What is PVD Coating? A Complete Guide to Physical Vapor Deposition
PVD coating transforms solid materials into gas in a vacuum, depositing them to create a thin, durable film that enhances hardness, wear resistance, corrosion resistance, and aesthetics.
Introduction to PVD Coating
PVD (Physical Vapor Deposition) is a high-tech surface treatment method. In simple terms, it involves converting solid materials into gas in a vacuum environment and then depositing them onto an object’s surface to form an ultra-thin protective layer. This layer not only boosts the object’s hardness, wear resistance, and corrosion resistance but also enhances its appearance. Everyday items like kitchen knives, watches, phone cases, and even car parts often utilize this technology.
Originally developed for aerospace and military applications, PVD has now become a part of our daily lives. For instance, PVD-coated kitchen knives stay sharper longer and resist rust, while PVD-coated watch cases are not only durable but also look premium. Compared to traditional electroplating, PVD coating is more environmentally friendly, produces no pollution, and offers better adhesion and uniformity.
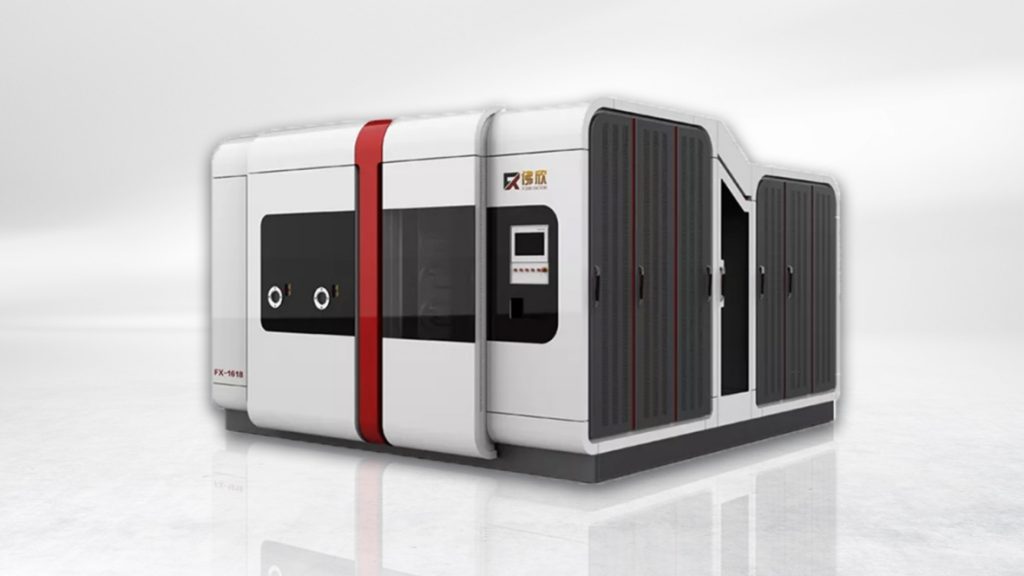
Principles and Process
The core principle of PVD (Physical Vapor Deposition) is to convert solid materials into a gaseous state through physical methods and then deposit them onto a target surface in a vacuum, forming a uniform and dense film. This process involves three key steps: vaporization, transport, and deposition. Here’s a detailed breakdown of the working principles and process.
Basic Principles of PVD
PVD technology uses high energy (such as heat, electric fields, or ion bombardment) to directly convert solid coating materials (like metals or compounds) into a gaseous state. This process occurs in a vacuum to minimize interference from air molecules, ensuring the coating’s purity and uniformity. The vaporized atoms or molecules then travel through the vacuum chamber and condense on the target surface, forming a dense film.
Precise control of the physical process is crucial in PVD technology. For example, in sputtering, high-energy ions bombard the target material, “knocking” atoms off and depositing them onto the target surface. Research shows that titanium nitride (TiN) coatings prepared by sputtering can achieve hardness levels above 2000 HV, far exceeding that of ordinary steel (around 200 HV). This high hardness makes TiN coatings widely used in cutting tools and molds, significantly extending their lifespan.
