PVD Coating Machine vs. CVD: Which Thin Film Tech Wins?
In today’s manufacturing world, thin film technology is revolutionizing the game, with PVD and CVD as the top contenders. Each shines in its own way, but which one’s your MVP? We’ve dissected their working principles, process conditions, applications, and pros and cons. Ultimately, a PVD coating machine stands out for precision needs, while CVD takes the crown for industrial scale—choose what fits your bill!
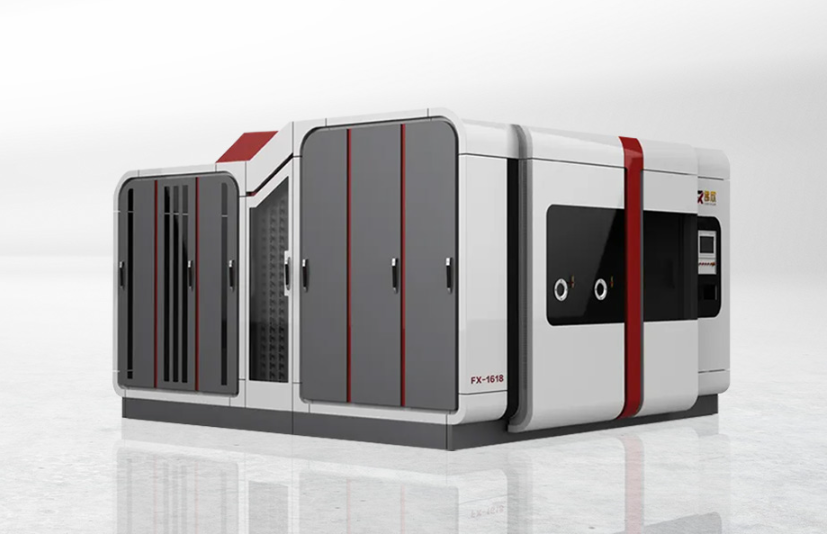
How They Work: Physical vs. Chemical Showdowns
PVD: The Physical Hauler
PVD—short for Physical Vapor Deposition—is all about moving material the old-school, physical way. It takes a solid, turns it into a gas, and slaps it onto a surface. No fancy chemistry here, just pure elbow grease. The main PVD tricks? Evaporation and sputtering.
- Evaporation: Picture this: in a high-vacuum setup, you heat the material until it vaporizes. That vapor floats over to your surface like a misty cloud and cools into a film. Simple, straightforward, and perfect for low-melting-point stuff.
- Sputtering: Here, high-energy particles (think argon ions) slam into a target, knocking atoms loose. Those atoms then settle onto your surface. Sputtering handles high-melting-point materials like a champ and delivers top-notch film quality.
PVD’s all about “keeping it physical”—no chemical reactions, just clean, pure films with minimal mess. Think of it as a “neat-freak mover” who gets the job done without trashing the place.
CVD: The Chemical Wizard
CVD—Chemical Vapor Deposition—takes a different route. It’s a chemical magic show where gases react to form a solid film right on your surface. Heat or plasma kicks things off, breaking down or mixing the gases into a slick coating. You’ve got classics like thermal CVD and plasma-enhanced CVD (PECVD).
- Thermal CVD: Crank up the heat, and the gases break apart to form a film. It’s great for high-temp materials like ceramics or silicon wafers.
- PECVD: Plasma juices up the gases, dropping the temp needed for the reaction. This makes it a go-to for heat-sensitive stuff, widening CVD’s playbook.
CVD’s all about “gas-phase wizardry”—it can whip up complex compound films and coat tricky shapes like nobody’s business. In short, it’s the “do-it-all magician” of the coating world.
Process Conditions: Low-Temp Precision vs. High-Temp Power
PVD: Cool, Calm, and Precise
PVD loves a vacuum—keeps pesky gases out of the way for ultra-pure, even films. It runs cool, usually between 100-300°C, making it a solid pick for heat-sensitive materials like plastics or certain alloys. Downside? It’s slow—think 0.1-10 microns per hour. Perfect for high-precision, high-quality jobs.
- Cost: PVD machines aren’t cheap. You’re paying for that high-vacuum system and fancy target materials.
- Materials: Metals, alloys, plastics—PVD’s got you covered. But it struggles with super high-melting-point stuff.
PVD’s like an “artsy craftsman”—takes its sweet time but delivers a masterpiece.
CVD: Hot, Fast, and Furious
CVD can work at normal or low pressure, but it’s picky about gas control and loves heat—think 500-1000°C. That rules out heat-sensitive materials, but it’s lightning-fast, pumping out 1-100 microns per hour. Great for big production runs.
