Is Machine PVD System the Solution Your Products Need?
Physical Vapor Deposition (PVD) has emerged as a critical technology in various industrial sectors, offering advanced surface coating solutions that enhance durability, performance, and aesthetics of products. A Machine PVD System represents the pinnacle of this technology, integrating precision engineering with cutting-edge materials science to deliver tailored coating applications. At the forefront of this innovation is Foxin Vacuum Technology Company, a leading manufacturer specializing in customizable PVD systems for diverse industries.
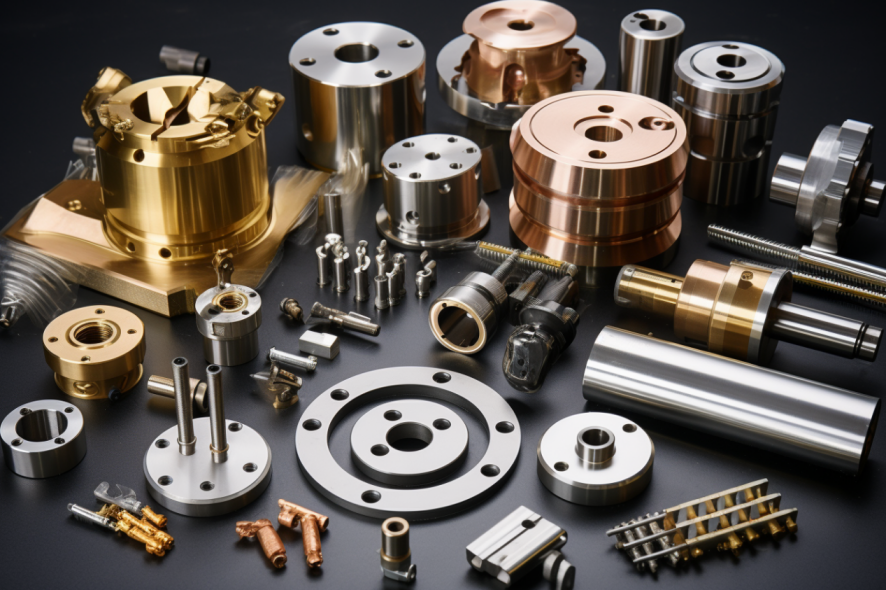
Industries Benefiting from Machine PVD System
Watch Industry
In the watch industry, precision and durability are paramount. Machine PVD system provides watchmakers with coatings that improve scratch resistance, enhance aesthetic appeal, and ensure longevity of timepieces.
3C Industry (Computers, Communications, Consumer Electronics)
Devices in the 3C industry demand both functionality and aesthetics. PVD coatings enable manufacturers to achieve desired surface properties such as anti-corrosion, wear resistance, and unique color finishes that distinguish their products in the market.
Hardware Industry
Hardware products, from architectural fittings to industrial tools, benefit from enhanced durability and corrosion resistance provided by PVD coatings. Machine PVD systems cater to these needs by offering customizable solutions that meet specific industry standards.
Precision Mold Industry
Precision molds require high wear resistance and low friction properties to maintain accuracy and longevity. Machine PVD systems can coat intricate mold surfaces uniformly, improving mold release and reducing maintenance downtime.
Tool Industry
Tools subjected to harsh conditions benefit from PVD coatings that enhance cutting performance, reduce friction, and extend tool life. Machine PVD systems are essential in optimizing these properties to meet the demanding requirements of tool manufacturers.
Kitchenware Stainless Steel Sink PVD Coating Machine: Enhancing Durability and Aesthetics
Overview
The Stainless Steel Sink PVD Coating Machine by Foxin Vacuum Technology utilizes advanced vacuum coating technology to apply thin films on stainless steel sinks. These coatings enhance surface properties such as corrosion resistance, wear resistance, and aesthetic appeal, thereby improving the durability and visual attractiveness of kitchen sinks.
