Custom Tooling & Mold: Metal PVD Coating Machine
For manufacturers, tools and molds must be durable to get the job done consistently and with the highest quality. This is where PVD (Physical Vapor Deposition) coatings come into play, offering an effective solution to extend the life of these essential components. In this blog, we will explore how metal PVD coating machine, such as this offered by Foxin Vacuum Technology Company, is revolutionizing the manufacturing industry.
Metal PVD Coating Machine by Foxin Vacuum Technology Company is a game-changer in the world of craft manufacturing. Its precision, ease of use, and ability to enhance the quality and durability of metal products make it an invaluable tool for artisans and manufacturers alike. By following the steps outlined in this blog, craft manufacturers can harness the full potential of this technology to create perfect craft manufacturing productions that stand the test of time.
Metal PVD Coating Machine: The Role of PVD Coatings in Tooling and Molds
Injection molds, die-casting molds, and other tooling used in manufacturing processes endure extreme conditions. The constant exposure to high temperatures, abrasive materials, and repeated use can cause wear, corrosion, and even failure over time. PVD coatings act as a protective shield for these vital components, significantly enhancing their durability and lifespan.
Metal PVD Coating Machine: Setting Up the Metal PVD Coating Machine
1. Metal PVD Coating Machine: Preparation and Safety Measures
Safety is paramount when working with any machinery. Before operating the Metal PVD Coating Machine, ensure that the work area is well-ventilated, free from flammable materials, and equipped with the necessary safety gear, such as gloves and eye protection. Foxin’s machines are designed with user safety in mind, featuring comprehensive safety systems.
2. Metal PVD Coating Machine: Loading the Substrate
Place the metal parts you want to coat onto the machine’s rack or holder. Make sure they are clean and free from any contaminants that could affect the coating process. Foxin’s machines often come with specialized racks and fixtures designed for optimal coating results.
3. Metal PVD Coating Machine: Machine Calibration
One of the key advantages of Foxin’s Metal PVD Coating Machines is their precise control and automation features. Use the machine’s interface to input the desired coating parameters, including deposition rate, temperature, and duration. The machine will handle the rest, ensuring a consistent and uniform coating.
Metal PVD Coating Machine: Operating the Machine
1. Metal PVD Coating Machine: Initiating the Coating Process
Once the machine is set up and calibrated, initiate the coating process. The Metal PVD Coating Machine will create a vacuum environment within its chamber, ensuring that the vaporized coating material adheres evenly to the metal substrate.
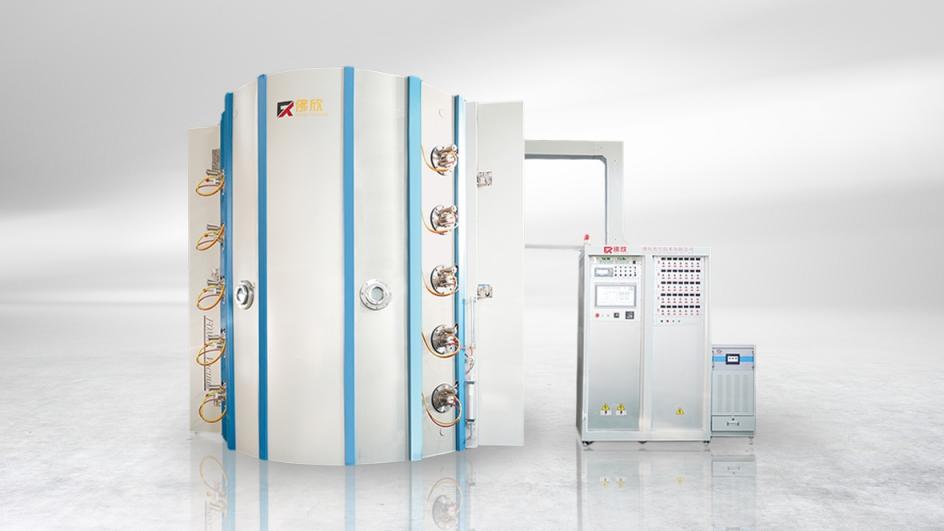
2. Metal PVD Coating Machine: Monitoring and Quality Control
During the coating process, it’s crucial to monitor the machine’s performance and the quality of the coating. Foxin’s machines often include real-time monitoring and quality control systems, allowing operators to make adjustments if necessary.
