PVD Coating: A Guide to Replace Chrome Plating
If you’re in a factory trying to make parts tougher, sharper-looking, and eco-friendly, chrome plating and PVD coating are worth a look. Chrome plating, the go-to surface treatment back in the 20th century, was huge for car rims, faucets, and tools. But now, with environmental heat and health concerns, it’s losing ground. PVD coating, with its green and efficient vibe, is stepping up to replace chrome plating.
1. Chrome Plating vs. PVD: The Basics
1.1 How Chrome Plating Works
Chrome plating is an electrochemical process that slaps a layer of chromium onto a part’s surface, usually 5-50 microns thick. You dip the part in a hexavalent chromium solution, crank up the electricity, and chromium ions stick to the surface, giving you a shiny, tough finish. Back in the 20th century, this was the go-to for car parts, bathroom fixtures, and industrial gear. That mirror-like gloss pops, and it holds up decently against corrosion.
Sounds easy, but it’s a pain. The plating bath needs to stay at 50-60°C, and if the current wobbles, you’re stuck with uneven or bubbly coatings. Hardness clocks in at 800-1000 Vickers, meets ISO 14001, but it guzzles power like nobody’s business, around 200-300 kWh per square meter. Polishing and cleaning are a slog, and wastewater treatment is a chemical nightmare. Mess it up, and you’re breaking rules with costs piling up fast.
1.2 What’s PVD Coating
PVD coating uses physical vapor deposition to lay down ultra-thin layers, 0.5-5 microns, on a surface in a vacuum. It’s all about vacuum technology, where you either sputter or evaporate material atoms onto the part. Some call it PVD plating.
- Sputtering: Like flinging confetti, it sticks material to the surface, great for tough coatings like titanium nitride. Magnetron sputtering and RF sputtering make it faster and smoother.
- Thermal evaporation: Heat the target material until it vaporizes, then let the vapor settle on the part. Perfect for gold PVD coatings.
This process nails precision on thickness, color, and performance. It’s a favorite for stainless steel surfaces and high-end gold jewelry. Compared to chemical vapor deposition, PVD runs cooler, 200-500°C, so parts don’t warp. It’s way more efficient than chrome plating.
1.3 Why Chrome Plating Fails & PVD Rises
Chrome plating’s got issues. Hexavalent chromium is toxic, and wastewater treatment costs snowball, $200-500 per ton. It’s a power hog with a ton of steps, and coatings can fail in heat or salty coastal air. Parts by the sea might rust in six months. Plus, plastics or alloys don’t play nice with it, limiting its use.
Global rules are cracking down on chrome plating. The EU’s RoHS and REACH have hexavalent chromium on the naughty list, with tighter restrictions since 2024. PVD coating is stepping up as the chrome plating alternative. Zero waste, killer performance, and it fits ISO 14001 and green manufacturing like a glove. It’s the new hotshot replacing chrome plating.
2. Chrome Plating Issues & PVD’s Advantage
2.1 Chrome Plating’s Environmental Risks
Chrome plating uses hexavalent chromium, and the wastewater and solid waste are seriously toxic. Treating this stuff is a pain and costs a fortune, like 200 to 500 bucks per ton of wastewater. Total cost killer. Workers around hexavalent chromium for too long? They’re looking at higher risks of lung cancer and skin issues. Companies get stuck with medical bills and legal headaches.
In 2023, a plating shop in Michigan got slapped with a 500,000-dollar fine for wastewater violations. Even small shops can get hit with 100,000-dollar penalties. The environmental pressure on chrome plating is no joke. The EU’s REACH regulations got tougher on hexavalent chromium in 2024. Manufacturers who don’t switch are out of luck.
2.2 PVD’s Green Game
PVD gets it done in a vacuum coating machine, no chemical solvents, and barely any waste. Sputter deposition or thermal evaporation slaps the material right onto parts, meeting EU RoHS and ISO 14001 standards. It helps factories breeze through environmental checks with pvd finishing and saves a ton on waste disposal costs every year.
