How to Choose the Right PVD Coating Equipment
Selecting the right vacuum coating equipment is crucial for optimizing production and product quality. Whether you need PVD coating, multi-arc ion coating, large-scale vacuum coating, or magnetron sputtering coating, each type has unique strengths. Let’s explore the best options for your industry.
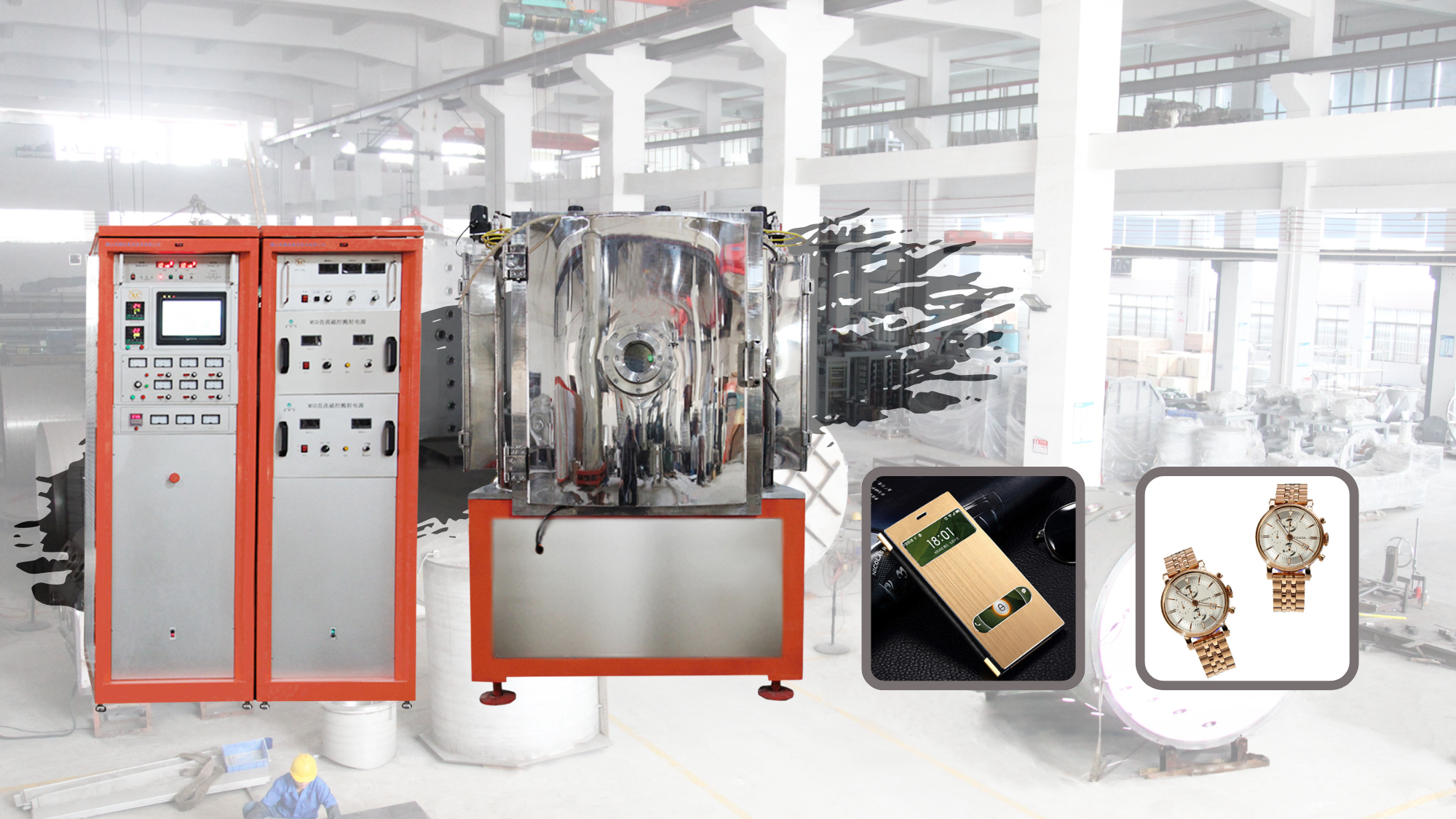
1.Multi-Arc Ion Coating Machine
This machine is perfect for industries that need durable, high-adhesion coatings. It’s widely used for tools, molds, and automotive parts like piston rings, where wear resistance is critical. The coating thickness ranges from 1 to 4 microns, with a hardness of up to 3000 HV.
2.Large-Scale Vacuum Coating Machine
If you’re working with oversized components like architectural glass or solar panels, this machine is a must. It handles substrates up to 3 meters long and ensures a uniform coating with a thickness accuracy of ±0.1 microns. It’s ideal for the construction and renewable energy sectors.
3.Magnetron Sputtering Coating Machine
Known for its precision, this versatile PVD coating method deposits metals, alloys, and ceramics. It’s a top choice for the electronics industry, used for semiconductors, displays, and optical components. With a deposition rate of 0.1 to 10 nm/s, it offers excellent control over film thickness and composition.
4.PVD Coating for Tableware and Kitchenware
PVD coating enhances both the durability and aesthetics of cutlery and cookware. Coatings like titanium nitride (TiN) provide scratch resistance, corrosion resistance, and a gold-like finish. The typical coating thickness is 0.5 to 2 microns, ensuring long-lasting performance.
5.PVD Coating for Tableware and Kitchenware
This technology is a game-changer for the hardware industry. It creates visually appealing finishes like gold, rose gold, or black chrome on door handles, faucets, and other decorative items. The coating thickness ranges from 0.3 to 1.5 microns, offering both beauty and durability.
Key Considerations:
- Industry Needs: Focus on wear resistance, aesthetics, or large-scale production.
- Coating Material: Choose machines optimized for materials like TiN, CrN, or DLC.
- Substrate Size: Ensure the equipment can handle your component dimensions.
- Precision: Look for machines with accurate thickness control and deposition rates.
- Energy Efficiency: Modern machines are designed to reduce operational costs.
Choosing the right vacuum coating equipment depends on your specific industry and product requirements. Whether you need multi-arc ion coating for industrial tools, large-scale coating for architectural glass, or decorative PVD coating for hardware, understanding each technology’s strengths is key. By investing in the right equipment, you can enhance product quality, improve efficiency, and stay competitive.
Explore our advanced PVD coating solutions tailored to your needs.