- Cost: CVD gear is cheaper upfront, but you’ll need a slick gas control system and heaters that can take the heat.
- Materials: Ceramics, silicon wafers, high-temp composites—CVD’s in its element here.
CVD’s your “high-speed factory”—tough conditions, but it churns out results like a boss.
Where They Shine: Decor vs. Industry
PVD: Style Meets Precision
PVD kills it in decorative coatings and precision tool coatings.
- Decorative Coatings: Watches, jewelry, phone cases—PVD delivers glossy, wear-resistant finishes that pop.
- Tool Coatings: Cutting tools and molds get a hardness boost and longer life with PVD films.
- Optical Films: Lenses and filters love PVD for its clarity and uniformity.
PVD’s your “jack-of-all-trades”—making your watch bling and your tools last.
CVD: The Industrial Beast
CVD rules the roost in semiconductors and tough, wear-resistant coatings.
- Semiconductors: Think insulation and conductive layers for silicon wafers and transistors.
- Wear & Corrosion Resistance: Engine blades and turbines lean on CVD for heat and corrosion protection.
- Ceramics & Composites: Silicon carbide, silicon nitride—CVD churns out high-melting-point magic.
CVD’s the “industrial king”—from chips to jet engines, it’s got the heavy lifting covered.
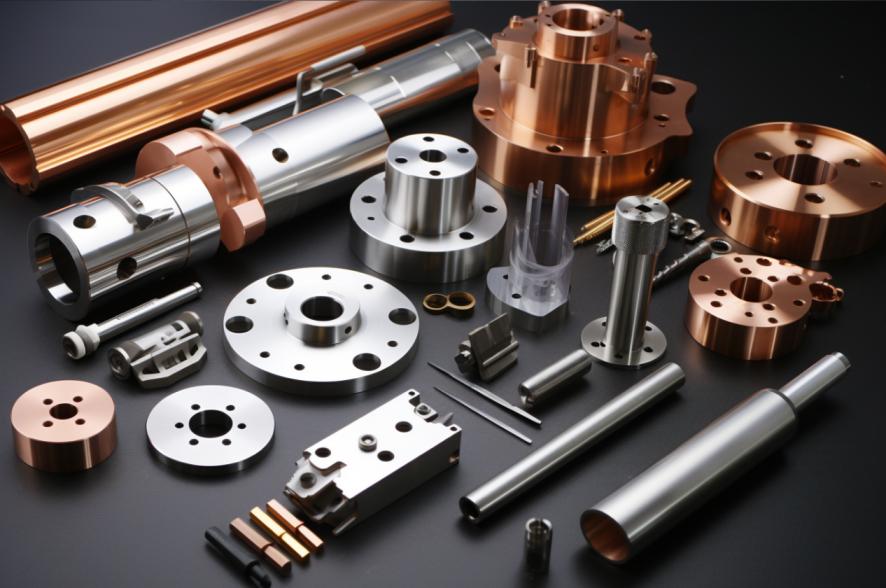
Pros & Cons: Strengths and Weaknesses
PVD: The Good and the Bad
- Pros:
- Super pure films—no chemical muck to mess things up.
- Low temps—great for plastics and alloys.
- Pinpoint precision—uniform films with less than 1% thickness variation.
- Eco-friendly—no chemical reactions, less pollution.
- Cons:
- Weak coverage—flat or simple surfaces only.
- Slow as molasses—2 hours for a 5-micron film.
- Pricey gear—high-end PVD machines hit the wallet hard.
- Material limits—struggles with high-melting-point stuff.
CVD: The Ups and Downs
- Pros:
- Killer coverage—coats nanoscale grooves like a pro.
- Fast—100 microns in an hour? No sweat.
- Versatile—whips up complex stuff like silicon nitride or tungsten carbide.
- Production-ready—high efficiency, low per-unit cost.
- Cons:
- High heat—only for materials that can take it.
- Safety risks—gases like silane can go boom if mishandled.
- Less pure—unreacted gas bits can sneak in.
- Running costs—guzzles gas and energy.
The Final Showdown
Comparison | PVD | CVD |
---|---|---|
Core Principle | Physical (target sputtering) | Chemical (gas reactions) |
Process Temp | 100–300°C | 500–1000°C |
Deposition Rate | 0.1–10 microns/hour | 1–100 microns/hour |
Best Materials | Metals, alloys, plastics | Ceramics, silicon, composites |
Long-Term Cost | High (vacuum, target upkeep) | High (gas, energy use) |
Top Uses | Luxury goods, tools, optics | Semiconductors, aerospace |
Conclusion
If you’re into blingy luxury goods or precision tools, a PVD coating machine’s your best bet. But if semiconductors or aerospace parts are your gig, CVD’s speed and coverage will steal the show.