What Is the Difference Between Gold Plating and Pvd Gold Plating
Traditional gold plating typically has a thickness of 0.5 to 5 microns, with relatively low hardness (HV 50-100). It tends to wear down easily and isn’t very resistant to corrosion. While it’s cheap, it’s not particularly eco-friendly. On the other hand, PVD (Physical Vapor Deposition) gold coating is thicker—ranging from 1 to 10 microns—and boasts a much higher hardness of HV 200-300. This makes it far more durable, corrosion-resistant, and environmentally friendly, though it comes at a higher cost. Because of these qualities, PVD gold plating is often used for high-end products like luxury watches and jewelry.
Process
Traditional Gold Plating
Also known as electroplating, this method uses an electrochemical reaction to deposit gold ions onto the surface of an object. The process involves immersing the item into a solution containing gold salts, then applying an electric current to reduce the gold ions into metallic gold, which adheres to the surface. Though this technique has been around for centuries and is well-established, it does have some drawbacks.
PVD Gold Plating
PVD gold coating is a modern technology that deposits a thin layer of gold or other metals onto an object in a vacuum environment. In this process, the gold (or gold alloy) is vaporized using heat or sputtering techniques, then allowed to condense on the object’s surface. Compared to traditional plating, PVD offers several significant advantages.
Process Steps
Traditional Gold Plating:
- Pre-Treatment: Clean the object to remove oils, dirt, or oxidation.
- Activation: Prepare the surface so it can bond better with the gold ions.
- Electroplating: Submerge the object in the electrolyte solution and apply an electric current to deposit the gold.
- Post-Treatment: Rinse, dry, and polish the finished product.
PVD Gold Plating:
- Pre-Treatment: Similar cleaning steps to ensure the surface is free of contaminants.
- Mounting: Secure the object inside the vacuum chamber.
- Vacuum Pumping: Create a high-vacuum environment within the chamber.
- Deposition: Vaporize the gold material and let it settle onto the object’s surface.
- Post-Treatment: Final cleaning and drying.
Comparison of Process Characteristics
Feature | Traditional Gold Plating | PVD Gold Plating |
---|---|---|
Coating Thickness | 0.5-5 microns | 1-10 microns |
Hardness | HV 50-100 | HV 200-300 |
Wear Resistance | Poor | Excellent |
Corrosion Resistance | Poor | Excellent |
Adhesion | Weak | Strong |
Environmental Impact | High pollution risk | Environmentally friendly |
Cost | Low | High |
Applications | Mass production, low-wear items | High-end, durable products |
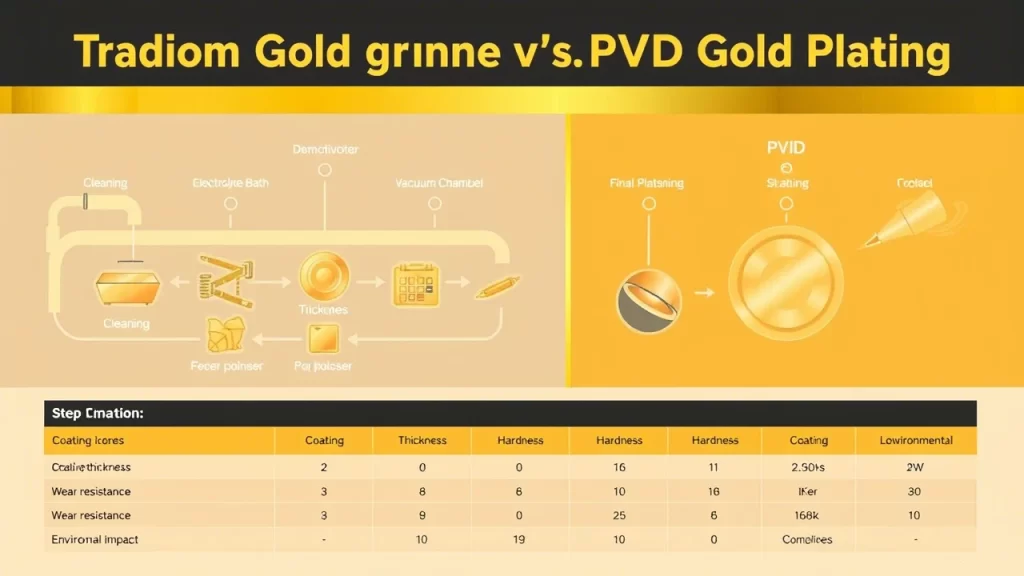
Durability
PVD gold coating stands out when it comes to durability:
Wear Resistance
- Increased Hardness: PVD coatings are 2-6 times harder than traditional gold plating. While traditional plating has a hardness of HV 50-100, PVD reaches HV 200-300 or even higher.
- Denser Structure: The crystalline structure of PVD coatings is much tighter, making them less prone to scratching or chipping compared to the looser structure of traditional plating.
- Real-World Example: Luxury watches and fine jewelry often use PVD because they need to maintain their appearance despite frequent handling and exposure to friction.
Corrosion Resistance
- Barrier Against Corrosive Agents: PVD creates a dense, uniform layer that blocks moisture, acids, and other corrosive substances.
- Chemical Stability: The materials used in PVD coatings are highly stable and don’t react easily with environmental factors.
