PVD Coating Full Form: Comprehensive Comparison & Material Selection
PVD coating is a versatile and efficient technology, offering numerous advantages over other surface engineering methods. PVD, which stands for Physical Vapor Deposition, is a process that deposits thin films of various materials onto surfaces, enhancing their durability, appearance, and functionality. This advanced technique is employed across diverse industries, thanks to its ability to match materials with a wide range of surfaces, including metal, ceramic, and plastic materials. In this exploration, we’ll delve into PVD Coating Full Form’s numerous advantages, and compare it to other coating techniques like CVD, electroplating, and thermal spraying, the world of PVD coating, and how it is harnessed to cater to the unique demands of different materials.
PVD Coating Full Form: A Quick Overview
PVD stands for “Physical Vapor Deposition.” It is a process used to deposit thin films or coatings of various materials onto surfaces. It is commonly used in manufacturing and various industries to improve the surface properties of objects, such as enhancing wear resistance, corrosion resistance, or providing decorative finishes. PVD Coating Full Form involves the vaporization of a solid material in a vacuum environment, which then condenses onto the object’s surface, creating a thin, adherent coating. This process is widely used in applications like cutting tools, decorative coatings on jewelry and watches, and automotive components, among others.
PVD Coating Full Form: Full Form and Its Advantages Over Other Techniques
1. PVD Coating Full Form: PVD vs. CVD (Chemical Vapor Deposition)
When it comes to comparing PVD and CVD, the key distinction lies in the deposition process itself. In PVD, the coating material is physically vaporized and then deposited on the substrate. In contrast, CVD, which stands for Chemical Vapor Deposition, involves chemical reactions that occur on the substrate surface to form the desired coating. PVD offers the advantage of better adhesion and a wider range of material choices, making it ideal for applications where precise control over coating properties is crucial.
2. PVD Coating Full Form: PVD vs. Electroplating
Electroplating, a common method for applying metallic coatings, involves the immersion of the substrate and a metal electrode into an electrolyte bath. While electroplating has its merits, PVD surpasses it in several aspects. PVD coatings are typically thicker and more uniform, offering enhanced corrosion resistance and improved wear resistance. Additionally, PVD does not rely on chemical reactions, reducing the risk of environmental hazards associated with electroplating.
3. PVD Coating Full Form: PVD vs. Thermal Spraying
Thermal spraying, as the name suggests, involves melting a material and spraying it onto the substrate’s surface. While it’s suitable for certain applications, PVD offers distinct advantages. PVD coatings are extremely thin, often measuring in micrometers, which means they add minimal thickness to the substrate. This makes them ideal for precision components where dimensional tolerances are critical. Furthermore, PVD coatings exhibit superior adhesion, hardness, and resistance to wear and corrosion compared to thermal sprayed coatings.
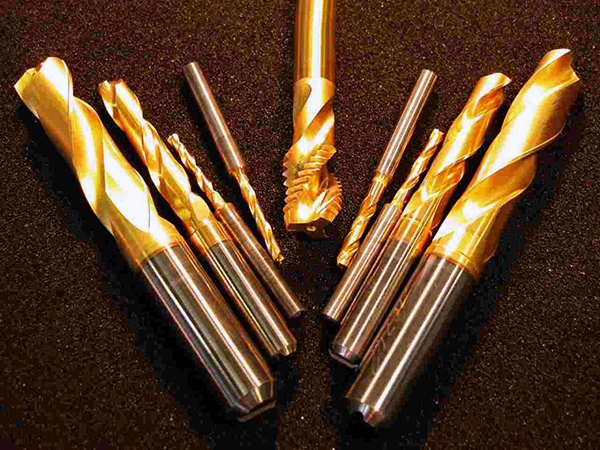
4. PVD Coating Full Form: Why Choose Foxin Vacuum Technology Company for PVD Coating?
When it comes to PVD Coating Full Form, choosing the right manufacturer is paramount. Foxin Vacuum Technology Company is a leading name in the industry, renowned for its cutting-edge PVD coating equipment and expertise. With a commitment to quality and innovation, Foxin offers tailored PVD solutions to meet the diverse needs of industries ranging from automotive and aerospace to medical devices and consumer electronics.
PVD Coating Full Form: Matching Materials with Precision
1. Metallic Marvel: PVD Coating Full Form on Metal
One of the most common applications of PVD Coating Full Form is on metal surfaces. Whether it’s for enhancing the aesthetics of jewelry, providing wear resistance to industrial tools, or improving the corrosion resistance of automotive components, PVD coating has proved its mettle. For metal surfaces, a wide array of materials can be used for coating, including titanium, chromium, and aluminum. These coatings not only bolster the appearance but also contribute to the longevity of the metal, making it an ideal choice in various industries.
2. Elegance Meets Endurance: PVD Coating Full Form on Ceramic Surfaces
Ceramic materials are known for their durability and resistance to wear and corrosion. However, PVD Coating Full Form takes their performance to the next level. When ceramic surfaces are coated with materials such as titanium nitride (TiN) or zirconium nitride (ZrN), they acquire enhanced hardness, reduced friction, and improved resistance to chemical degradation. This makes PVD-coated ceramic components invaluable in applications ranging from cutting tools to watch casings.
3. Plastic Precision: PVD Coating Full Form on Plastic Materials
PVD Coating Full Form is not limited to metals and ceramics; it also caters to the specific needs of plastic materials. While plastics offer flexibility and cost-effectiveness, they can lack the durability required in certain applications. PVD coating can add a protective layer to plastic components, making them more resilient and robust. Plastic components in the automotive, electronics, and medical device industries benefit significantly from this technology.
4. The Foxin Advantage: Pioneering PVD Coating Full Form Technology
When it comes to PVD Coating Full Form technology, one name that stands out is Foxin Vacuum Technology Company. With a reputation for innovation and precision, Foxin has been at the forefront of advancing PVD coating applications across a wide range of materials. Their state-of-the-art vacuum chambers and cutting-edge deposition techniques ensure that PVD coatings are not only effective but also precise, catering to the unique requirements of each material.
Conclusion
PVD coating, or Physical Vapor Deposition, is a versatile and precise surface treatment technique that offers numerous advantages over other coating methods like CVD, electroplating, and thermal spraying. Its ability to control coating properties with precision, minimal thickness addition, and excellent performance characteristics make it a preferred choice in various industries. When seeking reliable PVD Coating Full Form solutions, look no further than Foxin Vacuum Technology Company for state-of-the-art equipment and unmatched expertise in the field.