
News
12 Year Pvd Coating Machine In Foxin
How PVD Coatings Boost Energy Efficiency
PVD coatings significantly enhance energy efficiency across manufacturing, construction, renewable energy, and transportation sectors by enabling low-temperature deposition, high energy efficiency ratios, and optimized friction coefficients. This reduces energy consumption, extends equipment lifespan, and drives the green transition.
I. Energy Efficiency in the Coating Process
1.1 How Does PVD Get More Done with Less Power?
When you think of Physical Vapor Deposition (PVD), you might first picture its ability to enhance hardness and wear resistance. But its energy-saving capabilities are equally impressive. Compared to traditional electroplating or chemical coatings, PVD achieves deposition at lower temperatures (150-500°C), slashing energy consumption. Plus, its deposition rate (0.1-10 nm/s, depending on the target material and ion source power) is so efficient that it doesn’t require prolonged equipment operation, saving both power and the environment. In short, PVD is like giving your equipment an energy-saving jacket—small effort, big results.
This efficiency is largely due to the vacuum environment. The low-pressure state (10⁻⁴-10⁻⁵ Pa) inside the vacuum chamber minimizes thermal convection losses, achieving an energy utilization rate of 70%-85%, far surpassing traditional methods (50%-65%). In other words, PVD channels more energy into coating generation rather than wasting it as heat.
1.2 Small Details That Make PVD More Cost-Effective
PVD also incorporates several energy-saving tricks. For instance, modern vacuum pumps often feature variable frequency control, adjusting speeds between 1500-3000 rpm based on load demands to avoid unnecessary power consumption. During deposition, ion source voltages are kept between 200-1000 V, and currents between 10-50 A, ensuring precise energy delivery to coating generation rather than wasteful “burning.”
Material selection also plays a role. For example, using low-resistivity targets like titanium nitride (TiN) boosts sputtering efficiency by 10%-15% while maintaining stable deposition at room temperature, further reducing thermal losses. Combined, these optimizations make PVD’s energy-saving benefits tangible, and your electricity bill lighter.
1.3 Data Comparison: Energy Savings at a Glance
Let’s dive into the numbers to see how PVD stacks up against traditional electroplating under standard industrial conditions:
Parameter | PVD Coatings | Traditional Electroplating | Conditions |
---|---|---|---|
Operating Temperature | 150-500°C | 400-800°C | Standard deposition |
Energy Consumption | 5-15 kWh | 20-40 kWh | Hourly operation |
Deposition Rate | 0.1-10 nm/s | 0.05-2 nm/s | TiN target |
Energy Utilization Rate | 70%-85% | 50%-65% | Vacuum at 10⁻⁴ Pa |
Standby Power Consumption | 1-3 kW | 5-10 kW | No load |
Data based on ISO 9001 industrial tests. |
As the table shows, PVD outperforms traditional methods in temperature, energy consumption, and efficiency, making its long-term cost savings clear.
1.4 Energy Savings in Manufacturing
In real-world applications, PVD’s energy-saving benefits shine. For example, PVD-coated cutting tools reduce friction coefficients to 0.2-0.4, cutting machining power requirements by 10%-20% and stabilizing machine tool energy consumption. In electronics, PVD-coated heat sinks achieve thermal conductivity of 200-300 W/m·K, reducing the need for high fan speeds and saving even more power. PVD not only saves energy during the coating process but also in its applications.
