Is Your PVD Coating Machine Built for Quality? Factory Tour
FoXin brings three decades of PVD coating machine expertise to the market, combining advanced vacuum deposition technology with precision manufacturing. Their equipment delivers premium coatings for hardware, automotive and electronics applications. Rigorous quality standards and reliable customer support have made FoXin’s durable PVD coating systems a trusted choice worldwide.
1. Factory Overview
FoXin is a company that makes PVD coating machines, tucked away in a quiet industrial zone. From the outside, it doesn’t look like much, but step inside, and you’ll find a bustling manufacturing hub. For the past 30+ years, the team’s been all about designing and building these machines, shipping them worldwide. This visit takes us into the workshop to see how PVD coating goes from blueprints to real, working equipment. No fancy frills here, just machines and workers getting stuff done.
1.1 Inside the Operation
During the tour, the production line was running smoothly, with dozens of workers handling their tasks like a well-oiled machine, assembling PVD coating units one by one. Orders pour in steadily from buyers in the hardware, automotive, and electronics sectors, keeping the demand constant. The manufacturing center boasts an impressive annual output, ranking high in the industry, and spans tens of thousands of square meters. The workshop is packed with parts and finished machines, while detailed design sketches line the walls, mapping out every piece of equipment.
The R&D team works in a separate building, tinkering with vacuum coating tech and pouring significant funds into boosting machine performance year after year. Over in the materials area, stacks of stainless steel sheets and electrical components sit ready, essential ingredients for PVD coating. What started as a small shop has grown into this sprawling operation through years of hard work and technical know-how. This visit really drove home the sheer production power behind FoXin’s PVD coating machines, with golden finishes and wear-resistant coatings keeping the lines buzzing.
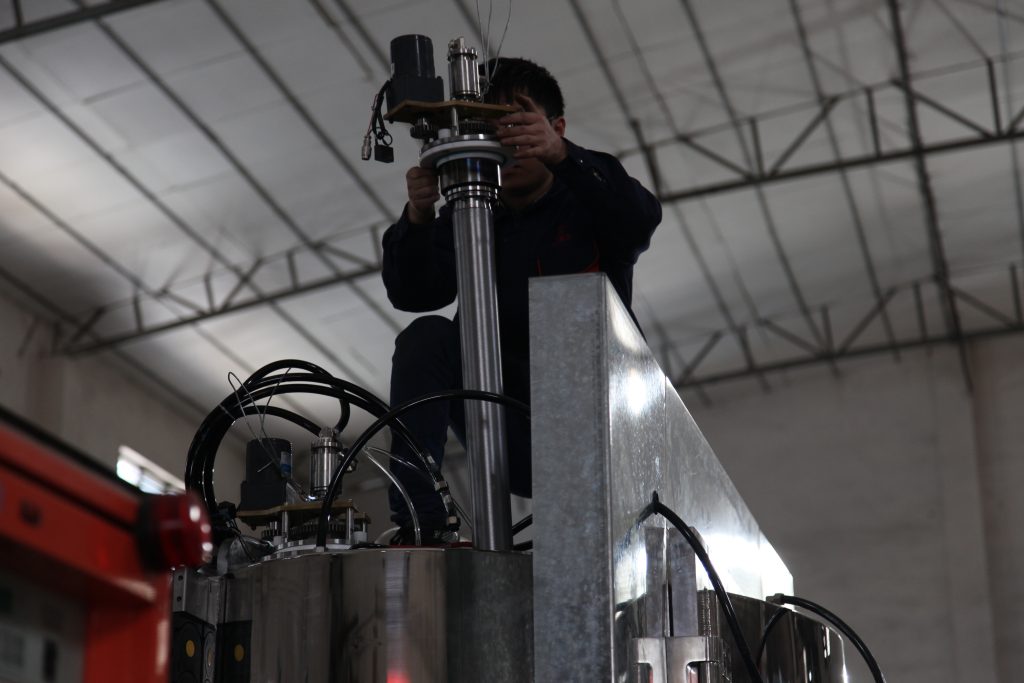
1.2 Business Scope
FoXin specializes in PVD coating machines, serving clients like hardware processors, automotive parts suppliers, and electronics companies. PVD coating, short for physical vapor deposition, uses vacuum coating technology to apply metal layers onto product surfaces. It’s both stylish and functional. The team designs machines capable of handling everything from decorative gold finishes to durable, wear-resistant coatings. For example, automotive parts suppliers might need heat-resistant metal layers, while hardware factories want shiny gold coatings. These machines deliver on all fronts.
With years of experience, the team knows how to craft efficient coating equipment. Their manufacturing hub holds patents for magnetron sputtering technology, ensuring even metal layers every time. Orders stay steady, with buyers spanning dozens of countries. The technical crew doesn’t just build PVD coating machines; they also offer support to make sure users get the hang of them. The R&D team regularly chats with customers, gathering feedback to fine-tune the coating process. At its core, the business is about delivering top-notch vacuum coating equipment to the people who need it, plain and simple.
