Metal Plating Process: A Simple Coating Guide
Metal plating by plating a layer of metal or alloy on the surface of an object, it can effectively improve its corrosion resistance, wear resistance and electrical conductivity, and is widely used in jewelry, automobiles and electronics.
1. Introduction to Metal Plating
Why Opt for Metal Plating
So, what exactly is metal plating? In simple terms, it’s like giving an object a shiny new jacket made of metal or alloy. Sure, it makes products look great (picture that mirror finish on stainless steel or the rich glow of gold jewelry), but the real value goes deeper. Metal plating delivers real, practical benefits. It protects items from rust, enhances durability against wear, and even amps up conductivity for electronic components.
The benefits keep coming. Metal plating can also save money. Instead of crafting something entirely out of gold, you can plate a cheaper base material with a thin layer of gold or silver. The result? Similar performance at a fraction of the cost. Factories rely on this trick for car parts, tools, and even aerospace gear. Plus, it’s a lifesaver for worn-out items. Using an electroplating machine, you can add a new metal layer to old parts, extending their life and avoiding the need for replacements. For example, a ring plated with rhodium stays bright and resists scratches because of rhodium s durability, keeping jewelry looking great for years. In short, metal plating protects, improves performance, and reduces costs. That’s a real benefit.
The Origins of Metal Plating
Metal plating didn’t just come out of nowhere. In the early 1800s, an Italian scientist named Luigi Galvani got the ball rolling with his battery experiments. By 1840, the British John Wright made the first set of gold plating and silver coating with cyanide solution, and the industry was lively, jewelry, tableware, and parts were used for metal plating.
Early metal plating was pretty basic and slow-going, not to mention risky with those cyanide mixes. But as the craft evolved, things got safer and smarter. Modern tools like PVD coating machines and vacuum coating systems stepped in, ditching messy liquid methods for cleaner approaches. Techniques like magnetron sputtering or thermal evaporation now let us stick metal onto surfaces with pinpoint precision in a vacuum, delivering top-notch quality. Today, you’ve got options: gold plating for that luxe shine, PVD coating for extra toughness, or budget-friendly coating equipment. Newer cyanide-free formulas cut down on hazards, and PVD machines produce almost no waste, making metal plating more efficient and eco-friendly than ever.
2. Metal Plating Techniques
Electroplating
When it comes to metal plating, electroplating is the original and most reliable method, using electric current to coat metal onto parts. Common jobs like zinc or nickel plating are standard in the industry. The process involves dipping the part into a solution bath, hooking it up to a DC power source, and letting metal ions deposit as a solid layer. For instance, a steel wrench gets zinc plating to resist rust, or a circuit board gets copper to boost conductivity. Factories use coating equipment to churn these out in bulk with reliable quality. That said, it requires electricity, and the waste liquid needs proper handling. In metal plating, electroplating remains a heavy hitter.
Electroless Plating
No power? No problem. Electroless plating gets metal plating done through chemical reactions. Often called chemical plating, nickel plating is a popular pick. You soak the part in a solution with metal salts and a reducing agent, and the metal sticks on its own, no electricity needed. This metal plating method handles complex shapes (think pipe interiors) and can even apply gold plating to jewelry at lower costs, keeping expenses down. It’s slower, and waste liquid still needs attention, but in metal plating, it holds its own for small-batch jobs.
Emerging Technology: The Edge of PVD
For the latest in metal plating, PVD, or Physical Vapor Deposition, takes the crown. Starting in the 1960s and hitting stride by the ’70s, it works in a vacuum, evaporating or sputtering metal onto parts without messy solutions. Thermal evaporation heats metal into a gas that settles as a thin, tough coating, built to last. That gold sheen on your phone case? Likely metal plating via PVD—clean process, next to no waste, and high efficiency.