Additionally, the vacuum environment and high energy input in PVD ensure strong adhesion between the coating and the substrate. Scratch and pull-off tests confirm that PVD coatings typically achieve adhesion strengths of over 50 N, demonstrating excellent bonding strength. This strong adhesion not only enhances the coating’s durability but also ensures stable performance under high-stress conditions.
PVD Process Steps
The PVD process involves the following steps:
- Pre-treatment: Clean the target surface to remove oils, oxides, and other impurities, ensuring strong coating adhesion. Studies show that surface cleanliness directly affects coating adhesion; untreated surfaces can reduce adhesion by over 30%.
- Vacuum Pumping: Evacuate the chamber to a high vacuum state (typically below 10⁻³ Pa) to minimize gas molecule interference. High vacuum is critical for PVD; insufficient vacuum can lead to gas inclusion, affecting coating density and performance.
- Vaporization: Convert the coating material into a gaseous state through sputtering, evaporation, or ion plating.
- Sputtering: Use high-energy ions to bombard the target material, knocking off atoms. Sputtering is suitable for complex-shaped workpieces, offering good coating uniformity but higher equipment costs.
- Evaporation: Heat the coating material to evaporate it. Evaporation is simple and suitable for large-area coatings but offers weaker adhesion.
- Ion Plating: Combine evaporation with an electric field to accelerate ions, enhancing coating adhesion. Ion plating produces dense coatings with strong adhesion but is complex and costly.
- Transport and Deposition: The vaporized atoms or molecules travel through the vacuum chamber and condense on the target surface, forming a film. Deposition rate is critical; too fast can cause uneven coatings, while too slow affects efficiency.
- Post-treatment: Cool, polish, or inspect the coating to ensure quality and performance. For example, scratch and pull-off tests confirm that PVD coatings typically achieve adhesion strengths of over 50 N, demonstrating excellent bonding strength.
Common PVD Techniques
Here are the main PVD techniques and their characteristics:
Method | Principle | Characteristics |
---|---|---|
Sputtering | High-energy ions bombard the target, knocking off atoms that deposit on the target surface. | Uniform coating, suitable for complex shapes; higher equipment costs. |
Evaporation | Heat the coating material to evaporate it, then deposit it on the target surface. | Simple process, suitable for large-area coatings; weaker adhesion. |
Ion Plating | Combine evaporation with an electric field to accelerate ions, enhancing coating adhesion. | Strong adhesion, dense coating; complex process, higher costs. |
Key Parameters and Influencing Factors
PVD coating quality is influenced by the following key parameters:
- Vacuum Level: Higher vacuum improves coating quality.
- Target Purity: Higher target purity ensures stable coating performance.
- Deposition Rate: Too fast can cause uneven coatings; too slow affects efficiency.
- Substrate Temperature: Too high can cause coating deformation; too low affects adhesion.
By precisely controlling these parameters, PVD coating performance can be optimized to meet various application needs. For example, in high-temperature cutting tools, titanium aluminum nitride (TiAlN) coatings maintain excellent performance above 800°C, significantly extending tool lifespan.
Materials and Properties
The performance and application range of PVD coatings largely depend on the materials used. Common PVD coating materials include titanium nitride (TiN), titanium carbide (TiC), and diamond-like carbon (DLC). These materials offer unique physical and chemical properties, excelling in hardness, wear resistance, and corrosion resistance. Here’s a detailed analysis of materials and their properties.