PVD coating equipment is fully sealed, so workers don’t touch harmful chemicals. Super safe. Take chromium nitride coating, for example, production is highly automated, and the shop runs smooth. This pvd coating technology keeps factories green and efficient, standing out big time.
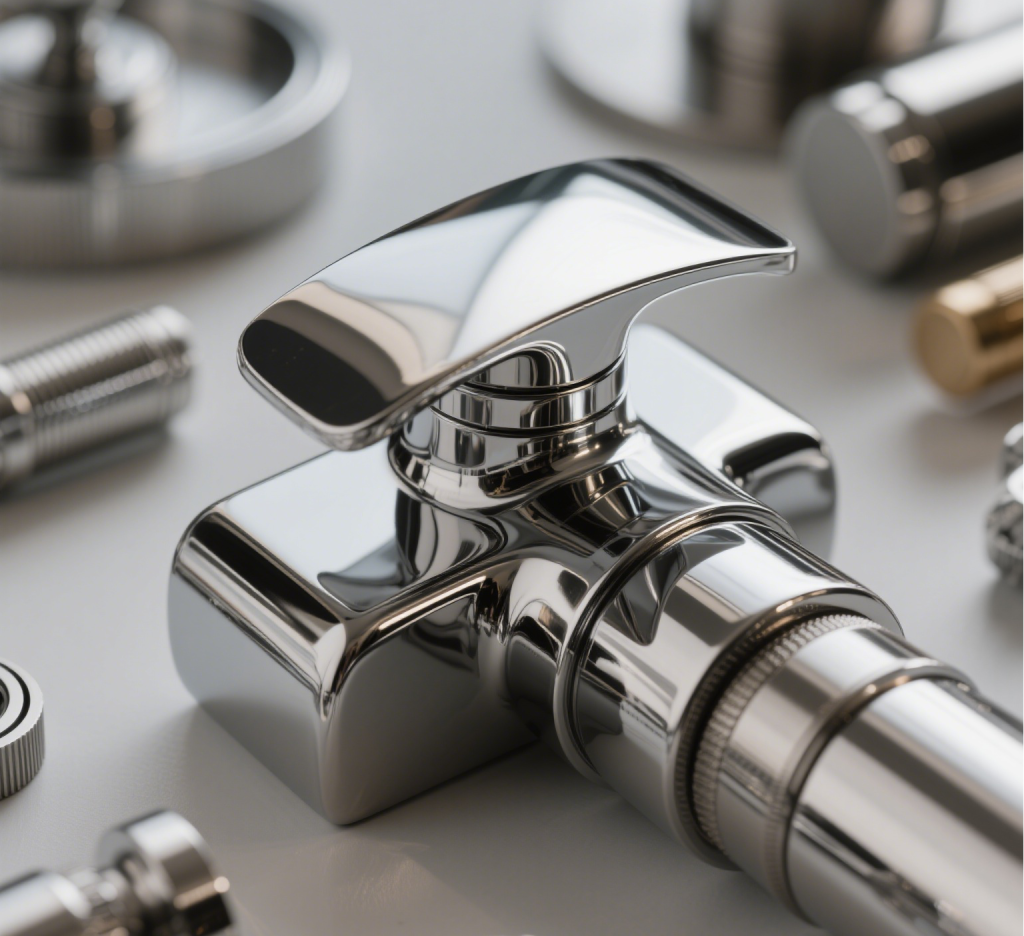
3. Chrome Plating vs. PVD: Performance Battle
3.1 Hardness Throwdown
Chrome plating hits a hardness of 800-1000 Vickers. It’s decent for light wear but flops under heavy friction. PVD coated stuff, like chromium nitride, rockets to 2200 Vickers, laughing off scratches and wear.
In the cutting tool game, chrome plating tools crap out in 3-6 months. Titanium nitride coating from PVD lasts 12-18 months. A shop in Ohio switched to PVD coated tools in 2023, slashed tool swaps by 60%, and boosted efficiency like nobody’s business.
