How Does Metal Coat Resist Chemical Corrosion
- Physical Barrier Protection
- Sacrificial Anode Protection
- Chemical Inertness
- Passive Film Formation
- Organic Coating Support
- Multi-layer Composite Protection
Physical Barrier Protection
Metal coatings form tight barriers that keep corrosive substances away from the base material. Coating integrity is crucial. Defects like pinholes or cracks speed up corrosion. We must control process parameters carefully to ensure smooth, defect-free surfaces. According to ISO 4628-3, defects should cover less than 0.1% of the surface.
Thickness matters for barrier effectiveness. For example, epoxy resin coatings typically range from 150-500 microns, effectively blocking water, oxygen, and ions. But too thick coatings may crack from internal stress. In marine environments, we need to increase coating thickness by 20%-30%.
Density depends on application methods and material properties. Spraying and electrophoresis improve density and reduce porosity. Nickel and chrome coatings can have porosity below 0.1%, significantly extending protection. For instance, nickel coatings corrode at just 0.01mm/year in high-pressure, high-temperature environments.
Here’s a comparison of common metal coatings:
Coating Type | Thickness (μm) | Density | Porosity (%) | Environment (ISO 12944) | Adhesion Standard |
---|---|---|---|---|---|
Epoxy Resin | 150-500 | High | 0.3-0.8 | C4/C5-I (Industrial/Marine) | ≥7MPa (ASTM D4541) |
Polyurethane | 80-250 | Medium | 0.2-0.5 | C4/C5-M | ≥6MPa (ISO 16276-2) |
Hot-dip Galvanizing | 50-150 | Low | <1.0 | C5-M (Marine Extreme) | ≥5MPa (ISO 4624) |
Electroplated Nickel | 20-100 | Very High | <0.1 | C5-I (High Temp/Pressure) | ≥10MPa (ASTM B571) |
Chrome Coating | 10-50 | Very High | <0.1 | C5-X (Strong Acid/Base) | ≥8MPa (ASTM B571) |
Environmental factors affect coating performance. High heat and humidity reduce barrier effectiveness. We need to choose coatings based on environment, base material, and coating properties. For example, chrome coatings outperform others in acidic chemical plant environments.
Adhesion is key for long-term stability. Good adhesion prevents peeling or cracking. We typically need adhesion over 5MPa. In shipbuilding, we usually require over 7MPa.
Sacrificial Anode Protection
Sacrificial anode protection uses coating metals that corrode first to protect the base material. We commonly use zinc, magnesium, and aluminum, with zinc being the most popular. Zinc has a lower electrode potential (-1.05V vs CSE) than steel (-0.65V vs CSE), so it corrodes first, forming a protective zinc oxide layer.
Coating thickness, uniformity, and environment affect protection. For example:
- In marine environments, every extra 10 microns of zinc coating adds about a year of protection.
- Zinc coatings usually range from 50-150 microns, but we need over 200 microns in harsh environments.
- Uneven coatings fail early in some spots, reducing overall protection.
Environment significantly impacts sacrificial anode protection. For instance:
- Zinc coatings corrode at 10-20 microns/year in seawater.
- In freshwater, corrosion drops to 5-10 microns/year.
- High temperatures or low pH speed up corrosion, shortening protection.
Sacrificial anode protection is simple and reliable, but coating metals wear out fast, requiring regular maintenance. For example, we typically maintain zinc coatings on marine platforms every 5-10 years. Also, good electrical contact between coating and base material is crucial. Insulation or contaminants can reduce protection. So, we must clean the base material thoroughly before application to ensure good contact.
Composite coating technology improves protection further. For example, covering zinc coatings with epoxy resin or polyurethane significantly slows zinc corrosion, extending protection. Tests show composite coatings last 2-3 times longer in salt spray than plain zinc coatings (ISO 20340). We widely use this composite structure in marine engineering and petrochemical fields.