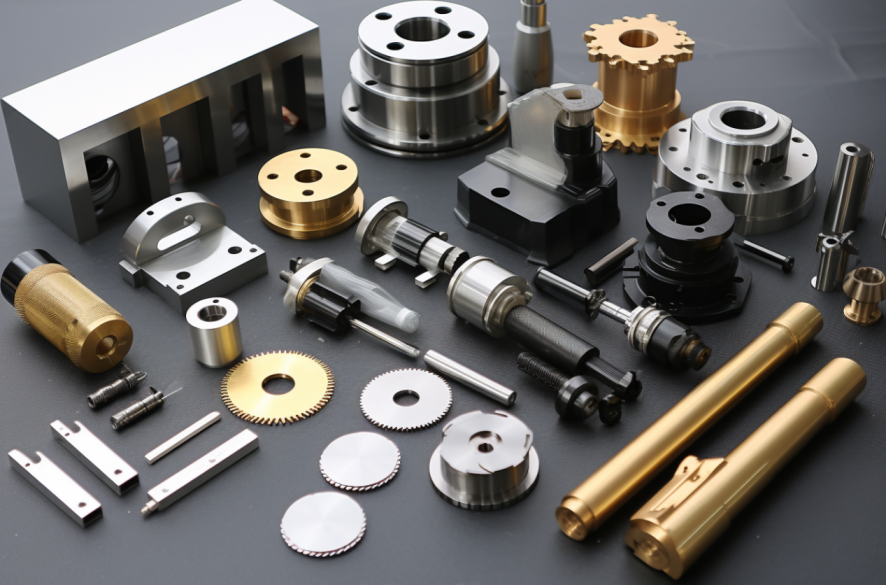
Enhancement of Corrosion Resistance
One of the primary benefits of using a PVD coating machine on stainless steel sinks is the enhancement of corrosion resistance. By depositing a protective layer, the sink becomes more resistant to rust, oxidation, and chemical damage, thereby prolonging its service life even in harsh environments.
Aesthetic Appearance
PVD coatings offer a wide range of color options and finishes, allowing manufacturers to customize the appearance of stainless steel sinks. This capability enhances the visual appeal of kitchen spaces by providing sinks with elegant and upscale finishes that complement various interior designs.
Improved Cleanliness and Fingerprint Resistance
Certain PVD coatings reduce the visibility of fingerprints and smudges on stainless steel surfaces. This feature not only maintains the sink’s cleanliness but also reduces the frequency of cleaning, making it ideal for high-traffic areas such as commercial kitchens and hospitality settings.
Customizing Your Machine PVD System for Products
Understanding Product Requirements
Before customizing a Machine PVD system, it’s crucial to assess specific product requirements such as material type, dimensions, desired coating properties, and production volume. This initial phase sets the foundation for designing a tailored PVD solution.
Designing the Coating Process
Once requirements are defined, the next step involves designing the coating process. This includes selecting appropriate PVD coating materials (e.g., titanium nitride, chromium nitride), optimizing deposition parameters (temperature, pressure, deposition rate), and determining the coating thickness to achieve desired properties.
System Configuration and Integration
Foxin Vacuum Technology Company offers flexibility in system configuration, allowing integration of various modules such as pre-treatment chambers, deposition chambers, and post-treatment units. Each module can be customized to accommodate specific product dimensions and production throughput.
Key Features of Foxin’s Machine PVD Systems
Advanced Control and Monitoring Capabilities
Foxin’s Machine PVD systems are equipped with advanced control systems that ensure precise deposition control and real-time monitoring of process parameters. This enhances coating uniformity and repeatability, critical for meeting stringent quality standards.
Scalability and Flexibility
Whether for small-scale production or high-volume manufacturing, Foxin’s Machine PVD systems are designed for scalability. Modular designs allow for easy expansion and adaptation to future production needs without compromising on performance or efficiency.
Eco-Friendly and Cost-Efficient Solutions
In line with global environmental standards, Foxin integrates eco-friendly practices into their Machine PVD systems. This includes optimized energy consumption, efficient material usage, and waste reduction measures, resulting in cost-effective solutions for customers.