PVD brings slick tricks like RF sputtering, using radio frequency energy to knock metal atoms off a target. It’s perfect for coating non-conductive stuff like glass or plastic with pinpoint precision. Aerospace parts and eyeglass lenses get metal plating with RF sputtering. Magnetron sputtering uses magnets to speed things up, delivering smooth coatings for watches or tools. Compared to electroplating’s waste or electroless plating’s crawl, PVD cuts hassle, ups quality, and flexes for different needs. The gear costs more upfront, but factories swear by it. Metal plating is leaning hard into PVD these days.
Quick Comparison
Method | How It Works | Pros | Cons | Trend |
---|---|---|---|---|
Electroplating | Current + Solution Tank | Fast batches, great conductivity | High power use, lots of waste | Traditional go-to, widely used |
Electroless | Chemical Reaction | Flexible shapes, low cost | Speed slow, waste messy | Handy backup, still kicking |
PVD | Vacuum Evaporation/Sputtering | Eco-friendly, top quality, durable | Gear’s pricey | Rising star, growing fast |
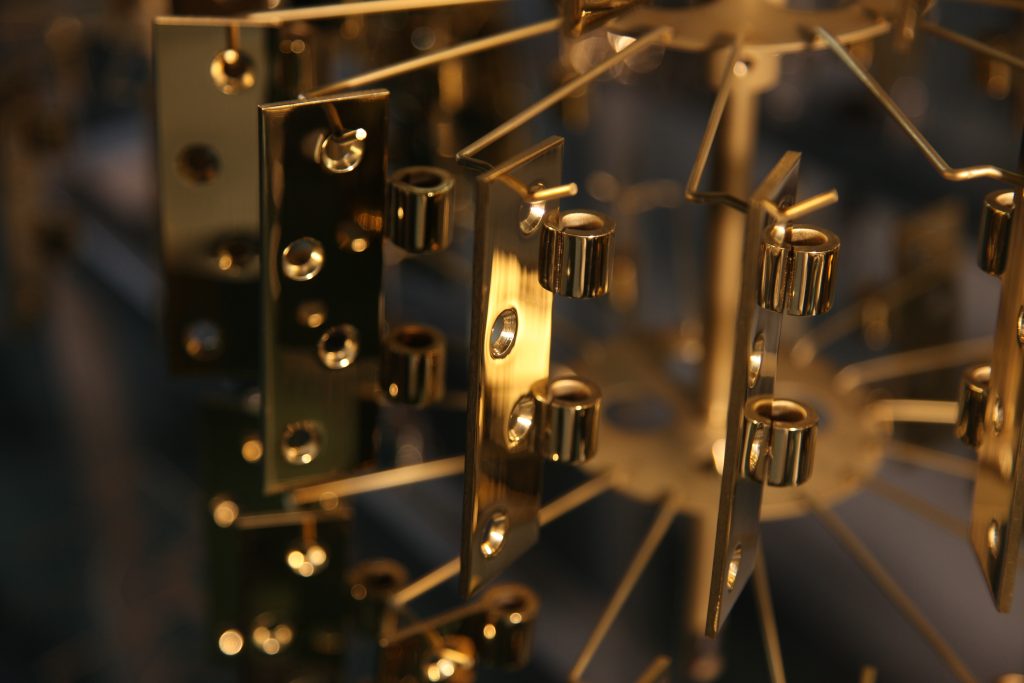
3. Types of Metal Plating
Precious Metals
In the realm of metal plating, gold and silver are the premium options. Gold plating gives jewelry a dazzling look and added durability while enhancing conductivity on circuit boards. Silver plating offers even better conductivity than gold, comes at a lower cost, and is a favorite for electrical connectors. It even has antibacterial perks for kitchen tools. Using solutions and electric currents, metal plating with these metals blends style and function seamlessly.