Common PVD Coating Materials
PVD coating material selection depends on specific application needs. Here are some common materials and their properties:
Material | Chemical Formula | Hardness (HV) | Wear Resistance | Corrosion Resistance | Main Applications |
---|---|---|---|---|---|
Titanium Nitride (TiN) | TiN | 2000 – 2500 | High | Medium | Cutting tools, molds, decorative coatings |
Titanium Carbide (TiC) | TiC | 2500 – 3000 | Very High | Medium | High-wear tools, cutting tools |
Diamond-Like Carbon (DLC) | C (amorphous) | 1500 – 4000 | Very High | High | Automotive parts, medical devices, electronic equipment |
Titanium Aluminum Nitride (TiAlN) | TiAlN | 3000 – 3500 | Very High | High | High-temperature cutting tools, aerospace components |
Titanium nitride (TiN) is widely used in cutting tools, molds, and decorative coatings due to its high hardness (2000 – 2500 HV) and golden appearance. Studies show that TiN coatings can extend cutting tool lifespan by 3 – 5 times. Titanium carbide (TiC) offers even higher hardness (2500 – 3000 HV), making it ideal for high-wear tools and cutting tools.
Diamond-like carbon (DLC) coatings, with their extremely high hardness (1500 – 4000 HV) and low friction coefficient, excel in automotive parts, medical devices, and electronic equipment. For example, DLC coatings on automotive engine piston rings significantly reduce friction loss and improve fuel efficiency. Titanium aluminum nitride (TiAlN) offers high hardness and oxidation resistance, making it ideal for high-temperature cutting tools and aerospace components, maintaining excellent performance above 800°C.
Physical and Chemical Properties of PVD Coatings
PVD coatings exhibit the following notable properties:
- High Hardness: PVD coatings are typically much harder than the substrate. For example, titanium nitride can achieve hardness above 2000 HV, while ordinary steel is around 200 HV.
- Wear Resistance: The high hardness and dense structure of coating materials effectively resist wear, extending tool and component lifespan.
- Corrosion Resistance: Some materials (like DLC and TiAlN) offer excellent chemical stability, resisting acids, alkalis, and other corrosive media.
- Low Friction Coefficient: Materials like DLC have extremely low friction coefficients, reducing friction and energy loss between moving parts.
Key Properties and Influencing Factors
PVD coating performance is influenced by the following factors:
- Material Selection: Different materials vary significantly in hardness, wear resistance, and corrosion resistance.
- Coating Thickness: Too thin may offer insufficient protection; too thick may affect substrate performance.
- Deposition Process: Process parameters (like temperature, pressure, deposition rate) directly affect coating density and adhesion.
- Substrate Properties: Substrate hardness, surface roughness, and chemical composition affect coating adhesion strength.
By precisely controlling these factors, PVD coating performance can be optimized to meet various application needs. For example, in high-temperature cutting tools, titanium aluminum nitride (TiAlN) coatings maintain excellent performance above 800°C, significantly extending tool lifespan.
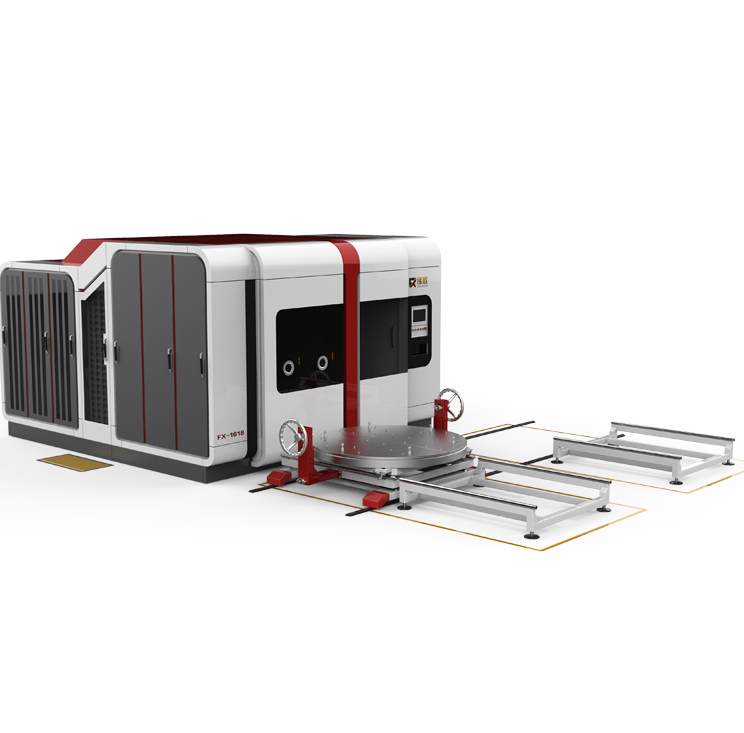
Advantages and Limitations
Advantages of PVD Technology
PVD technology offers several key advantages:
- High Hardness and Wear Resistance: PVD coatings are extremely hard. For example, titanium nitride (TiN) coatings can achieve hardness above 2000 HV, far exceeding ordinary steel (around 200 HV). This high hardness significantly improves tool and component wear resistance. In practical applications, PVD-coated cutting tools can extend lifespan by 3 – 5 times, reducing wear rates by 70% when machining high-strength materials.
