
News
12 Year Pvd Coating Machine In Foxin
Understanding the Machine PVD System: A Comprehensive Guide
Physical Vapor Deposition (PVD) systems have revolutionized the process of depositing thin films, offering precision and versatility in various industrial applications. This blog delves into the intricacies of Machine PVD systems, focusing on their definition, components, and working principles.
Definition and Functionality of Machine PVD Systems
1.1 What is a Machine PVD System?
A Machine PVD (Physical Vapor Deposition) system is an advanced apparatus used for depositing thin films onto substrates. These systems operate under high vacuum conditions, ensuring controlled environments for optimal film formation.
1.2 Core Definition
At its core, a Machine PVD system utilizes physical processes to vaporize material from a source and deposit it as a thin film onto a substrate. This method is crucial in industries like semiconductor manufacturing, optics, and surface engineering.
1.3 Purpose and Applications
The primary purpose of a Machine PVD system is to create thin films with specific properties such as hardness, wear resistance, or optical characteristics. Applications range from coating tools and components to enhancing the performance of electronic devices.
1.4 Advantages Over Other Methods
Compared to chemical vapor deposition (CVD) and other thin-film deposition techniques, PVD offers superior adhesion, high-purity coatings, and the ability to deposit a wide range of materials including metals, alloys, and ceramics.
Components of a Machine PVD System
2.1 Vacuum Chamber: The Heart of the System
The vacuum chamber is the central component where the deposition process takes place. Maintaining a high vacuum is crucial for preventing contamination and ensuring high-quality film formation.
a. Construction and Design
Typically made of stainless steel, the vacuum chamber is designed to withstand high vacuum pressures and accommodate various sources and substrates. It includes ports for viewing, loading, and monitoring the process.
b. Vacuum Maintenance
An array of pumps, including rotary and turbomolecular pumps, work in tandem to achieve and maintain the desired vacuum levels. These pumps remove air and other gases from the chamber, creating an optimal environment for deposition.
c. Importance in Deposition Quality
The quality of the vacuum directly affects the purity and adherence of the thin films. A well-maintained vacuum environment minimizes defects and impurities, resulting in superior film properties.
2.2 Deposition Sources: Evaporation and Sputtering
The sources in a PVD system are responsible for generating the vapor that condenses onto the substrate. These sources vary depending on the specific deposition method used.
a. Evaporation Sources
Evaporation sources include electron beam, resistance, and thermal evaporation methods. These techniques heat the material until it vaporizes, allowing it to condense on the substrate.
b. Sputtering Targets
In magnetron sputtering, targets made of the coating material are bombarded with high-energy particles, causing atoms to be ejected and deposited onto the substrate. This method is ideal for coating complex shapes and large areas.
c. Source Power Supply
A dedicated power supply provides the necessary energy to the evaporation sources or sputtering targets. This component is crucial for controlling the deposition rate and ensuring consistent film thickness.
2.3 Substrate Handling: Uniform Coating and Precision
Substrate handling mechanisms are designed to hold and manipulate the substrates during the deposition process, ensuring uniform coating and high precision.
a. Substrate Holders
Substrate holders secure the substrates in place and often incorporate rotation or movement mechanisms to achieve even coating. They can accommodate various substrate sizes and shapes, enhancing the system’s versatility.
b. Movement Mechanisms
Rotational and translational movements are employed to expose the substrate to the vapor from all angles. This ensures a uniform film thickness across the entire surface.
c. Temperature Control
Maintaining optimal substrate temperature is critical for adhesion and film quality. Many systems include heating or cooling elements to control the substrate temperature throughout the process.