3. Metal PVD Coating Machine: Finishing Touches
Once the coating process is complete, carefully remove the coated metal parts from the machine. Foxin’s machines are designed for ease of use, making this step straightforward.
Metal PVD Coating Machine: The PVD Coating Process
Foxin’s metal PVD coating machines utilize a vacuum chamber to apply coatings to tooling and molds. Here’s a simplified overview of the PVD coating process:
1. Cleaning and Preparation: The tooling or mold is thoroughly cleaned and prepped to ensure optimal adhesion of the PVD coating.
2. Loading: The cleaned component is placed in the vacuum chamber of the PVD coating machine.
3. Deposition: A specialized process, such as sputtering or evaporation, is used to deposit a thin layer of the chosen PVD coating material onto the component’s surface.
4. Quality Control: Coating thickness and uniformity are closely monitored to ensure consistent results.
5. Unloading: Once the coating process is complete, the coated component is removed from the machine.
The Advantages of Foxin’s Metal PVD Coating Machine
When it comes to PVD coating machines for metal components, Foxin Vacuum Technology Company is a name that stands out. This manufacturer specializes in producing high-quality machines designed to apply PVD coatings to various substrates. Their machines are renowned for their precision, efficiency, and reliability, making them a top choice for businesses looking to improve tooling and mold performance.
1. Enhanced Durability: Foxin’s PVD coating machines create a thin, protective layer on the surface of molds and tooling, making them more resistant to wear, corrosion, and chemical damage. This results in longer lifespans for these crucial components, reducing downtime and replacement costs.
2. Improved Performance: Coated molds and tooling exhibit improved release properties, reducing the chances of material sticking during the manufacturing process. This, in turn, leads to higher production efficiency and reduced rejects.
3. Versatility: Foxin’s machines are versatile and can be used for a wide range of applications. Whether you’re working with steel, aluminum, or other metals, these machines can apply PVD coatings tailored to your specific needs.
4. Environmentally Friendly: PVD coating is an environmentally friendly process, as it does not involve harmful chemicals or produce hazardous waste. Foxin’s machines are designed to be energy-efficient, contributing to sustainability efforts in the manufacturing industry.
Metal PVD Coating Machine Success Story: French Stainless Steel Sheet Manufacturer
A renowned stainless steel sheet manufacturer from France turned to FOXIN for their PVD coating needs. The customer was seeking ways to enhance the performance of their stainless steel sheets for various applications. After visiting FOXIN’s facilities, they were not only impressed by the state-of-the-art machines but also by the presence of knowledgeable professionals who could address their queries.
FOXIN’s team worked closely with the French customer to understand their specific requirements. They recommended a custom PVD coating solution that would significantly improve the wear resistance and corrosion protection of the stainless steel sheets, extending their lifespan and increasing customer satisfaction.
The result? The French manufacturer experienced a notable increase in the longevity of their products. This not only saved them costs on replacements but also boosted their reputation for delivering high-quality stainless steel sheets.
Conclusion
Foxin Vacuum Technology Company’s metal PVD coating machine is changing the game in the manufacturing world. By extending the lifespan of injection molds and other tooling, these machines offer a cost-effective and environmentally friendly solution to a common industry challenge. Manufacturers looking to enhance the durability and performance of their molds and tooling can benefit greatly from investing in PVD coating technology, and Foxin stands at the forefront of this innovation. With their precision-engineered machines, they are empowering manufacturers to achieve higher quality and efficiency while reducing maintenance costs.