Rainbow PVD Coating: Top Stainless Steel Finish
- Introduction to Rainbow PVD Coating
- The Perfect Partner for Stainless Steel
- Technology and Performance Highlights
- Comparison to Other Finishes
- Usage and Maintenance
1. Introduction to Rainbow PVD Coating
1.1 How PVD Technology Works
PVD, short for Physical Vapor Deposition, is a cutting-edge method that uses vacuum technology to deposit metal onto stainless steel surfaces. The process is straightforward. Inside a sealed PVD coating machine, metals like titanium or chromium are either heated into a gas through thermal evaporation or blasted onto the surface using magnetron sputtering. Take stainless steel cutlery, for instance: it’s often processed this way. The result? A super-thin yet incredibly tough coating that bonds tightly to the steel.
Unlike traditional electroplating machines, PVD has some serious advantages. It skips chemical reactions entirely, producing no waste liquid, which makes it eco-friendly and safe. PVD coating machines also allow precise control over thickness, down to the nanometer level, creating a durable stainless steel finish. This metallization process boosts surface hardness, making it scratch-resistant and highly practical. Run a key lightly across it, and you won’t see a mark. The coating is even, with excellent adhesion.
1.2 Where the Rainbow Effect Comes From
The dazzling, multicolored sheen of rainbow PVD coating is its standout feature, and it all comes down to optics. During the PVD coating process, thin layers of metal coatings, like titanium or gold, are stacked onto stainless steel. When light hits the surface, it reflects and refracts. The interaction of different wavelengths of light creates that rainbow effect, kind of like what you see with soap bubbles. You can go for a gold PVD coating for a luxurious vibe or opt for cooler tones to match a modern aesthetic.
This isn’t something you can achieve with a simple paint job. The PVD (Physical Vapor Deposition) process relies on specialized machines that precisely control the thickness and materials of the coating, ensuring the colors come out smooth and consistent. Rainbow PVD coating isn’t just for show either; it’s popping up everywhere, from kitchen gadgets to architectural decor. Beyond looking cool, it’s super practical. It’s wear-resistant, corrosion-resistant, and way tougher than your average metal coating. Wondering if the color fades? Nope, not a chance. The vacuum coating technology locks that layer in tight, keeping it shiny and vibrant even after years of use.
With its eye-catching, multicolored glow and top-notch durability, it’s no surprise rainbow PVD coating stands out among stainless steel finishes. Whether it’s for home use or commercial projects, it makes stainless steel tougher and adds serious style points.
2. The Perfect Partner for Stainless Steel
2.1 Why Choose Rainbow PVD Coating
Stainless steel is already a solid choice due to its strength, but when paired with rainbow PVD coating, it becomes a versatile champion that excels in both performance and looks. This coating is applied through vacuum technology, offering greater durability than traditional metal plating. While regular coatings might wear down or lose their shine over time, the exceptional hardness of vacuum coating stands up to scratches and daily use effortlessly. For example, a bathroom hook exposed to wet towels every day can still look flawless.
Its corrosion resistance is another major plus. Whether it’s constant moisture or salty air, rainbow PVD coating keeps stainless steel rust-free and polished. Compared to standard metal coatings, it provides better defense against environmental damage, making it perfect for applications that demand long-term durability. On the aesthetic side, its multicolored sheen adds a stylish edge. With a gleam reminiscent of gold plating, it can make anything from kitchen utensils to commercial decor feel more upscale and refined.
When it comes to cost, a PVD coating machine may carry a higher price tag than spray methods, but the benefits are worth it. The extended lifespan and lasting finish deliver excellent value over time. One upfront investment can keep things looking great for years, sparing you the hassle of frequent replacements or maintenance. Combining stainless steel with this technology offers a practical and appealing option that’s hard to beat.
2.2 Where It Shines
So, where does rainbow PVD coating fit in? Just about anywhere. In the kitchen, you’ll spot it on PVD-processed knives, sinks, and cookware. The sputter deposition technique gives them a glossy finish that’s not only attractive but also resistant to grease and scratches. Picture a frying pan still shining like new after six months of regular cooking.