3.2 Durability Face-Off
Metal plating chokes in heat or salty conditions. The layer peels, and parts die fast. Coastal stainless steel parts rust in six months. PVD coated parts, with their super-tight sputtered structure, act like a shield. Thin but tough, they crush corrosion.
In hot engines, PVD stretches piston ring life by 50%. Near the ocean, PVD coated stainless steel cuts corrosion rates by 60%. Chrome plating doesn’t stand a chance.
3.3 Looks and Strength Combo
Chrome plating owns the shiny decorative coating scene. Think car trim or faucets. But scratches and fading are a pain. PVD finishing matches the shine, plus you get slick options like gold PVD or black coatings that are tough and pretty.
Gold coating makes decorative pieces fancy and durable, with way less maintenance. Gold electroplating scratches up in daily use, getting smoked by PVD in high-end settings.
4. Switching from Chrome Plating to PVD Uses
4.1 Automotive Industry
Chrome plating used to be the go-to for car rims and badges, but it’s a pain with low durability and tons of waste. PVD coating is the new hotshot. Titanium nitride coating and DLC are slapped on piston rings and valves, cutting wear and friction big time.
A mid-size German car brand in 2024 threw PVD coating on racecar engine parts. Lifespan jumped 40%, and fuel efficiency climbed 5%. Chrome plating ages fast in hot engines, but gold PVD coating boosts badges and interior pieces with style and toughness. Chrome can’t touch that.
4.2 Aerospace
Aerospace demands top-notch materials. Chrome plating struggles with weak adhesion and lousy high-temp performance. It’s falling behind. PVD coating, using rf sputtering, slaps tough protection on turbine blades and fasteners. Titanium nitride coating slashes corrosion rates by 70% in salty environments.
A British jet engine shop in 2023 coated Boeing 737 engine parts with PVD coating stainless steel. Maintenance costs dropped 30%. Vacuum technology ensures even coverage on tricky shapes. Chrome plating doesn’t stand a chance.
4.3 General Manufacturing
Chrome plating on molds and bearings wears out fast in high-friction setups. PVD coating, with its DLC, brings low friction and high hardness. Pumps, molds, even kitchen tools love it. One pump factory stretched maintenance cycles from 6 months to 18 with a PVD coating machine, saving 40% on downtime costs.
A faucet maker used PVD for corrosion resistant coating, fixing color fade in humid spots and cutting defects by 25%. From faucets to non-stick, scratch-proof cookware, PVD makes hardware tougher and sharper-looking. Manufacturing’s switching gears, and PVD coating solution is driving it.
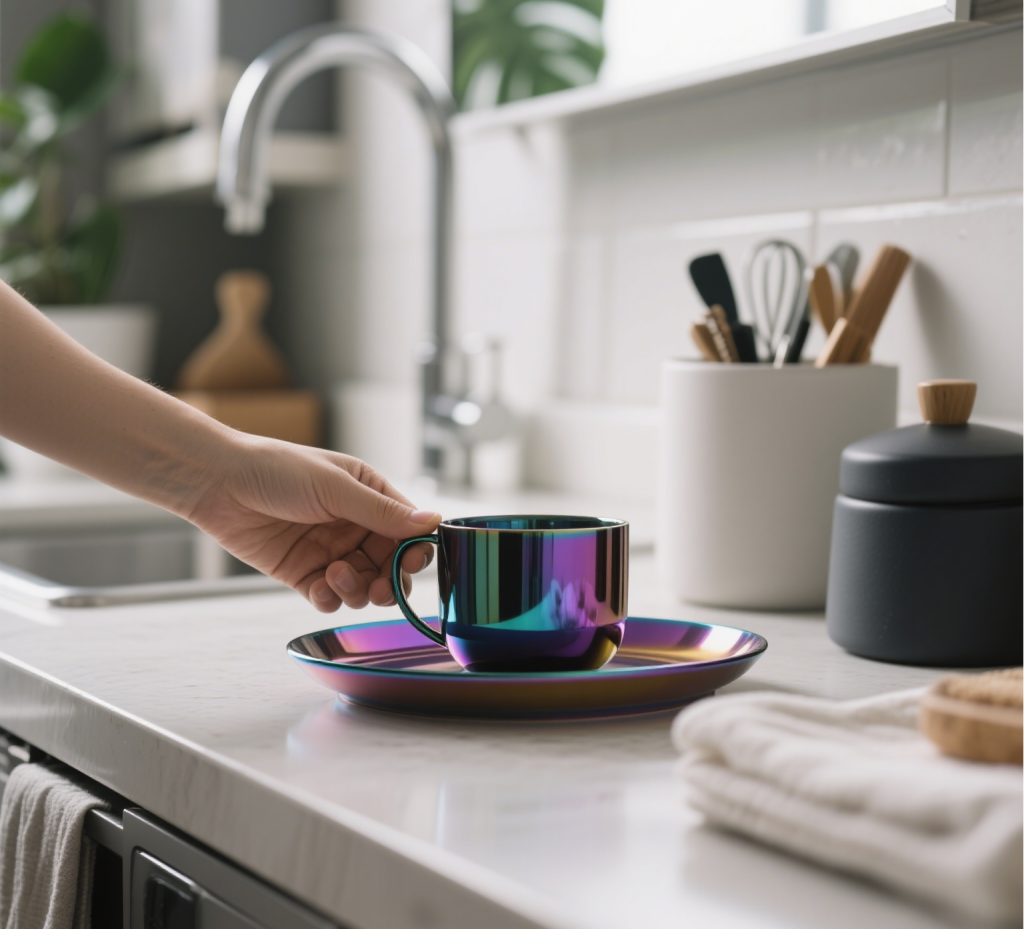