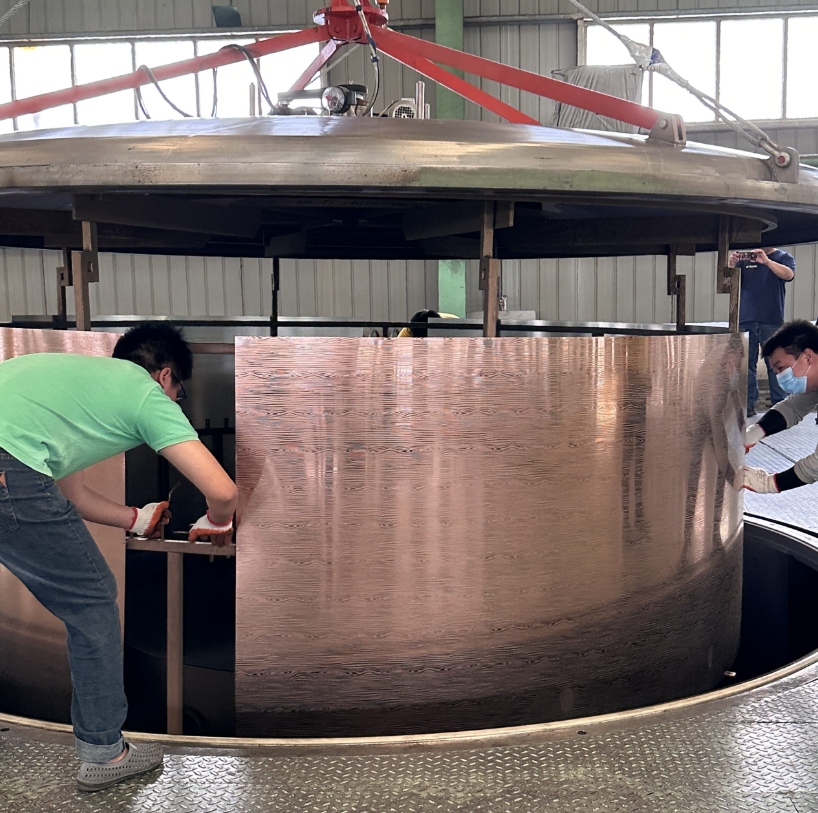
Working Principle of Machine PVD Systems
3.1 Vapor Generation and Deposition
The working principle of a Machine PVD system involves the generation of vapor from the source material and its subsequent condensation onto the substrate to form a thin film.
a. Heating the Source Material
Depending on the method (evaporation or sputtering), the source material is heated to a point where it vaporizes. In evaporation, this is achieved through electron beams, resistance heating, or thermal methods. In sputtering, high-energy particles are used to dislodge atoms from the target material.
b. Vapor Transport
The vapor travels through the vacuum chamber and condenses onto the substrate. The high vacuum ensures that the vaporized atoms or molecules reach the substrate without colliding with other gas molecules, maintaining their purity.
c. Film Formation
As the vapor condenses, it forms a thin, uniform film on the substrate. The thickness and properties of the film can be precisely controlled by adjusting the deposition parameters such as source power, substrate movement, and chamber pressure.
3.2 Ensuring Uniform Coating
Achieving a uniform coating is paramount in PVD processes. This is accomplished through the careful design and operation of the substrate handling mechanisms.
a. Rotational Movement
Substrates are often rotated to ensure that all surfaces are evenly exposed to the vapor. This rotation can be continuous or oscillatory, depending on the desired film characteristics.
b. Multiple Sources
Using multiple sources within the chamber can also help achieve uniform coatings, especially for large or irregularly shaped substrates. These sources can be strategically positioned to cover different areas of the substrate.
c. Real-Time Monitoring
Advanced PVD systems incorporate real-time monitoring tools to adjust parameters on the fly, ensuring uniform film deposition. Sensors and feedback mechanisms provide data on film thickness and uniformity.
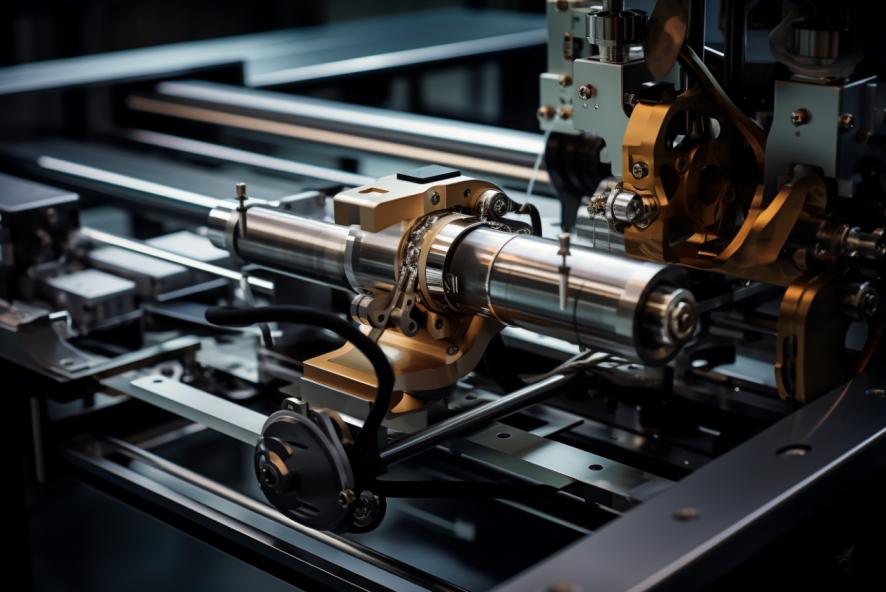
3.3 Maintaining High Vacuum Conditions
The efficiency and quality of the PVD process depend heavily on maintaining high vacuum conditions within the chamber.