Outside the kitchen, it’s a favorite in architectural design. Stainless steel facades and railings treated with rainbow PVD coating resist corrosion while lending a modern touch to spaces. For instance, a luxury hotel in Dubai uses this coating on its exterior walls to endure desert heat while turning heads with its brilliance. Coastal yard fences also hold up against salty sea air, staying vibrant for years.
At home, it boosts the durability and charm of dinnerware. In a hotel lobby, it elevates decor with a luxurious vibe. Vacuum technology even allows for color customization. Whether you prefer the cool tones of rhodium plating or the warm hues of gold electroplating, it can match any style. From installing a sleek bathroom faucet to adding unique flair to commercial buildings, the gold-coated effect grabs attention every time. From everyday items to high-end designs, rainbow PVD coating proves it’s up to the task.
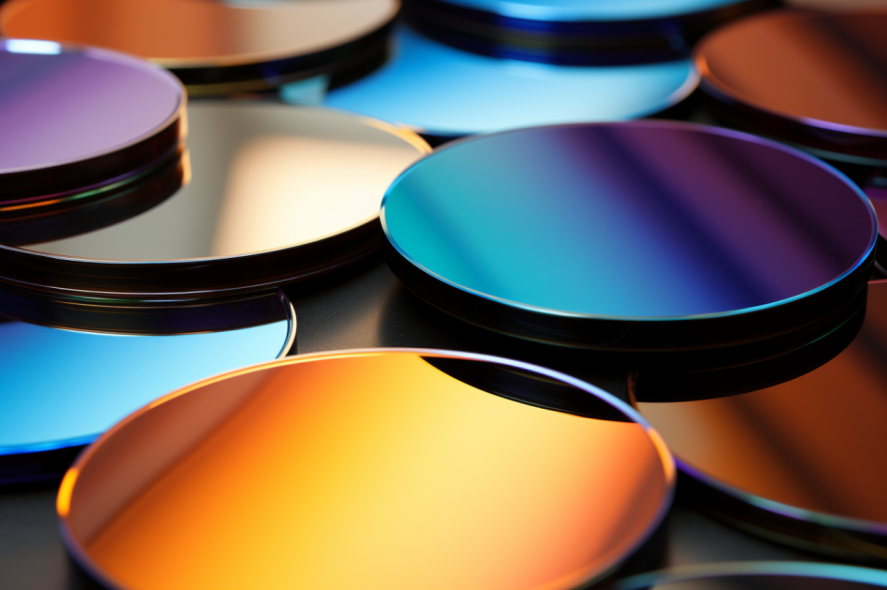
3. Technology and Performance Highlights
3.1 Manufacturing Process
The quality of rainbow PVD coating stems from a precise manufacturing process. At the heart of it is the PVD machine, which operates in a sealed chamber supported by vacuum technology to keep out dust and moisture. Metals like titanium are broken down into tiny particles through sputtering at high temperatures and then evenly deposited onto stainless steel. This creates a tough layer less than 0.1 microns thick. DC sputtering works great for quickly coating cookware, while RF sputtering is ideal for complex alloys, ensuring a smooth finish that’s over 10 times more durable than traditional spray coatings. This process delivers strong adhesion, making it perfect for long-term use.
3.2 Wear Resistance, Corrosion Resistance, and High-Temperature Durability
- Wear Resistance: The metal coating produced by the PVD machine is 3 to 5 times harder than regular stainless steel, standing up to scratches from knives and everyday bumps. For example, a coated kitchen knife can chop veggies and meat daily for six months and still look smooth and shiny, unlike regular coatings that peel or chip. This durability saves you money on replacements over time.
- Corrosion Resistance: Whether it’s a humid kitchen or salty coastal air, rust isn’t an issue. Tests show that rainbow PVD coating can withstand 1,000 hours in a salt spray environment without corroding, making it a solid choice for coastal railings or marine parts.