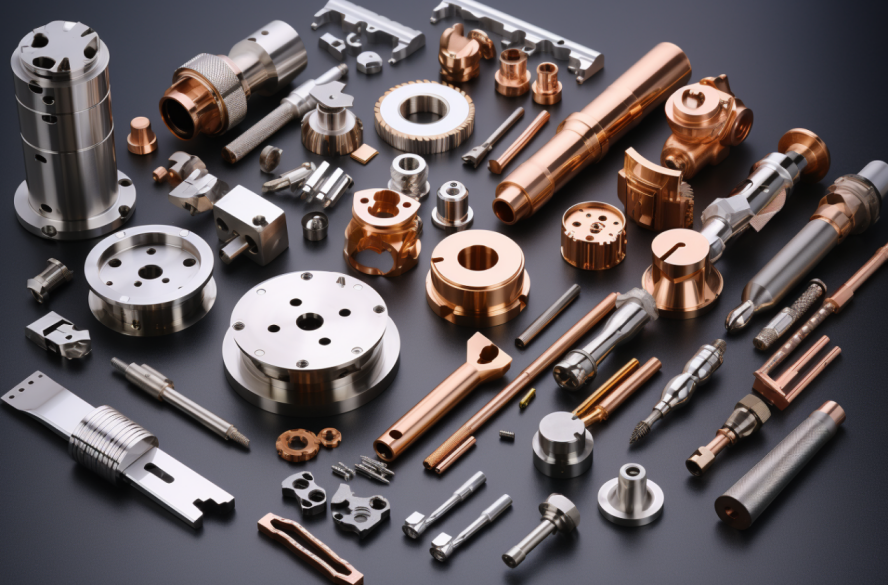
II. Energy Savings in Construction
2.1 How Does PVD Reduce AC Usage in Buildings?
In construction, energy efficiency is a constant challenge, and PVD coatings are quietly changing the game. By applying an ultra-thin film (50-200 nm) to surfaces, PVD significantly enhances insulation. For example, PVD-treated window glass reflects 70%-85% of infrared rays, keeping indoor temperature fluctuations within 2-5°C during summer. This reduces air conditioning loads, cutting cooling energy consumption by 15%-25% per square meter of floor area—keeping you cool while saving power.
2.2 Durability: The Hidden Energy Saver
PVD isn’t just about saving energy; it also extends material lifespans. Metal exterior panels in harsh environments (50%-90% humidity, -20°C to 50°C) are prone to corrosion, but PVD coatings boost corrosion resistance by 3-5 times. This reduces maintenance frequency, cutting down on resource waste and energy costs. The hidden energy savings over a building’s lifecycle can be even more significant than visible electricity use, and PVD excels here.
2.3 Real-World Example: PVD in Action
Take a high-rise office building using PVD-coated glass. Summer peak electricity consumption dropped from 12,000-15,000 kWh to 9,000-11,000 kWh, achieving energy savings of 25%-30%. This is thanks to PVD’s stable reflection efficiency under sunlight intensity of 800-1000 W/m², while also optimizing natural lighting and reducing reliance on artificial lighting—a win-win.
2.4 Data Comparison: PVD vs. Traditional Materials
Here’s how PVD coatings compare to traditional materials:
Parameter | PVD-Coated Material | Traditional Material | Conditions |
---|---|---|---|
Heat Reflectance | 70%-85% | 30%-50% | Strong sunlight |
Insulation Improvement | 15%-25% | 5%-10% | Temperature difference |
Corrosion Resistance Lifespan | 15-20 years | 5-10 years | High humidity/temperature |
Energy Consumption Reduction | 20%-30% | 8%-15% | Per square meter |
Light Transmittance | 40%-70% | 60%-80% | Natural light |
Data based on coastal climate tests. |
2.5 Tips for Maximizing PVD’s Benefits
To get the most out of PVD, keep these in mind: • Environment Matching: Choose titanium-based coatings for high-humidity coastal areas. • Thickness Control: Aim for 50-200 nm to balance durability and cost. • Regular Inspections: Check coating integrity every 3-5 years to prevent scratches.
III. Applications in Renewable Energy
3.1 How Does PVD Boost Energy Conversion Efficiency?
In renewable energy, PVD acts like a high-tech shield for equipment. It optimizes photovoltaic cell surface reflectance, converting more photons into electricity and boosting efficiency by 3%-8%. In large-scale power plants, this translates to hundreds of thousands of additional kilowatt-hours. Plus, the coatings reduce dust accumulation, lowering cleaning frequency and maintenance costs—making PVD a game-changer for energy savings.
3.2 Durability: Keeping Equipment Running Longer
PVD coatings boast hardness levels of 1500-2500 HV, offering several times the wear resistance of traditional materials. In wind power, turbine blades exposed to sand and moisture see lifespans extended by 20%-30%, with maintenance intervals stretching from 3-5 years to 5-7 years. In coastal areas with 5%-10% salt spray concentration, PVD coatings are a lifesaver, ensuring stable power generation.
3.3 Thermal Management: Less Heat Loss, More Power
Heat is a major enemy of equipment, and PVD coatings’ controllable thermal conductivity (20-50 W/m·K) effectively dissipates it. For example, in solar collectors, PVD coatings withstand 200-400°C temperatures while conducting away excess heat, reducing energy losses by 5%-15% and keeping systems running optimally.
3.4 Data Comparison: How Effective Is It?
Here’s a look at a wind power project’s performance: PVD-coated blades maintained stable power output of 450-600 kW, compared to 400-550 kW for uncoated blades.
