Unlocking the Power: Stainless Steel Vacuum Coating Machine
The world of material science is constantly evolving, pushing the boundaries of innovation to deliver stronger, lighter, and more durable materials for countless applications. One such breakthrough that has truly revolutionized the industry is the stainless steel vacuum coating machine.
This game-changing technology not only enhances the properties of stainless steel but also enables new possibilities for its use across various sectors. In this blog, we’ll explore the inner workings of stainless steel vacuum coating machines, their benefits, and the numerous applications they serve.
Understanding Stainless Steel Vacuum Coating Machine
At the core of stainless steel vacuum coating technology is a process called Physical Vapor Deposition (PVD). This method involves vaporizing a material and then depositing it onto a substrate in the form of a thin film. PVD is conducted in a vacuum chamber, ensuring a controlled environment and minimizing contamination. This results in coatings with exceptional hardness, wear resistance, and corrosion protection.
Stainless steel vacuum coating machines utilize a variety of PVD techniques, including sputtering, evaporation, and ion plating. Each technique has its own unique advantages, making it suitable for specific applications and desired coating properties.
Stainless Steel Metal Parts Steel Titanium Pvd Deposit Machine for Sale
In the rapidly evolving world of material science, manufacturers are continually seeking ways to improve the durability and performance of their products. One such innovation is the Steel Titanium PVD Deposition Machine from Foxin Vacuum Technology, specifically designed for stainless steel metal parts.
This state-of-the-art equipment not only enhances the mechanical, chemical, and physical properties of stainless steel parts but also ensures their increased durability, corrosion resistance, and overall performance.
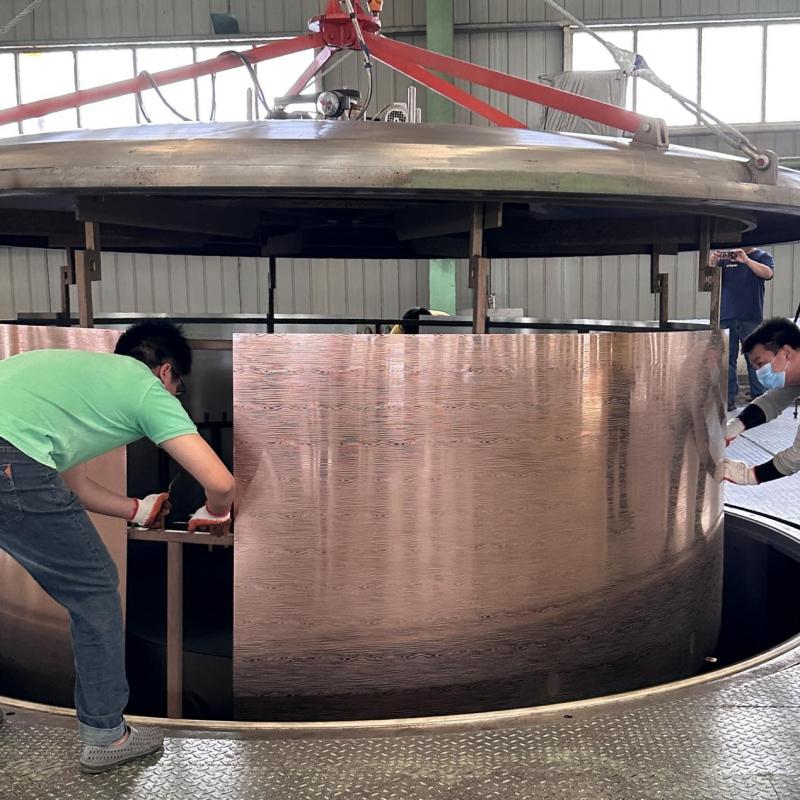
Purpose of the Steel Titanium PVD Deposition Machine
The primary purpose of the Steel Titanium PVD Deposition Machine is to coat a layer of titanium film onto stainless steel metal parts. This process significantly improves the properties of stainless steel parts, making them more durable, and corrosion-resistant, and enhancing their overall performance. Industries such as automotive, aerospace, electronics, and consumer goods can greatly benefit from this advanced technology.