- Excellent Adhesion: PVD coatings bond strongly with substrates, typically achieving over 50 N in scratch and pull-off tests. This strong adhesion ensures stable performance under high stress, preventing peeling. For example, PVD coatings on automotive engine piston rings significantly enhance durability.
- Environmental Friendliness: Unlike traditional electroplating, PVD involves no harmful chemicals and offers high material utilization, reducing waste. This makes it ideal for environmentally and health-sensitive fields like medical devices and food processing equipment. For instance, PVD coatings are widely used in surgical instruments and implants due to their biocompatibility and eco-friendliness.
- Uniformity and Precision: PVD technology can form uniform coatings on complex-shaped workpieces. Precise control of process parameters (like vacuum level, deposition rate, and substrate temperature) allows accurate adjustment of coating thickness and performance. For example, PVD coatings on aerospace components ensure uniformity and performance consistency.
- Diverse Material Options: PVD technology works with various coating materials like titanium nitride (TiN), titanium carbide (TiC), and diamond-like carbon (DLC), meeting diverse application needs. For instance, DLC coatings are widely used in automotive engine parts and electronic devices due to their low friction and high wear resistance.
Limitations of PVD Technology
Despite its advantages, PVD technology has some limitations:
- High Equipment Costs: PVD equipment requires high vacuum and complex control systems, leading to higher costs. For example, sputtering and ion plating equipment costs far exceed traditional electroplating, posing a financial burden for small and medium-sized enterprises.
- Process Complexity: PVD technology demands precise control of parameters like vacuum level, target purity, deposition rate, and substrate temperature, increasing operational difficulty and production costs. For instance, improper parameter control in an automotive parts project led to unstable coating quality and higher costs.
- Coating Thickness Limitations: PVD coatings are typically thin (usually a few microns). Excessive thickness can increase internal stress, affecting adhesion. For example, in high-wear applications, thin coatings may offer insufficient protection, requiring additional surface treatments.
- High Substrate Requirements: PVD technology requires substrates with good surface quality and chemical composition. For example, substrates must be clean and oxide-free; otherwise, coating adhesion and uniformity may suffer. In one project, improper substrate treatment caused local peeling, reducing product yield.
- Limited Application Scope: PVD technology is better suited for small-batch, high-value precision components. For high-volume, low-cost products, it may not be economically viable. For example, traditional electroplating remains more cost-effective for low-cost consumer goods.
