
News
12 Year Pvd Coating Machine In Foxin
What are the key industries benefiting from PVD black coating technology?
In the realm of surface engineering, PVD (Physical Vapor Deposition) coating technology plays a pivotal role in enhancing the properties of various materials. Among its many applications, PVD black coating stands out for its dual advantages of durability and aesthetic appeal, making it a preferred choice across industries such as automotive, aerospace, medical devices, and consumer goods.
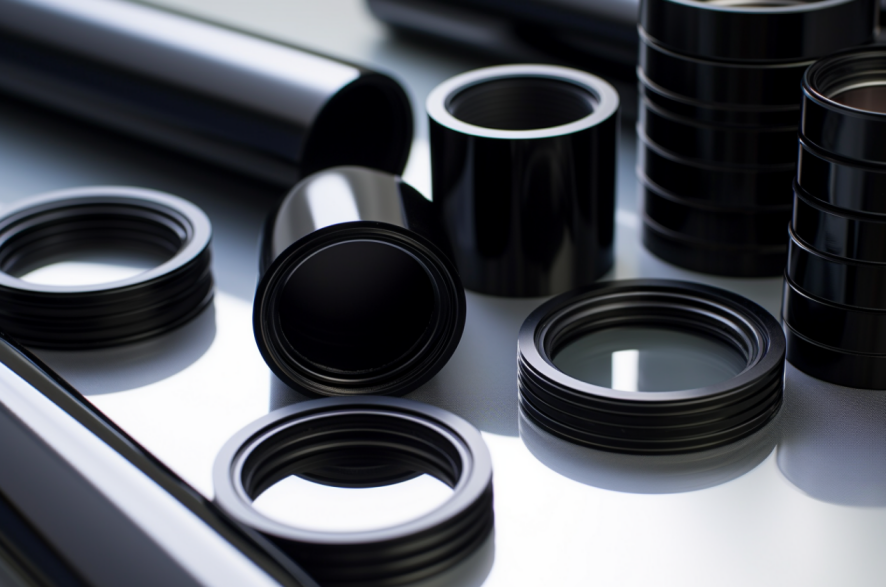
1. What is PVD Coating?
Definition and Overview of PVD Coating PVD coating is a method of surface treatment where a thin film of material is deposited onto a substrate using a vacuum environment. Unlike traditional coating methods that rely on chemical processes, PVD coating involves the physical vaporization of the coating material, which is then condensed onto the substrate to form a uniform, thin film.
How PVD Process Works and Its Advantages The PVD process begins with the preparation of the substrate in a vacuum chamber. The coating material, often in the form of solid metal or compound, is heated to evaporate it. The vaporized atoms then travel through the vacuum chamber and deposit onto the substrate’s surface, where they condense and form the desired coating. This method offers several advantages over conventional coating techniques, including better adhesion, uniformity, and the ability to coat complex shapes and geometries.
2. The Technology Behind PVD Black Coating
Detailed Explanation of PVD Black Coating PVD black coating specifically involves depositing materials that result in a black-colored finish on the substrate. The coloration is achieved through specific combinations of coating materials and deposition parameters. The process not only imparts a distinct aesthetic but also enhances the functional properties of the substrate.
Types of Materials Used in PVD Black Coatings Common materials used for achieving black PVD coatings include titanium nitride (TiN) and chromium nitride (CrN). These materials are chosen for their ability to create durable, black-colored films that offer superior performance characteristics.
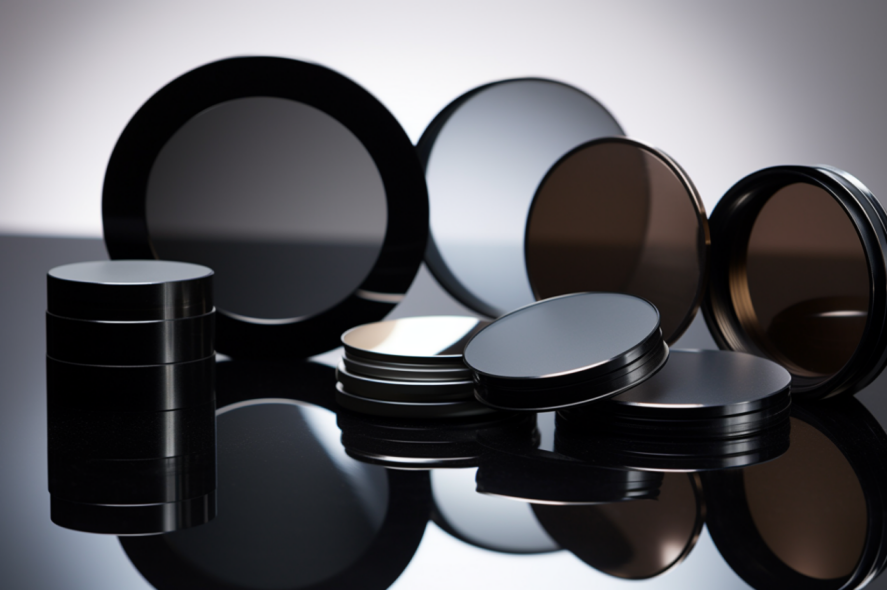
3. Advantages of PVD Black Coating
Benefits in Terms of Durability and Performance Enhancement PVD black coatings are renowned for significantly improving the substrate’s durability and performance. They provide enhanced wear resistance, making components last longer under abrasive conditions. Moreover, the coatings offer superior corrosion resistance, protecting the substrate from environmental factors that could degrade its integrity over time.