2. PVD Coating Machine Technology
2.1 Core Technology
PVD coating relies on vacuum technology, where a multi-stage pumping system keeps things running smooth. Rotary vane pumps kickstart the pressure drop, roots pumps maintain the environment, then diffusion pumps or turbomolecular pumps pull high vacuum. Each high-end pump has its own strengths:
Pump Type | Working Principle | Advantages | Drawbacks | Best Use Cases |
---|---|---|---|---|
Diffusion Pump | Oil vapor evacuation | Fast pumping, high capacity | High power use, slow startup | Stainless steel coatings, hardware |
Molecular Pump | High-speed blade exhaust | Energy-efficient, stable | Higher cost | Electronic components, wear-resistant coatings |
Diffusion pumps excel at rapid pumping, making them ideal for high-volume PVD coating tasks like stainless steel layers on hardware, which accounts for a big chunk of production. Molecular pumps, on the other hand, save energy and run quietly, perfectly suiting wear-resistant coatings for electronic parts. Production facilities keep both pump types on hand, letting users choose based on their needs. The vacuum system is critical to PVD coating quality; pick the wrong pump, and you’ll end up with uneven metal layers. To maintain efficiency, technicians regularly service the pumps, swapping out oil and cleaning parts to ensure steady performance. A PLC control system keeps parameters precise, making the coating process seamless with virtually no thickness errors in the metal layers. This vacuum coating tech has been refined over years, delivering hard, durable surfaces every time.
2.2 Machine Design
PVD coating machines are built tough and user-friendly. The stainless steel chamber withstands high heat and corrosion, with tight seals to prevent leaks during coating. The rotating rack comes in two styles: top-mounted or cart-based, accommodating parts of all sizes for flexible operation. The control panel is straightforward, showing vacuum levels, temperature, and gas flow at a glance, so operators can easily keep tabs on things.
Coating methods include thermal evaporation or magnetron sputtering. Thermal evaporation heats the target material, vaporizing metal to form a film quickly, which works great for decorative PVD gold finishes. Magnetron sputtering uses plasma to bombard the target, creating uniform, tough metal layers ideal for wear-resistant coatings.
During a recent visit, I saw a machine in action, its chamber glowing faintly as the coating process unfolded. The design adapts to specific needs: thermal evaporation for decorative pieces, magnetron sputtering for durable ones. Inside, aluminum or stainless steel shields line the chamber, swapped out regularly to protect the walls. The rotating rack has been fine-tuned for even motion, ensuring gold and wear-resistant coatings hit every angle without blind spots. Want a PVD gold or black finish? Just tweak the nitrogen and target material mix, and the machine handles it. The design team frequently visits the shop floor, observing real-world production to make practical upgrades, ensuring the equipment keeps getting better.
3. Production Process
3.1 Manufacturing Process
The production kicks off with the parts. Workers start with stainless steel sheets and electrical components, cutting and welding them according to blueprints. The stainless steel chamber is welded tightly to ensure no leaks during the vacuum coating process. The rotating rack is built from sturdy steel, designed to hold hundreds of pounds of parts without breaking a sweat. Wiring the control panel has to be spot-on; a single mistake in the circuitry could throw off the entire coating process. Once the parts are ready, the machine is assembled with screws, every panel aligned perfectly with no gaps. After assembly, it’s powered up for a test run to catch any issues.
The target materials, usually titanium or chromium, are stored in a designated area and pulled out for installation to guarantee top-notch PVD coating results. In the workshop, multiple machines are assembled at once, churning out a solid daily output of parts with decent overall capacity. Speed is key, but cutting corners on details isn’t an option. Every PVD coating machine has to stand up to scrutiny. A spare parts inventory is always on hand to replace anything that breaks, keeping delays at bay. Years of experience have streamlined the process, with workers collaborating seamlessly to save time. Installing targets for thermal evaporation and magnetron sputtering is critical, as it directly impacts the quality of gold-colored or wear-resistant coatings. For stainless steel coatings, welding demands extra attention; even a tiny leak can ruin everything.
3.2 Equipment Testing
Once a PVD coating machine is assembled, it’s time for testing. First, the vacuum is pumped down to see if the system can handle the pressure drop. If the stainless steel chamber isn’t sealed tight, the coating process is a bust. Next, a trial run kicks off: parts are loaded in, and the machine runs a cycle using either thermal evaporation or magnetron sputtering. The rotating rack spins, and the metal coating needs to come out even, not thick on one side and thin on the other. The control panel’s readings have to stay steady, with vacuum levels and temperatures holding firm. Only when the parts come out smooth and flawless does it pass the test.