PVD vs. Traditional Technologies
Feature | PVD Technology | Traditional Electroplating |
---|---|---|
Environmental Friendliness | No pollution, no harmful chemicals | May produce harmful waste and emissions |
Adhesion | High (typically > 50 N) | Lower (typically < 30 N) |
Coating Uniformity | High, suitable for complex shapes | Lower, suitable for simple shapes |
Equipment Costs | High | Low |
Process Complexity | High, requires precise parameter control | Low, relatively simple process |
Coating Thickness | Thin (typically < 10 microns) | Thicker (up to tens of microns) |
Application Scope | High-value, precision components | Low-cost, high-volume products |
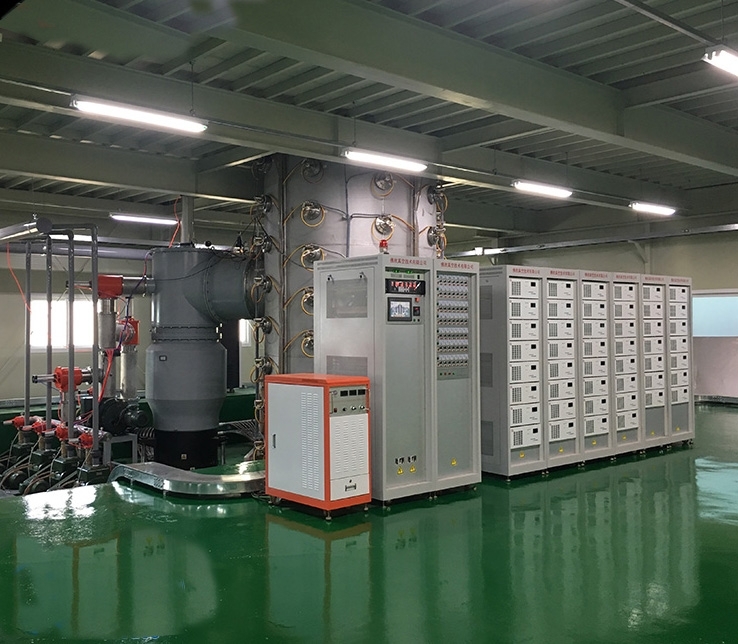
Quality Control and Testing
The quality of PVD (Physical Vapor Deposition) coatings directly affects their performance and application effectiveness. To ensure coatings meet design requirements, key indicators like thickness, adhesion, hardness, wear resistance, and corrosion resistance must be strictly controlled and tested. Here’s a detailed analysis of PVD coating quality control and testing.
Key Quality Control Indicators
PVD coating quality control focuses on the following key indicators:
- Coating Thickness: Thickness is crucial for performance. Too thin may offer insufficient protection; too thick may increase internal stress, affecting adhesion. Typically, PVD coatings are a few microns thick.
- Adhesion: Adhesion between the coating and substrate directly determines durability. Poor adhesion can cause peeling, affecting component lifespan.
- Hardness: Coating hardness is a key indicator of wear and scratch resistance. High hardness extends tool and component lifespan.
- Wear Resistance: Wear resistance determines performance under friction and wear conditions, directly affecting component durability.
- Corrosion Resistance: Corrosion resistance determines performance in corrosive environments, crucial for components used in harsh conditions.
Testing Methods and Techniques
To ensure PVD coating quality, various testing methods and techniques are used:
- Thickness Measurement:
- X-ray Fluorescence (XRF): Measures characteristic X-rays of coating materials to calculate thickness.
- Scanning Electron Microscopy (SEM): Uses high-resolution imaging to directly observe coating thickness.
- Profilometer: Measures height difference between coating and substrate to calculate thickness.
- Adhesion Testing:
- Scratch Testing: Uses a scratch tester to apply increasing loads to the coating surface, observing the critical load at which peeling occurs.
- Pull-off Testing: Uses a pull-off tester to measure the force required to separate the coating from the substrate.
- Hardness Testing:
- Microhardness Testing: Uses a microhardness tester to apply small loads to the coating surface, measuring indentation size to calculate hardness.
- Nanoindentation Testing: Uses a nanoindenter to apply nano-level loads, measuring indentation depth to calculate hardness.
- Wear Resistance Testing:
- Friction and Wear Testing: Uses a friction and wear tester to simulate actual working conditions, measuring wear rate.
- Sandpaper Wear Testing: Uses sandpaper to abrade the coating surface, measuring wear amount.
- Corrosion Resistance Testing:
- Salt Spray Testing: Places coating samples in a salt spray environment to observe corrosion.