Improved Wear Resistance One of the primary advantages of PVD black coatings is their ability to withstand wear and abrasion better than untreated surfaces. This is crucial in industries such as automotive and machining, where components are subjected to high levels of friction and mechanical stress.
Enhanced Corrosion Resistance The corrosion resistance of PVD black coatings helps protect substrates from chemical exposure and environmental elements. This property is particularly valuable in outdoor applications, marine environments, and medical devices where exposure to bodily fluids or sterilization processes can degrade materials over time.
Surface Hardness PVD black coatings typically increase the surface hardness of substrates, thereby improving their resistance to scratches and impacts. This attribute is beneficial in applications where the substrate must maintain its structural integrity despite frequent handling or mechanical stress.
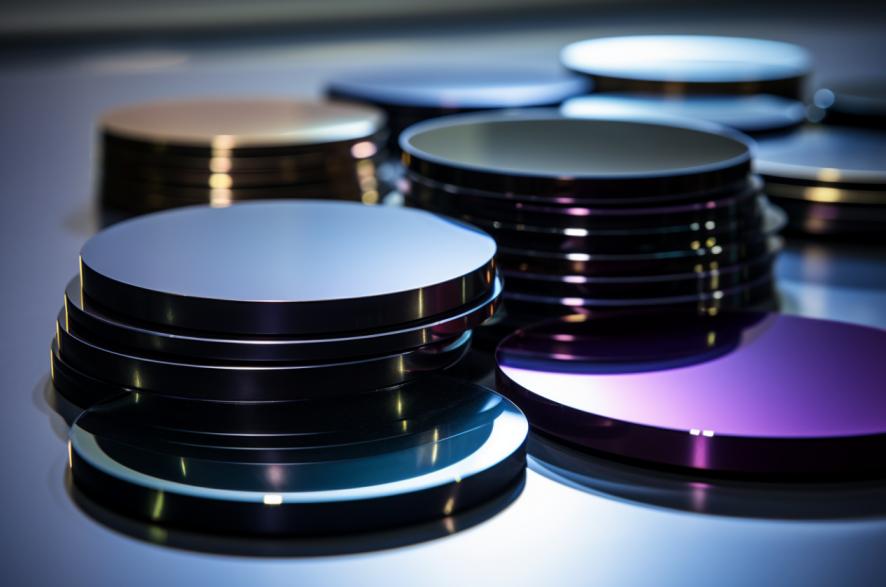
4. Considerations in PVD Black Coating
Achieving high-quality PVD black coatings involves careful consideration of several factors that influence performance and durability:
Substrate Preparation Proper cleaning and surface preparation of the substrate are critical to ensuring adhesion and uniformity of the PVD black coating. Any contaminants or surface irregularities can compromise the coating’s integrity and performance.
Process Parameters Optimal deposition parameters, including temperature, pressure, and deposition rate, must be carefully controlled to achieve the desired thickness, hardness, and adhesion strength of the PVD black coating. Variations in these parameters can affect coating uniformity and quality.
Coating Thickness The thickness of the PVD black coating directly impacts its properties such as hardness, wear resistance, and visual appearance. Precise control over coating thickness ensures consistency and meets specific performance requirements for different applications.
Vacuum Quality Maintaining high vacuum levels during the deposition process is crucial to minimize impurities and ensure the purity of the deposited coating. This significantly affects the final properties of the PVD black coating, including its adhesion and corrosion resistance.
Choice of Coating Materials The selection of coating materials, such as titanium nitride (TiN) or chromium nitride (CrN), influences the color, hardness, and performance characteristics of the PVD black coating. Advances in material science continue to expand the range of options available for achieving specific aesthetic and functional goals.
Adhesion Promotion Techniques To enhance adhesion between the substrate and the PVD black coating, various surface treatments and adhesion promotion techniques, such as ion etching or pre-coating with intermediate layers, are employed. These techniques improve the reliability and longevity of the coating in demanding applications.
6. Future Trends and Innovations in PVD Technology for Black Coatings
As technology advances, the field of PVD black coatings continues to evolve, driven by innovation and emerging trends:
Multilayer Coatings Advancements in PVD technology enable the deposition of multilayered coatings with tailored properties, combining different materials and thicknesses to achieve superior performance in terms of wear resistance, corrosion protection, and aesthetic appeal.
Nanostructured Coatings The development of nanostructured PVD coatings offers enhanced mechanical properties and surface functionalities, such as self-cleaning or antibacterial properties, opening new possibilities in medical and consumer electronics applications.
Sustainable Coating Solutions There is a growing emphasis on developing environmentally friendly PVD processes and materials that minimize energy consumption, waste generation, and the use of hazardous substances, aligning with global sustainability goals.
Functional Coatings Future advancements may include the integration of functional additives or nanoparticles into PVD coatings to impart unique properties such as conductivity, magnetic responsiveness, or enhanced thermal management, expanding their applications in electronics and advanced manufacturing.
Customized Coating Solutions Advances in digital manufacturing technologies and computational modeling are expected to enable the customization of PVD black coatings according to specific performance requirements, offering tailored solutions for diverse industries and applications.
Enhanced Durability and Performance Continuous research into improving the mechanical and tribological properties of PVD coatings will lead to coatings that can withstand more demanding operating conditions in aerospace, automotive, and industrial applications.
Conclusion
In conclusion, PVD black coating technology represents a significant advancement in surface engineering, offering both aesthetic appeal and functional benefits across various industries. Manufacturers like Foxin Vacuum Technology Company specialize in delivering high-quality PVD black coatings that meet stringent performance standards. Whether for automotive components, medical instruments, or consumer electronics, the application of PVD black coatings continues to expand, driven by their ability to enhance durability and maintain a sleek appearance.