Key Features of the Steel Titanium PVD Deposition Machine
1. Vacuum Chamber: The machine is equipped with a vacuum chamber where the stainless steel parts are placed during the coating process. The vacuum environment ensures a controlled atmosphere for the deposition, resulting in high-quality and uniform coatings.
2. Plasma Source: The machine features a plasma source capable of generating high-energy plasma. This plasma is essential for ionizing titanium atoms, which are then deposited onto the stainless steel parts to form a protective film.
3. Target Material: The target material in the machine is a titanium source, which is responsible for producing a stream of titanium atoms. These atoms are then ionized and deposited onto the stainless steel parts, forming a durable and corrosion-resistant layer.
4. Power Supply: The machine’s power supply provides the necessary energy for the plasma source and target, ensuring a stable and efficient coating process.
5. Cooling System: The Steel Titanium PVD Deposition Machine is equipped with a cooling system designed to prevent overheating of the stainless steel parts during the PVD process. This ensures that the coated parts maintain their structural integrity and avoid any potential damage from excessive heat.
How Does Stainless Steel Vacuum Coating Machine Work?
Stainless steel vacuum coating machines use Physical Vapor Deposition (PVD) to apply thin films onto stainless steel substrates within a vacuum chamber. The process involves preparing and placing stainless steel parts inside the chamber, creating a high-vacuum environment, and sometimes heating the parts.
PVD techniques, such as sputtering, evaporation, or ion plating, are used to deposit coating material onto the stainless steel parts. The coating material, typically in the form of a target, is vaporized or ionized and then deposited onto the substrate. Finally, the coated parts are cooled, resulting in enhanced properties like hardness, corrosion resistance, and wear resistance.
The Benefits of Stainless Steel Vacuum Coating Machine
1) Enhanced Durability: Vacuum coating significantly improves the hardness and wear resistance of stainless steel, extending the lifespan of products and reducing maintenance costs. This is particularly beneficial for components that are exposed to harsh environments or heavy wear.
2) Corrosion Resistance: Stainless steel vacuum coating creates a protective barrier against corrosion, making it ideal for applications in industries such as marine engineering, chemical processing, and oil and gas.
3) Aesthetic Appeal: Vacuum coating can produce a variety of colors and finishes, offering an attractive and customizable appearance for products. This is particularly popular in consumer goods, such as watches, jewelry, and electronic devices.
4) Improved Performance: By altering the surface properties of stainless steel, vacuum coating can optimize the material’s performance for specific applications, such as reducing friction in moving parts or enhancing heat dissipation in electronics.
5) Environmentally Friendly: PVD techniques used in stainless steel vacuum coating are environmentally friendly and produce little waste, making them a sustainable choice for manufacturers.
Applications of Stainless Steel Vacuum Coating Machine
1. Automotive Industry: Vacuum-coated stainless steel components, such as engine parts and exterior trim, offer improved wear resistance, corrosion protection, and aesthetics, contributing to longer-lasting and more attractive vehicles.
2. Aerospace: Enhanced durability and corrosion resistance make vacuum-coated stainless steel ideal for aerospace components, such as turbine blades, fasteners, and landing gear.
3. Medical Devices: The non-toxic and biocompatible nature of vacuum-coated stainless steel makes it an excellent choice for medical implants, surgical instruments, and other medical devices.
4. Electronics: Vacuum coating can improve heat dissipation, electrical conductivity, and corrosion resistance in electronic components, such as connectors, heat sinks, and semiconductor wafers.
5. Consumer Goods: From watches and jewelry to kitchen appliances and electronics, vacuum-coated stainless steel enhances both the aesthetics and durability of consumer products.
Conclusion
Stainless steel vacuum coating machines have truly transformed the material science landscape, enabling the development of high-performance, durable, and visually appealing products across a wide range of industries. As the technology continues to advance, we can expect even more exciting innovations and applications in the future, solidifying the stainless steel vacuum coating’s position as a cornerstone of modern material engineering.