Industrial Metals
Metal plating is a must-have in factories, especially with metals like nickel, chromium, zinc, and copper. Nickel plating fights rust, making it ideal for car parts and tools that stay strong for years with the help of metal plating. Chrome plating is strong and bright, and it is indispensable for faucets and exhaust pipes. Zinc plating is cheap and rust-proof, screws, iron shelves by metal plating galvanized top. Copper plating conductive good, to the circuit board bottom. The coating equipment dries these metals in bulk for high efficiency electroplating.
Advanced Materials
Titanium alloy coatings are incredibly hard and corrosion-resistant, making them ideal for aerospace and medical equipment. Adding a titanium layer via metal plating boosts durability in tough environments. Palladium plating delivers conductivity and long-lasting performance, offering a budget-friendly option for electronic components with metal plating. Metal-ceramic composite coatings incorporate ceramic particles for increased hardness and heat resistance, extending tool life through a metal plating upgrade. Vacuum technology and magnetron sputtering create these coatings to be thin yet strong, advancing metal plating into cutting-edge applications.
Comparison of Metal Plating Types
Type | Features | Applications | Technique |
---|---|---|---|
Gold/Silver | High conductivity, decorative | Jewelry, circuit boards, connectors | Electroplating |
Nickel/Chromium/Zinc/Copper | Corrosion resistance, cost-effective | Car parts, faucets, screws | Electroplating/Electroless |
Advanced Materials | High hardness, heat resistance, versatile | Aerospace, medical, tools | PVD |
4. Applications of Metal Plating
Jewelry
Metal plating is the MVP of the jewelry world. Gold and silver plating can turn simple accessories into luxurious treasures. For example, adding a gold layer through metal electroplating makes necklaces and rings shiny and scratch-resistant, giving them a luxurious look. Even budget brands love using metal plating to apply a gold PVD coating , which keeps the color vibrant longer and resists scratches better than traditional plating. Silver plating is just as impressive. Earrings and bracelets coated with silver are dazzlingly bright, antibacterial, and safe to wear.
Automotive
The automotive industry can’t get enough of metal plating, especially chrome plating. Bumpers and door handles coated with chrome via metal plating turn heads with their mirror-like finish. Chrome plating offers more than just a dazzling finish. This durable coating resists wear and corrosion, holding up against tough weather and rough road conditions. Wheel rims are often plated with chrome or nickel, keeping them rust-free and strong, and looking fresh for years, even with heavy use.
In factories, coating equipment churns out these metal-plated parts at lightning speed. Picture a production line where dozens of bumpers get plated in minutes. Nickel plating often serves as a base layer, topped with chrome for double the protection and durability. Metal plating in cars isn’t just decoration—it doubles the lifespan of components.
Electronics
Metal plating is a big player in the electronics industry, and copper and gold are the main forces. Circuit boards depend on metal plating to add copper layers, ensuring top-notch conductivity for fast, reliable signals. Many circuits begin with a copper base from coating machinery, then add layers of nickel or gold to enhance performance. For critical contacts and connectors, gold plating is the top choice. It offers unmatched conductivity that lasts, while completely stopping oxidation, even after years of use.
Hardware
Hardware leans heavily on metal plating. Screws and bolts plated with zinc through metal plating offer first-rate rust protection, lasting years outdoors without a speck of corrosion. These essential fasteners are used across construction, furniture, and machinery applications where plating adds crucial durability. Take deck screws, for example: zinc plating keeps them safe from rain, saving you the hassle of constant replacements.
Zinc plating is budget-friendly, and coating equipment can handle hundreds of screws in one go. Want extra toughness? Add a nickel plating layer for double the strength.
