
News
12 Year Pvd Coating Machine In Foxin
How SMEs Can Select the Right Vacuum Coating Machinery
In the dynamic fields of automotive, electronics, and decorative coatings, small and medium – sized enterprises (SMEs) often grapple with choosing the optimal vacuum coating machinery. This decision significantly impacts both performance and cost. Let’s compare two prevalent vacuum coating techniques – Physical Vapor Deposition (PVD) and Chemical Vapor Deposition (CVD).
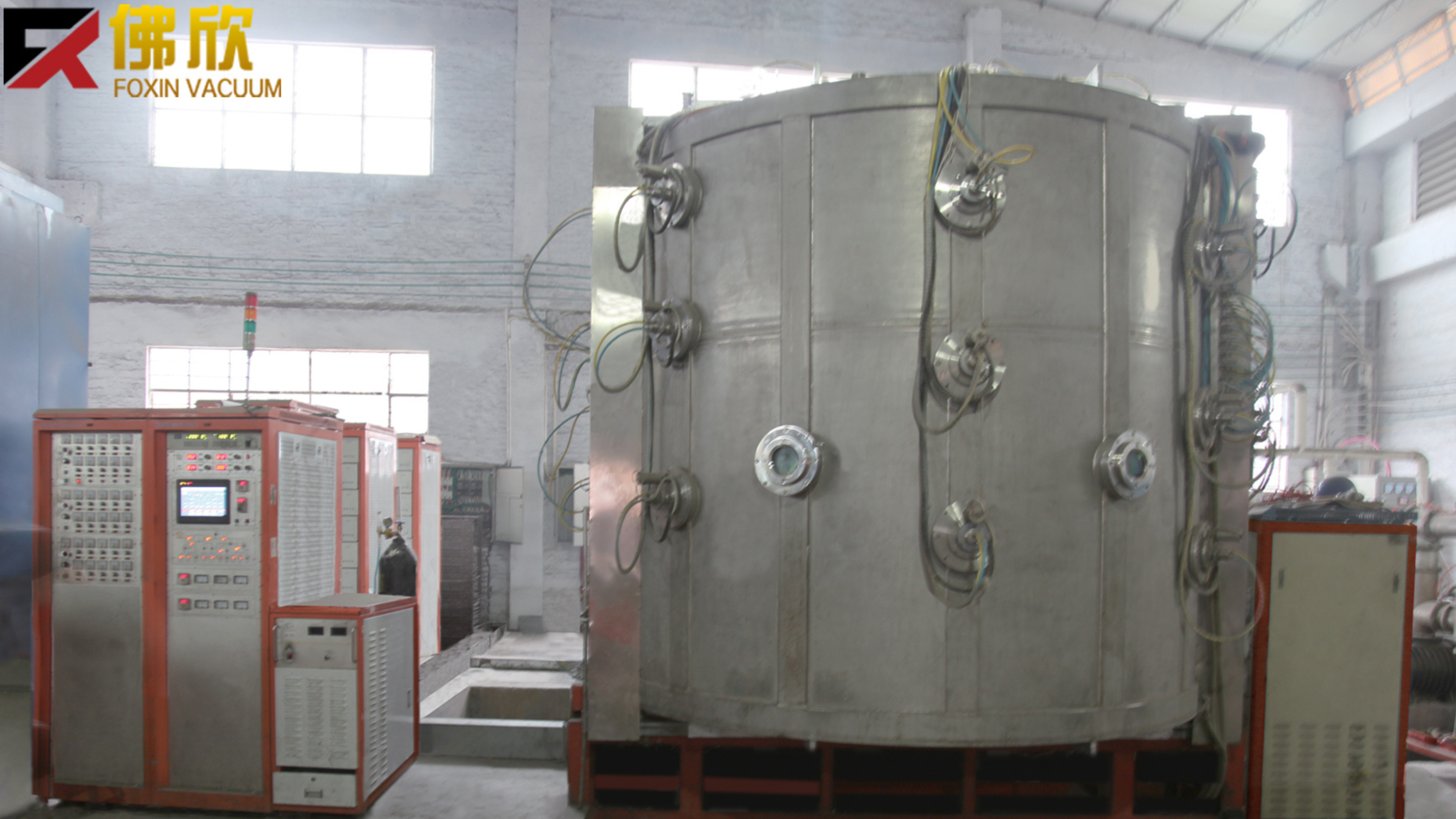
Understanding Vacuum Coating Machinery
Vacuum coating machinery is designed to deposit thin films on substrates within a vacuum environment. These films enhance crucial properties like wear resistance, aesthetic appeal, and electrical insulation. PVD and CVD are the two main processes employed in such machinery.