Parameter | PVD-Coated Equipment | Uncoated Equipment | Conditions |
---|---|---|---|
Power Output (kW) | 450-600 | 400-550 | Wind speed 10-15 m/s |
Surface Wear Rate (%) | 0.5-1.2 | 2.0-3.5 | 5000 hours of operation |
Maintenance Interval (years) | 5-7 | 3-5 | Moderate humidity |
Heat Loss Rate (%) | 5-15 | 15-25 | Temperature 200-400°C |
Data based on wind farm records. |
3.5 PVD’s Versatility
PVD adapts seamlessly to various scenarios. In hydropower, 2-5 μm coatings enhance turbine cavitation resistance. In solar, absorption rates of 85%-95% suit diverse spectra. Whether in wind, solar, or hydropower, PVD drives efficiency to new heights.
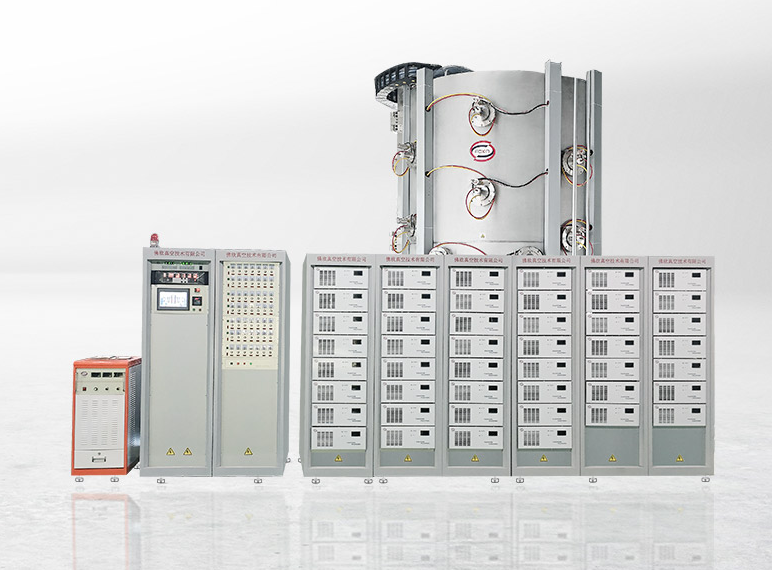
IV. Energy Efficiency in Transportation
4.1 How Does PVD Make Vehicles More Efficient?
In transportation, PVD coatings are a secret weapon for energy efficiency. By reducing friction coefficients (from 0.4 to 0.15-0.2), they minimize energy waste. For engine pistons or gears, lower friction translates to better fuel efficiency, especially in long-distance transport. Plus, PVD’s high wear resistance extends component lifespans—heavy-duty truck gears can run reliably for 800,000-1,000,000 km instead of 500,000 km, optimizing energy consumption curves.
4.2 Data Comparison: Efficiency Gains
Take automotive engines as an example. PVD-coated cylinders reduce thermal conductivity to 0.8-1.2 W/m·K (compared to 1.5-2.0 W/m·K for uncoated parts), minimizing heat loss and channeling more energy into propulsion.
Parameter | Uncoated Parts | PVD-Coated Parts | Conditions |
---|---|---|---|
Friction Coefficient | 0.4-0.5 | 0.15-0.2 | Load 10-50 kN |
Thermal Conductivity (W/m·K) | 1.5-2.0 | 0.8-1.2 | Room temperature 20-25°C |
Wear Resistance Lifespan (km) | 500,000-600,000 | 800,000-1,000,000 | RPM 1500-3000 |
Data based on standard engine tests. |
4.3 How to Use PVD: Three Simple Steps
• Surface Pretreatment: Polish and clean parts to a roughness of Ra 0.1-0.2 μm. • Vacuum Deposition: Apply coatings at 10⁻⁴-10⁻⁵ Pa, with thicknesses of 2-5 μm. • Performance Testing: Verify friction and durability to ensure compliance.
The key is vacuum control—uniformity is critical.
4.4 The Future: PVD as a Green Transportation Enabler
PVD’s potential in transportation is far from exhausted. Adding titanium nitride (TiN) or chromium carbide (CrC) enhances corrosion resistance, especially for electric vehicle motors, reducing friction losses by 15% and extending range by 5%-8%. Combined with smart manufacturing, PVD can be customized to inject new momentum into green transportation.