Case Studies: Applications Across Industries
Case Study 1: Luxury Watch Coatings
A luxury watch manufacturer partnered with Foxin to enhance the scratch resistance and aesthetics of their timepieces. By customizing a Machine PVD system, the manufacturer achieved a bespoke gold-colored coating that improved customer appeal while maintaining high durability standards.
Case Study 2: Aerospace Component Coatings
An aerospace company required PVD coatings for components subjected to extreme temperatures and corrosive environments. Foxin’s Machine PVD system delivered coatings with superior thermal stability and oxidation resistance, ensuring reliable performance under demanding conditions.
Case Study 3: Automotive Parts Coatings
In the automotive industry, parts such as engine components and decorative trims benefit from PVD coatings that offer wear resistance and decorative finishes. Foxin’s Machine PVD systems enabled automotive manufacturers to achieve desired functional and aesthetic enhancements.
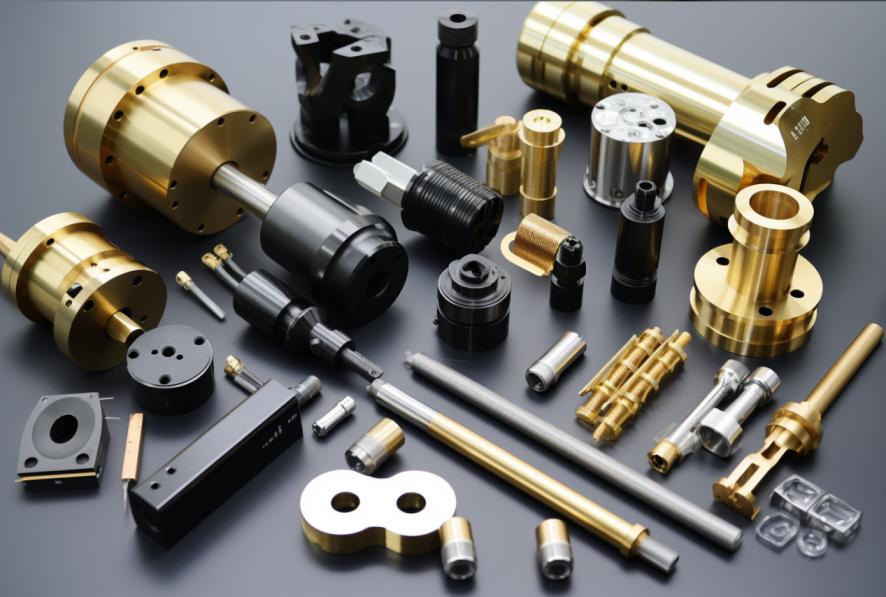
Future Trends and Innovations in PVD Technology
Looking ahead, the future of PVD technology promises continued innovation and expansion into new frontiers. Foxin Vacuum Technology Company remains committed to driving these advancements through ongoing research, collaboration with industry partners, and anticipation of market trends.
Emerging Materials and Coating Compositions
Advancements in materials science are enabling the development of new PVD coatings with enhanced properties such as increased hardness, improved thermal stability, and reduced friction. Foxin is at the forefront of integrating these materials into its systems to meet evolving industry demands.
Sustainability and Environmental Impact
As sustainability becomes a priority across industries, Foxin is exploring eco-friendly alternatives in PVD coatings and processes. Innovations in recycling of coating materials and reduction of energy consumption are central to the company’s sustainable development goals.
Integration of Industry 4.0 Technologies
Industry 4.0 principles, including IoT connectivity and data analytics, are transforming manufacturing processes. Foxin is incorporating these technologies into its PVD systems to enable predictive maintenance, optimize production workflows, and enhance overall efficiency.
Conclusion: Embracing the Future of Surface Coating
Machine PVD systems from Foxin Vacuum Technology Company represent a technological leap forward in surface coating applications across diverse industries. By offering customizable solutions tailored to specific product requirements, these systems empower manufacturers to enhance product performance, durability, and visual appeal. As industries continue to evolve, the demand for advanced PVD technologies will grow, reinforcing the pivotal role of Machine PVD systems in shaping the future of manufacturing and product innovation.