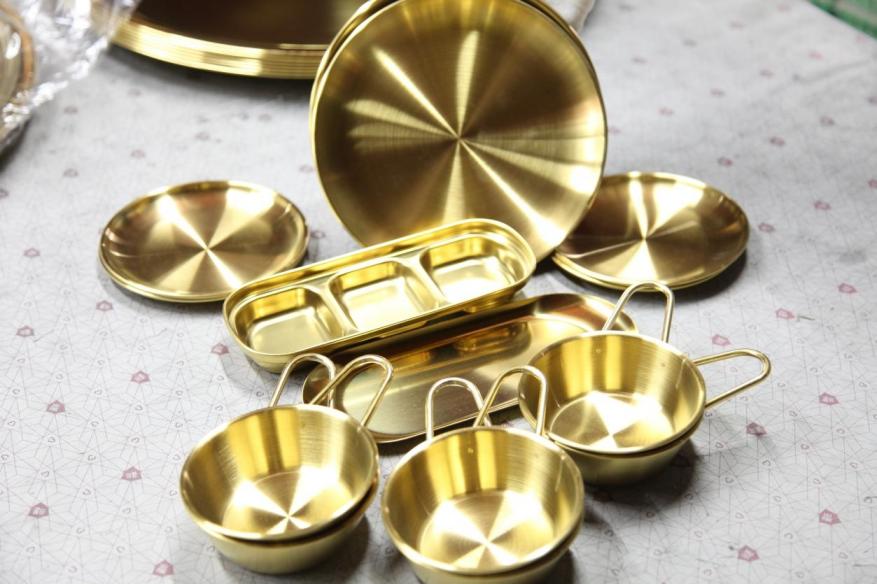
Chemical Inertness
One of the key ways metal coatings resist chemical corrosion is through their chemical inertness. This means the coating material doesn’t easily react with corrosive substances in its environment. This inertness works through various physical and chemical mechanisms, effectively blocking corrosive agents from reaching the base material and slowing down or stopping corrosion. Here’s how metal coatings use chemical inertness to fight corrosion:
- Forming a Protective Oxide Layer
- Aluminum coatings quickly form a thin aluminum oxide (Al₂O₃) layer in the air. This layer is only 2-10 nanometers thick but stays stable in pH ranges from 2 to 11. It resists attacks from acids, bases, and salts.
- Stainless steel coatings contain chromium, which forms a chromium oxide (Cr₂O₃) layer. This layer can self-repair after damage, boosting corrosion resistance.
- Boosting Inertness with Alloy Elements
- Chromium (Cr): Adding over 12% chromium helps stainless steel form a stable chromium oxide layer at room temperature, significantly improving corrosion resistance.
- Nickel (Ni): Stainless steel with over 8% nickel reduces corrosion rates in sulfuric and hydrochloric acids to less than 0.1 mm/year.
- Molybdenum (Mo): Adding 2-3% molybdenum raises the pitting potential of stainless steel in chloride environments to over 0.5 V, enhancing pitting resistance.
- Creating Dense Coating Structures
- Thermal spray coatings form dense structures through high-speed particle impact, with porosity as low as 1%. This dramatically slows down corrosive agent penetration.
- Electroplated coatings like zinc form a protective zinc carbonate layer in humid environments. This layer, 5-10 micrometers thick, effectively blocks corrosive agents.
- Performing in Extreme Environments
- Aluminum oxide coatings stay stable at high temperatures (>1000°C), making them ideal for aerospace and chemical equipment.
- Tantalum (Ta) coatings show corrosion rates below 0.01 mm/year in concentrated sulfuric acid (>95%), perfect for chemical equipment.
- Titanium (Ti) coatings have corrosion rates below 0.1 mm/year in 20% hydrochloric acid, ideal for strong acid environments.