The manufacturing center enforces strict testing standards, and every machine has to clear the bar before shipping out. If a buyer wants a PVD gold finish or a wear-resistant coating, technicians tweak the settings and run more tests. Testing takes time, but skipping it isn’t an option; the coating tech has to be flawless. With a hefty annual order volume, the testing area is a hive of activity, employees keeping a close eye on each machine to ensure metal coating quality. Noise levels are monitored too; if it’s running too loud, adjustments are made to keep the workshop bearable. The vacuum system gets regular checkups after long runs, or the PVD coating quality starts to slip.
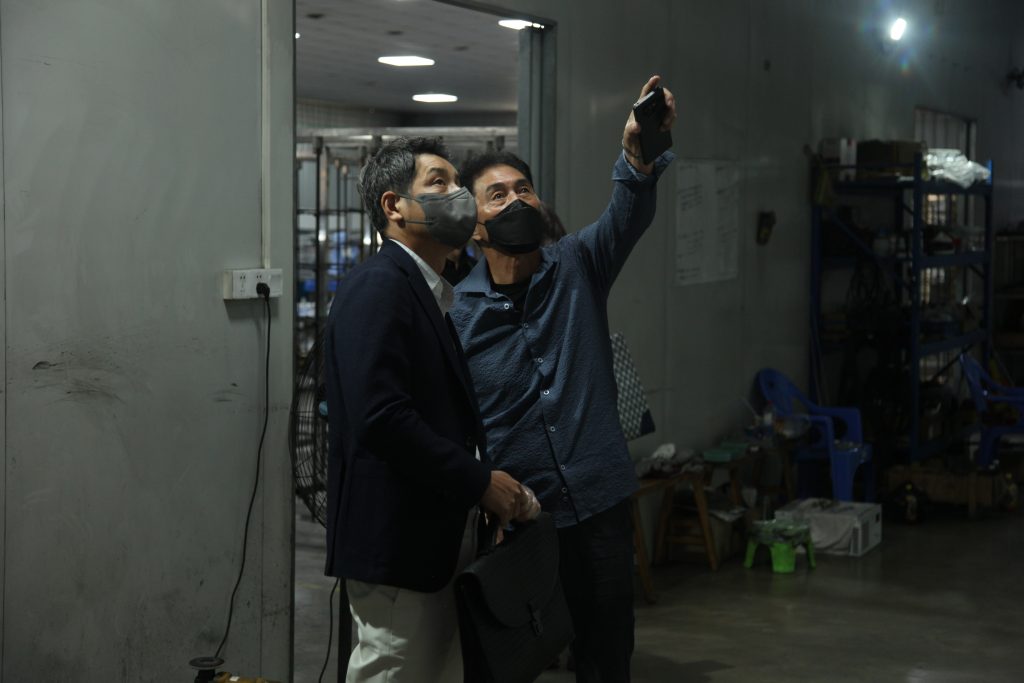
4. Machine Features and Applications
4.1 Coating Benefits
PVD coating adds a metal layer to products, offering both rust protection and durability. A shiny gold coating can last for years, making it perfect for decorative purposes. When applied to stainless steel hardware, it creates a smooth, corrosion-resistant surface with no issues. Wear-resistant coatings, like the tough black titanium nitride, stand up to high temperatures and abrasion, doubling the lifespan of tools. The coating process is adjustable, ranging from vibrant PVD gold to deep black, depending on what’s needed.
The equipment’s stability ensures an even metal layer with no missed spots. Manufacturing hubs keep refining coating tech, making wear-resistant layers harder and gold finishes brighter. Though thin, these coatings pack enough hardness to handle daily wear and tear. Whether it’s hardware, car parts, or electronic components, PVD coatings deliver solid results. Stainless steel coatings, in particular, hold up well in humid environments without breaking a sweat.
4.2 Customer Use Cases
PVD coating machines are incredibly versatile. Hardware factories use them to coat door handles or lighting fixtures, churning out tens of thousands of pieces yearly with gold finishes that look great and last long. Auto parts suppliers apply wear-resistant coatings to things like exhaust pipes, which shrug off high heat with ease. Electronics companies rely on the machines for precision parts, such as PVD gold conductive elements that need to be thin yet uniform. Toolmakers add wear-resistant layers to blades, boosting hardness and extending usability.
Customers have all kinds of needs, some running huge batches, others doing small custom jobs, and PVD coating machines handle it all. Manufacturing teams talk to buyers often, picking up on what they want and designing with those scenarios in mind. Big orders need speed, small ones demand precision, and the coating tech adapts seamlessly. Thermal evaporation works great for quick decorative jobs, while magnetron sputtering nails wear-resistant needs. These vacuum coating machines never let you down.