- High-Temperature Durability: While typical gold electroplating starts to discolor above 200°C, this coating holds strong up to 400°C without warping. That makes it ideal for grill grates or industrial equipment.
3.3 Color and Shine
The standout feature of rainbow PVD coating is its vibrant, multi-colored shine. By tweaking the coating thickness, you can control the color: a 0.05-micron layer gives a golden hue, while 0.08 microns shifts to cooler tones, offering rainbow-like variety. Want a luxurious gold finish for your dinnerware or a sleek, cool tone for bathroom fixtures? It’s fully customizable.
This shine is built to last. Thanks to vacuum coating, the color bonds tightly to the surface, resisting 1,000 rubs without fading, far outpacing spray coatings. For instance, a ring stored in a jewelry box will still sparkle after a year. Plus, rainbow PVD coating offers custom color options, making it a stylish and practical pick for elevator panels, door handles, or architectural accents.
4. Comparing Surface Finishes
4.1 Traditional Electroplating vs. Rainbow PVD Coating
Traditional electroplating uses an electroplating machine to chemically bond a metal coating, like gold plating, onto stainless steel. This method has been around for ages and typically costs 20-30% less than rainbow PVD coating. However, when it comes to durability, it doesn’t hold a candle to rainbow PVD coating. In friction tests, electroplated coatings often wear out after fewer than 500 rubs, and in humid environments like bathrooms, rust can start creeping in within 1-2 years due to weaker adhesion.
Rainbow PVD coating, on the other hand, relies on a PVD machine and vacuum technology to deposit metal onto the surface, making it over three times harder than electroplating. It easily resists scratches and corrosion. For example, a PVD-coated sink still shines after three years, while an electroplated one might look patchy and worn. Electroplating may seem cheaper upfront at about $10 per square meter, but with yearly maintenance, the five-year cost could exceed $50. Rainbow PVD coating, priced at $15-20 per square meter, is a one-and-done deal, requiring no extra upkeep over five years. Visually, the single-tone gold of electroplating fades fast, while rainbow PVD coating’s multi-layered sheen stays vibrant for over five years. If you’re after a cost-effective, long-lasting stainless steel finish, PVD is the smarter pick.
Metric | Traditional Electroplating | Rainbow PVD Coating |
---|---|---|
Cost | ~$10 per square meter | $15-20 per square meter |
Wear Resistance | <500 rubs | >2000 rubs |
Corrosion Resistance | Rust possible in 1-2 years | 1000-hour salt spray test, no rust |
Maintenance Cost | ~$50 over 5 years | No extra cost over 5 years |
Appearance | Single-tone gold, fades | Multi-layered rainbow sheen, 5+ years fade-free |
4.2 Spray Coating vs. Rainbow PVD Coating
Spray coating involves using a spray gun to apply paint onto stainless steel, costing as little as $5 per square meter with endless color options. But compared to rainbow PVD coating, it’s no match in durability. In greasy, high-wear spots like kitchens, spray coatings can peel off in under six months, exposing the bare stainless steel underneath. Rainbow PVD coating, applied through sputter deposition, locks metal onto the surface and withstands over 2000 rubs in wear tests, dwarfing spray coating’s measly 300 rubs.
The gap widens with corrosion and heat resistance. Spray coatings might crack in humid conditions within three months and discolor in under an hour at 200°C. Rainbow PVD coating, thanks to vacuum coating technology, holds up in a 1000-hour salt spray test without rusting and stays stable at 400°C. For instance, a spray-coated stainless steel panel in a restaurant might need replacing in six months, while a PVD-coated one lasts three years without a hitch. Appearance-wise, spray coating’s flat, uniform gloss lacks pizzazz, while rainbow PVD coating’s dynamic, multi-layered shine brings a premium vibe, perfect for upscale commercial settings. If long-term performance and standout looks matter to you, PVD is the clear winner.