By tweaking the chemical makeup and structure of coatings, we can boost their inertness and corrosion resistance. For example, in marine environments, molybdenum-rich stainless steel coatings can cut corrosion rates to below 0.05 mm/year. In chemical equipment, tantalum or titanium coatings can extend service life to over 20 years. Chemical inertness isn’t just the heart of a coating’s corrosion resistance—it’s also what keeps it stable in extreme conditions.
Passive Film Formation
Passive films are spontaneous, dense oxide or compound layers that form through electrochemical and thermodynamic processes. When metals are exposed to corrosive environments, surface atoms react with substances like oxygen or water, creating stable oxide layers. We can describe this process using Gibbs free energy change (ΔG). Negative ΔG values show spontaneous reactions. For example, Cr₂O₃ passive films on stainless steel have ΔG298K = -1059 kJ/mol (NIST database), showing high thermodynamic stability.
Passive film formation involves several steps:
- Initial adsorption: Oxygen or water molecules physically attach to the metal surface.
- Chemical adsorption: Attached molecules break apart and form chemical bonds with metal atoms.
- Nucleation and growth: Oxide nuclei form and expand.
- Stabilization: The film structure becomes dense and reaches dynamic equilibrium.
Passive films resist corrosion through several mechanisms. First, they usually have semiconductor properties. Their band gap (Eg) determines electron transfer capability. For example, Cr₂O₃’s Eg of about 3.0 eV is much higher than Fe₂O₃’s 2.2 eV, making chromium alloys more corrosion-resistant. Second, passive films’ dense structures effectively block corrosive ions (like Cl⁻, H⁺) from reaching the metal base. For example, Al₂O₃ passive films’ tight lattice structure significantly reduces ion mobility. Finally, passive films react very little with corrosive substances. For example, TiO₂ passive films show excellent stability in strong acids and bases.
We can optimize passive film performance by:
- Adding rare earth elements to increase film density.
- Including nanoparticles to improve film stability.
- Controlling environmental conditions to promote uniform film growth.
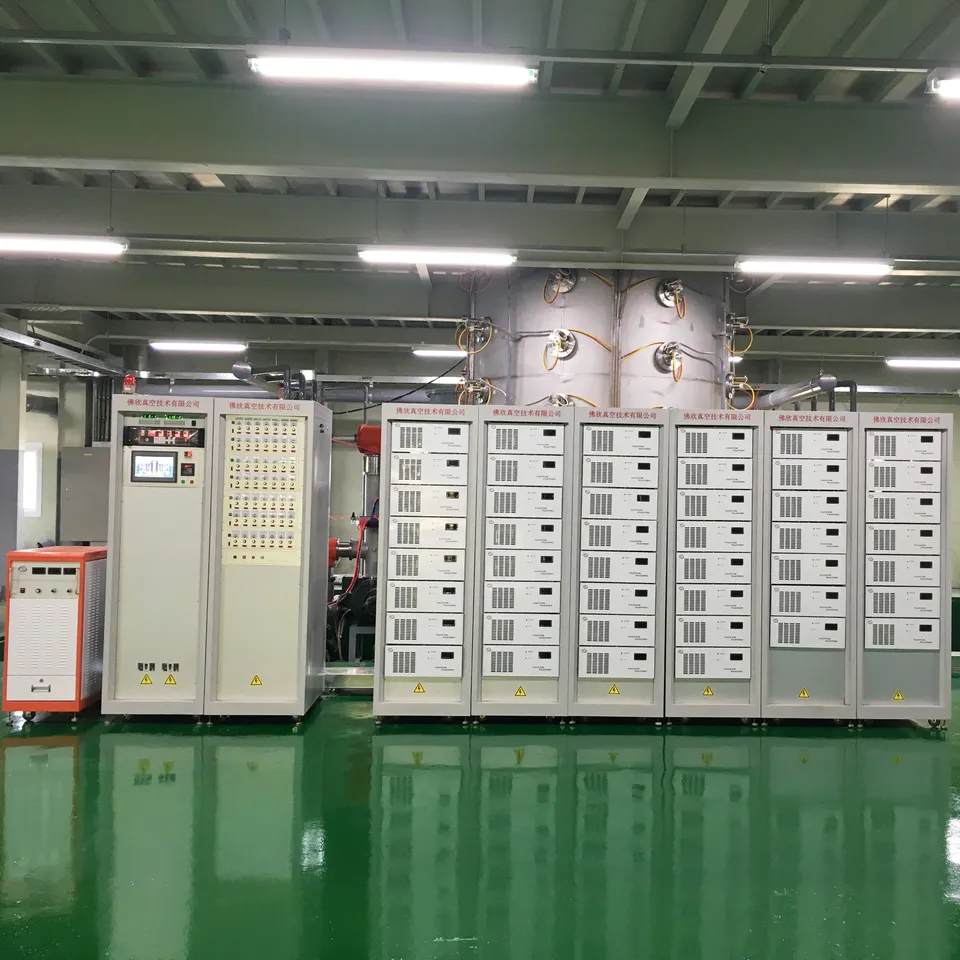
Organic Coating Support
Organic coatings do more than just provide physical barriers. They also enhance passive film protection through various mechanisms. Organic coatings usually consist of polymer bases, fillers, and additives. Their performance depends on chemical composition and microstructure. For example, epoxy resin coatings are widely used in metal corrosion protection due to their excellent adhesion and chemical stability.
Organic coatings protect through:
- Physical barriers: They form dense layers that block corrosive substances from contacting metal surfaces.