Quality and Service
5.1 Quality Management
Quality control is woven into every step of the PVD coating machine production process. When parts arrive at the factory, they’re inspected thoroughly: stainless steel sheets must be flat, and electrical components need to be dependable. During assembly, precision is non-negotiable. Welds are airtight, screws are tightened just right. Testing involves microscopes and gauges to measure metal coating thickness, with PLC controllers ensuring pinpoint accuracy and minimal errors. Only when inspection reports confirm that hardness and thickness meet standards does the coating technology get the green light.
Pre-treatment is a make-or-break step for vacuum coating. Parts go through ultrasonic cleaning to strip away grease, ensuring the metal coating sticks tight. Then, a baking oven dries them at a controlled temperature to keep moisture from messing things up. The cleaning relies on high-frequency vibrations to blast away dust and grime, while the drying temp is dialed in perfectly. Years of hands-on experience have fine-tuned this process. Every batch of PVD coating machines gets sampled and tested, and only the ones that pass ship out. Buyers rave about the golden and wear-resistant coatings, and repair rates stay low. Stainless steel coatings, though? They demand extra attention during pre-treatment, or the PVD layer might peel off.
5.2 Customer Support
Selling a PVD coating machine is just the starting line; making sure it works well for the customer is the finish. Picture this: a truck loaded with equipment, labeled for the buyer, ready to roll out. Delivery deadlines are tight, so the logistics crew syncs seamlessly with production. The moment a machine is ready, it’s packed up and shipped, no delays. Techs connect with buyers, walking them through setup, parameter tweaks, and running the coating process. Want to tweak the golden or wear-resistant PVD finish? They’ll guide you remotely or even show up on-site.
The production base has a solid support system in place. Issues pop up? They’re tackled fast, keeping downtime off the table. Decades of know-how don’t just go into building the machines; they fuel the service too. When buyers ask about maintenance, the team delivers straight answers to keep those vacuum coating machines humming smoothly.
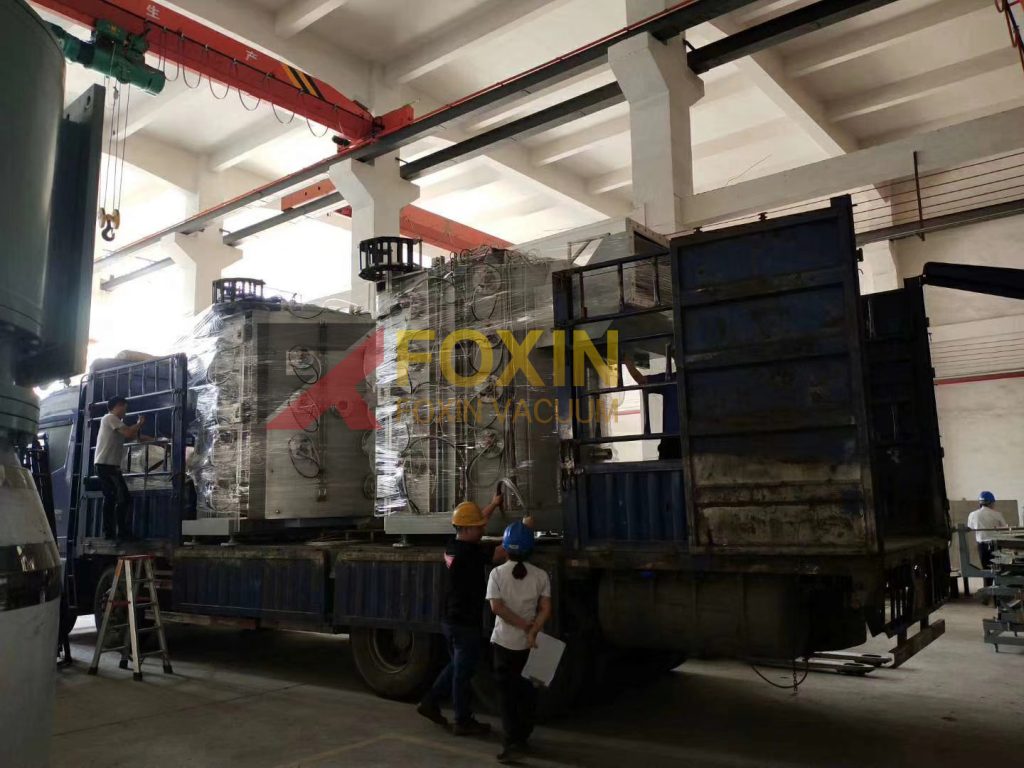
Wrap-Up
This visit peeled back the curtain on how PVD coating machines go from raw parts to finished products, with every step grounded in real craftsmanship. FoXin’s 30 years of focus and technical expertise shine through in every machine. With strong manufacturing chops and top-notch service, these machines land in customers’ hands ready to perform.