PVD and CVD: A Comparative Overview
Physical Vapor Deposition (PVD) Coating Machinery
PVD – based vacuum coating machinery vaporizes solid materials in a vacuum chamber. The vapor then condenses onto the substrate. Evaporation, where material is heated to vaporize, and sputtering, which uses plasma to eject atoms from a target onto the substrate, are common PVD methods. This type of machinery is ideal for producing coatings such as titanium nitride (TiN), chromium nitride (CrN), and diamond – like carbon (DLC). These coatings are hard and wear – resistant, finding applications in automotive parts, tooling, and decorative items.
Chemical Vapor Deposition (CVD) Coating Machinery
CVD machinery uses chemical reactions in a vacuum. Gaseous precursors react to deposit solid material on the substrate. Variants like Low – Pressure CVD (LPCVD) and Plasma – Enhanced CVD (PECVD) have their unique applications. CVD machinery is well – suited for creating coatings like silicon dioxide (SiO₂) and silicon nitride (Si₃N₄), which are crucial in semiconductor and aerospace industries due to their ability to form thick, durable films.
Key Considerations for SMEs
1. Coating Material Compatibility
PVD machinery: Perfect for hard – wearing coatings, offering durability in various applications.
CVD machinery: Specializes in coatings for high – tech industries, providing thick and reliable films.
2.Substrate Adaptability
PVD machinery: Compatible with metals, glass, ceramics, and plastics, suitable for thin – film applications.
CVD machinery: Can coat complex shapes, but high temperatures limit its use with heat – sensitive substrates.
3.Coating Thickness and Uniformity
PVD machinery: Produces coatings from nanometers to micrometers, with some challenges in coating complex geometries.
CVD machinery: Creates thicker, more uniform coatings, ideal for components with intricate shapes.
4.Temperature and Process Requirements
PVD machinery: Operates at lower temperatures (150°C – 500°C), suitable for temperature – sensitive materials.
CVD machinery: Requires higher temperatures (500°C – 1000°C), suitable for high – performance applications but not for heat – sensitive substrates.
5.Cost – Efficiency
PVD machinery: Generally more cost – effective, with lower energy use and simpler maintenance.
CVD machinery: Tends to be more expensive in terms of initial investment, energy, and maintenance.
6.Environmental and Safety Aspects
PVD machinery: Environmentally friendly with fewer toxic byproducts, requiring less complex safety measures.
CVD machinery: Can produce hazardous byproducts, necessitating advanced safety and ventilation systems.
For SMEs seeking high-performance, cost-effective coatings for wear resistance, decoration, or aesthetics, PVD vacuum coating machinery offers versatile solutions, widely used in industries such as automotive, tooling, and consumer electronics with small- to medium-scale production. CVD machinery, known for creating thick, uniform coatings, excels in specialized fields like semiconductor manufacturing and aerospace. However, its higher costs and complexity are factors to consider when deciding its suitability for specific applications. By evaluating material type, coating thickness, substrate compatibility, and production scale, SMEs can assess the best coating solution for their needs.
If you have any questions or need more information, please feel free to leave a message in the background and we will answer you as soon as possible. Looking forward to working with you!