- Real-World Example: Products exposed to harsh environments, such as marine equipment or chemical machinery, benefit greatly from PVD’s ability to resist corrosion.
Oxidation Resistance
- Non-Reactive Surface: PVD coatings are less likely to oxidize or tarnish, maintaining their original luster.
- Heat Tolerance: Some PVD coatings remain stable even at high temperatures, resisting oxidation.
- Real-World Example: Architectural fixtures and outdoor gear rely on PVD to prevent fading and discoloration over time.
Thickness
Traditional gold plating usually ranges from 0.5 to 5 microns thick, while PVD coatings are slightly thicker, ranging from 1 to 10 microns. Not only is PVD thicker, but it also provides better uniformity, with tolerances as precise as ±0.1 microns, compared to ±0.5 microns for traditional plating.
Because traditional plating is thinner, it’s more susceptible to damage from external forces, leading to scratches, peeling, or discoloration. PVD’s thicker and harder coating (HV 200-300 vs. HV 50-100) offers superior protection against wear and tear, extending the lifespan of the product.
For this reason, traditional plating is best suited for everyday accessories where thickness isn’t critical, whereas PVD is ideal for premium items like luxury watches and jewelry that demand both beauty and longevity.
Cost
While PVD equipment requires a hefty upfront investment—often several times more expensive than traditional plating—it delivers long-term savings thanks to its durability and minimal maintenance needs. Here’s how the costs compare:
Cost Factor | Traditional Plating | Gold Plating |
---|---|---|
Equipment Investment | Low | High |
Processing Fees | Low | High |
Maintenance Costs | High | Low |
Material Efficiency | Low | High |
Environmental Costs | High | Low |
Overall Cost | Moderate | Moderate |
Although PVD processing fees are higher, the reduced need for repairs and replacements balances out the initial expense. Plus, PVD minimizes waste, making it a more sustainable option overall.
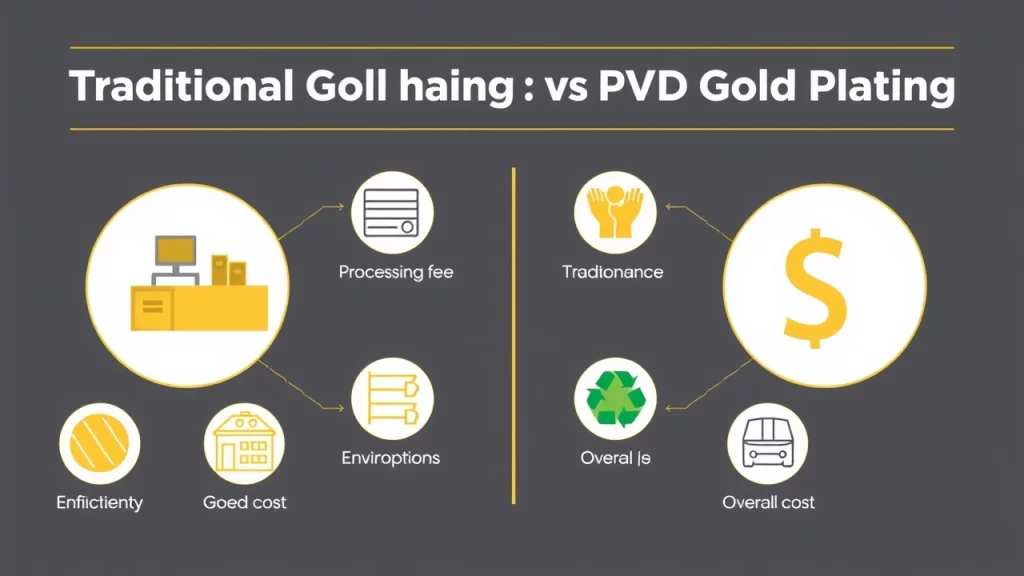
Appearance
When it comes to looks, there are notable differences between traditional gold plating and PVD:
- Color Consistency: Traditional plating often starts with a soft, warm glow but can develop scratches or patches as the base metal shows through due to wear. PVD, however, maintains a consistent color even as the top layer wears off, thanks to its underlying hard layers.
- Customization: PVD allows for greater flexibility in achieving different shades of gold, including rose gold or deep yellow tones, by tweaking parameters during the process. Traditional plating relies solely on the type of gold alloy used, offering fewer options.
- Finish Quality: PVD produces a sleek, mirror-like sheen, while traditional plating tends to have a softer, warmer finish that may dull over time.
Applications
Traditional gold plating works well for inexpensive, mass-produced items like costume jewelry, whereas PVD excels in high-value applications like luxury watches, precision instruments, aerospace components, and decorative pieces.
Examples of PVD applications include:
- Optics: Enhancing lenses for glasses and cameras.
- Semiconductors: Depositing conductive or insulating films for advanced chips.
- Solar Panels: Improving efficiency in renewable energy systems.
Environmental Impact
Traditional gold plating poses significant environmental risks due to toxic chemicals like cyanide used in the process. These substances can harm workers and pollute water and soil if not properly managed.
In contrast, PVD operates in a vacuum without harmful chemicals, producing minimal waste that’s easy to recycle. This makes PVD a greener choice, especially in industries prioritizing sustainability.