Metric | Spray Coating | Rainbow PVD Coating |
---|---|---|
Cost | ~$5 per square meter | $15-20 per square meter |
Wear Resistance | <300 rubs | >2000 rubs |
Corrosion Resistance | Cracks possible in 3 months | 1000-hour salt spray test, no rust |
Heat Resistance | Discolors in 1 hour at 200°C | Stable at 400°C |
Lifespan | Peels in 6 months (kitchen) | 3 years intact (restaurant) |
Appearance | Flat, uniform gloss | Dynamic, multi-layered rainbow sheen |
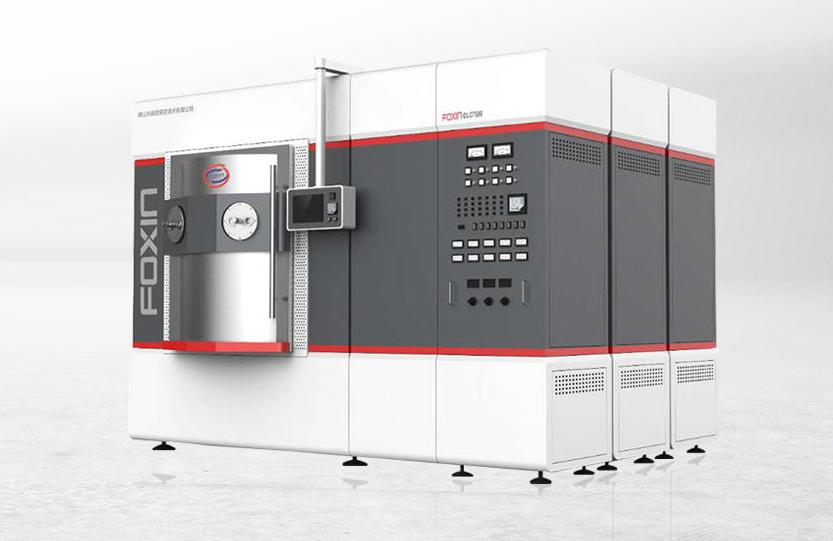
5. Use and Maintenance
5.1 Cleaning Tips
The surface of rainbow PVD coating is incredibly tough, thanks to its vacuum deposition technology. Grease and dust simply don’t stick to it. Keeping it shiny is a breeze, and with these quick, easy steps, you’ll have it sparkling in no time:
- Step 1: Gather Your Supplies Mix some mild soapy water, like dish soap with warm water, and grab a soft cloth or sponge. Skip the steel wool or rough scrubbers; they’ll scratch the metal coating and dull its shine.
- Step 2: Wipe Gently Dampen your cloth and lightly wipe away grease or fingerprints. For a PVD-treated kitchen sink, follow up with a dry cloth to banish water spots. The same goes for bathroom fixtures; a quick wipe keeps them spotless.
- Step 3: Avoid Harsh Chemicals and Force Steer clear of acidic cleaners like vinegar, bleach, or heavy-duty stain removers; they can damage the vacuum coating’s surface. For outdoor pieces like garden lights, a simple rinse with water handles dust just fine. No need for aggressive scrubbing.
For rainbow PVD coating on architectural features like elevator buttons, a occasional wipe with a damp cloth keeps them gleaming. This top-tier coating stays stunning for years with minimal effort, making upkeep both simple and effective.
5.2 Longevity and Versatility
Rainbow PVD coating is built to last. Thanks to its advanced process, it bonds tightly to metal, unlike gold plating that flakes off over time. With normal use, it can hold up for over a decade, resisting scratches and corrosion while saving you the cost of frequent replacements.
It’s also incredibly versatile. From everyday items to industrial applications, it shines anywhere. Kitchen pots that soak in water daily stay glossy, while outdoor mailboxes withstand years of sun without fading. In industrial settings, high-heat components coated with PVD outperform traditional coatings, resisting discoloration like champs. Even commercially, using rainbow PVD coating on storefront signs adds a touch of class. It’s a finish that adapts to any situation effortlessly.