- Electrochemical Testing: Uses an electrochemical workstation to measure corrosion potential and current, assessing corrosion resistance.
Key Quality Control Factors
PVD coating quality is influenced by the following key factors:
- Process Parameters: Vacuum level, deposition rate, and substrate temperature directly affect coating quality and performance. For example, insufficient vacuum can lead to gas inclusion, affecting density and adhesion.
- Target Purity: Higher target purity ensures stable coating performance. Impurities can cause defects, affecting performance.
- Substrate Surface Treatment: Substrate surface cleanliness and roughness directly affect coating adhesion and uniformity. Untreated surfaces can reduce adhesion.
- Coating Material Selection: Different materials vary in hardness, wear resistance, and corrosion resistance. Selecting the right material for specific applications is crucial for coating quality.
Frequently Asked Questions
1. How long does a PVD coating last?
The lifespan of a PVD coating depends on factors like coating material, substrate properties, usage environment, and process parameters. For example, titanium nitride (TiN) coatings on cutting tools typically extend lifespan by 3 – 5 times, but in high-wear or corrosive environments, lifespan may shorten. Optimizing coating thickness, adhesion, and other parameters can further extend lifespan.
2. Is PVD coating suitable for all materials?
PVD coating has high substrate requirements and is mainly suitable for metals, ceramics, and some plastics. Substrate surface quality and chemical composition directly affect coating adhesion and uniformity. For example, substrates must be clean and oxide-free; otherwise, adhesion may suffer. For some special materials (like certain polymers), surface treatment or alternative coating technologies may be needed.
3. How to choose the right PVD coating process?
Choosing the right PVD coating process involves considering the following factors:
- Application Needs: Select coating materials and processes based on usage environment (e.g., high wear, corrosion, or temperature). For example, TiN is suitable for cutting tools and molds, while DLC is ideal for automotive parts and medical devices.
- Substrate Properties: Select process parameters based on substrate hardness, surface roughness, and chemical composition. For example, sputtering is better for complex shapes than evaporation.
- Cost-effectiveness: Choose processes based on production scale and budget. For example, PVD is ideal for small-batch, high-value precision components, while traditional electroplating may be more cost-effective for high-volume, low-cost products.
4. What are the advantages of PVD coating over traditional electroplating?
PVD coating offers the following advantages over traditional electroplating:
- Environmental Friendliness: PVD involves no harmful chemicals, reducing environmental pollution.
- Strong Adhesion: PVD coatings bond strongly with substrates, preventing peeling.
- High Uniformity: PVD can form uniform coatings on complex shapes.
- Diverse Material Options: PVD works with various materials like TiN, TiC, and DLC, meeting diverse application needs.
5. How is PVD coating thickness controlled?
PVD coating thickness is typically controlled by adjusting the deposition rate and deposition time. Common methods for measuring thickness include:
- X-ray Fluorescence (XRF): Measures the characteristic X-rays emitted by the coating material to calculate thickness.
- Scanning Electron Microscopy (SEM): Provides high-resolution imaging to directly observe and measure coating thickness.
- Profilometer: Measures the height difference between the coating and substrate to determine thickness.
By precisely controlling process parameters like vacuum level, deposition rate, and substrate temperature, manufacturers can achieve accurate and uniform coating thickness. For example, in high-precision applications, coating thickness is often controlled to within a few microns to ensure performance consistency.
6. How does PVD coating perform in high-temperature environments?
The performance of PVD coatings in high-temperature environments depends on the coating material. For example:
- Titanium Aluminum Nitride (TiAlN): Known for its high hardness and oxidation resistance, TiAlN coatings can maintain excellent performance at temperatures above 800°C, making them ideal for high-temperature cutting tools and aerospace components.
- Titanium Nitride (TiN): While TiN coatings are highly durable, their performance may degrade at extremely high temperatures.
When selecting a PVD coating for high-temperature applications, it’s essential to consider the specific material properties and the operating environment.