings to ensure they meet design requirements, providing reliable assurance for PVD coating applications.