a. Pumping Systems
A combination of mechanical and turbomolecular pumps is used to achieve the required vacuum levels. These pumps work continuously to remove any residual gases that could interfere with the deposition process.
b. Leak Detection
Regular leak detection and maintenance are essential to prevent air ingress, which can compromise the vacuum and affect film quality. Modern systems often include automated leak detection tools.
c. Vacuum Measurement
Accurate vacuum measurement is critical for process control. Gauges and sensors are used to monitor vacuum levels, ensuring they remain within the desired range throughout the deposition process.
Foxin Vacuum Technology Company: Leading the Way
4.1 Innovative PVD Solutions
Foxin Vacuum Technology Company is renowned for its cutting-edge PVD systems, offering innovative solutions for various industrial applications.
a. Advanced Technology
Foxin’s PVD systems incorporate the latest advancements in vacuum technology, ensuring high performance and reliability. Their systems are designed to meet the demanding requirements of modern thin-film deposition processes.
b. Customization and Flexibility
Understanding that different industries have unique needs, Foxin offers customizable PVD systems. These systems can be tailored to specific applications, providing flexibility and precision.
c. Global Reach
With a strong global presence, Foxin serves customers across multiple continents, providing excellent support and service. Their commitment to quality and innovation makes them a preferred choice for PVD systems.
4.2 Commitment to Quality
Foxin Vacuum Technology Company emphasizes quality in every aspect of its PVD systems.
a. Rigorous Testing
Each system undergoes rigorous testing to ensure it meets the highest standards of performance and reliability. This commitment to quality ensures consistent results in thin-film deposition.
b. Continuous Improvement
Foxin continuously invests in research and development to improve its PVD technology. By staying at the forefront of innovation, they ensure their systems deliver the best possible performance.
c. Customer Support
Foxin provides comprehensive customer support, from system installation to ongoing maintenance. Their expert team is available to assist with any technical challenges, ensuring smooth operation and maximum uptime.
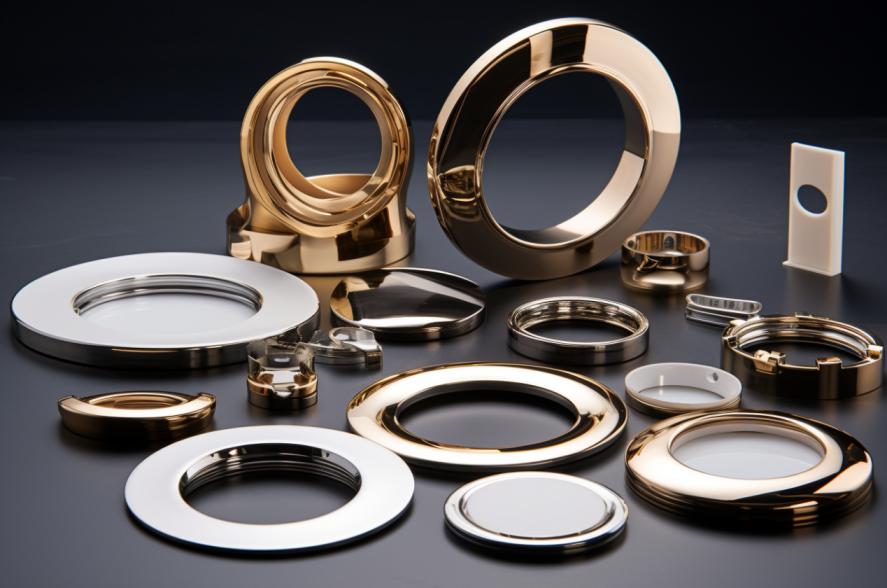
Conclusion
In conclusion, Machine PVD systems play a crucial role in the thin-film deposition industry. With their advanced technology and commitment to quality, companies like Foxin Vacuum Technology are leading the way in providing reliable and efficient PVD solutions. Whether for electronic devices, optics, or surface engineering, PVD systems offer unmatched precision and versatility.