- Inhibitor release: Inhibitors (like molybdates) in the coatings slowly release, slowing corrosion.
- Interface enhancement: Coatings form chemical bonds with metal surfaces, improving adhesion and durability.
Organic coatings support protection in several ways. First, their physical barriers effectively block water, oxygen, and corrosive ions (like Cl⁻). For example, polyurethane coatings’ low porosity significantly reduces substance diffusion. Second, inhibitors in coatings react with metal surfaces to form protective layers, further slowing corrosion. For example, molybdate inhibitors create MoO₄²⁻ films on stainless steel, enhancing passive film stability. Finally, the bond strength between organic coatings and metal surfaces determines coating durability. For example, silane coupling agents improve coating-metal adhesion through chemical bonding.
We can optimize organic coating performance by:
- Adding nano fillers (like SiO₂, TiO₂) to increase density and mechanical strength.
- Including functional additives (like inhibitors, UV absorbers) to improve environmental adaptability.
- Controlling curing processes to optimize microstructure and interface bonding.
Multi-layer Composite Protection
Multi-layer composite coatings offer the most advanced protection. They combine different materials to create multi-level protective structures. These systems usually include primer, middle layer, and topcoat, each serving specific functions that work together for comprehensive protection. For example, in marine environments, zinc layers act as sacrificial anodes, epoxy middle layers provide barriers, and polyurethane topcoats resist UV light. These structures can protect for over 15 years, but they’re complex to apply and expensive.
Here’s an example of a multi-layer composite coating structure:
- Primer: Zinc layer, 50μm thick, acts as sacrificial anode to protect base metal.
- Middle layer: Epoxy resin, 150μm thick, provides dense barrier against corrosive substances.
- Topcoat: Polyurethane, 100μm thick, resists UV light, mechanical wear, and chemical erosion.
Multi-layer composite coatings protect through multiple mechanisms. Primers’ sacrificial anode function works through electrochemical principles – zinc’s electrode potential is lower than the base metal, so it oxidizes first to form a protective layer. Middle layers’ epoxy resin effectively blocks water, oxygen, and ions through its dense structure and high cross-link density. Topcoats’ polyurethane protects lower layers from environmental erosion through excellent weather resistance and mechanical properties.
Multi-layer composite coatings offer several advantages:
- Long-term protection: Layers work together to significantly extend protection periods.
- Multi-functionality: We can customize coating structures for different corrosive environments.
- Wide adaptability: Suitable for extreme environments like marine, chemical, and high-temperature conditions.