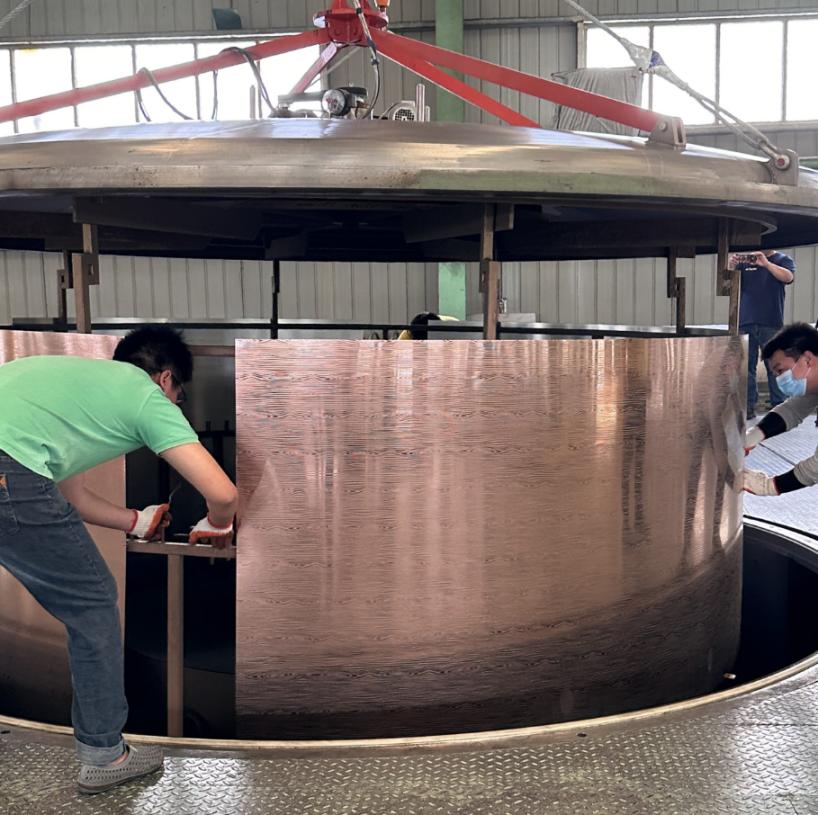
5. Environment and Safety
Managing Hazardous Substances
Metal plating involves chemicals that demand careful handling. Acids and metal salts in plating tanks, like nickel salts for nickel plating or chromic acid for chrome plating, can spell trouble for people and the planet if mishandled. Factories need sealed coating equipment to keep these risky substances under control.
How do you manage them? Here are some solid strategies:
- Strong Ventilation: Install exhaust fans in the workshop to suck out fumes and vapors, keeping the air from turning toxic.
- Proper Gear: Workers should wear gloves, masks, and, when needed, full protective suits.
- No Dumping: Used solutions, especially cyanide-rich ones from gold plating, are highly toxic and must be collected for specialized disposal.
Waste Handling and Regulations
What happens to the waste liquid and sludge after metal plating? You can’t simply dispose of the liquid waste and sludge casually because environmental regulations are strict. Take zinc solutions from galvanizing or copper salts from copper plating: they’re loaded with heavy metals. Dumping them into rivers is a disaster waiting to happen. The solution? Filter and settle them properly before release. In the U.S., the EPA enforces stringent discharge standards for metal plating waste. Failure to comply results in heavy fines and potential facility shutdowns. Coating machinery should include waste recovery systems to cut down on loss. PVD plating stands out here: it generates less waste, simplifies cleanup, and keeps things green and easy.
Here’s the step-by-step breakdown:
- Settle Heavy Metals: Add chemicals to make metal ions sink, preventing them from polluting waterways.
- Filter Wastewater: Use equipment to purify the water until it hits discharge standards.
- Hand Off Solids: Pack up solid waste and let professional companies deal with it.
Eco-Friendly Tips:
- Recycle Water: Set up a system to filter and reuse wastewater, slashing discharge volumes.
- Go Low-Toxicity: Switch to cyanide-free gold plating—it’s safer and far less toxic than older methods.
- Switch to PVD: Small shops should ditch acids for a PVD coating machine. It’s pricier upfront but pays off long-term.
- Add Sensors: Monitor waste liquids to save headaches.
Safety Note: Maintain leak-free equipment and properly dispose of waste. Following these practices ensures smoother metal plating operations.