5. Economic & Production Benefits
5.1 Maintenance Costs Slashed
Chrome plating seems cheap up front, but you’re stuck with frequent maintenance and hefty wastewater treatment bills. It’s a losing game long-term. PVD coatings, with their high hardness and corrosion resistance, make parts last longer right away. Chromium nitride coatings extend tool life from 3 months to 12 months, cutting maintenance costs by 20%.
PVD-coated stainless steel drops after-sales repair rates by 15%. Sure, PVD coating prices are higher at first, but the long-term payoff crushes chrome plating.
5.2 Production Efficiency Doubled
Chrome plating is a slog—polishing, cleaning, multiple steps, long cycles, and high scrap rates. PVD coating equipment, with its automated design, runs like a sports car, boosting efficiency at every step. DC sputtering or thermal evaporation gets deposition done in one go, saving time and effort.
A bathroom fittings factory using PVD for gold decorative finishes cut production time from 3 days to 1 day and reduced scrap rates by 30%. Vacuum coating machines deliver reliable quality with less hassle, leaving chrome plating in the dust.
6. How Factories Use PVD
6.1 Figuring Out What You Need
First step in using PVD is knowing what you want. Different parts and their performance need the right coating type. Here’s what’s common:
- CrN Coating: Super hard and wear-resistant, great for car piston rings or cutting tools.
- Titanium Nitride Coating: Fights corrosion, has a gold look, perfect for stainless steel or gold decorations.
- DLC Coating: Crazy low friction, ideal for bearings, pumps, or molds.
When figuring this out, think about the part’s environment. Is it hot, wet, or dealing with acidic corrosion? How long should it last? Plastic parts might need plasma cleaning first to make the coating stick. Pick the right coating, and a valve could run 500 hours longer, doubling efficiency. Tight budget at a small shop? We can find a cheap option nearby.
6.2 Gear and Testing
Once you pick the coating, next up is getting the right PVD coating machine and running tests. Modern PVD systems are modular, supporting sputtering or thermal evaporation tech, so they work for different production sizes. Here’s how it goes:
- Pick the Machine: Based on output and part size, choose a PVD coating machine. Small factories can go for compact systems, while big production needs multi-chamber setups. Make sure the machine has vacuum technology for top-notch coating quality.
- Test Samples: Before full production, test the PVD coating process on samples. Check hardness, corrosion resistance, and friction. One mold maker found DLC coating boosted mold life by 50% after testing.
- Tweak Settings: Use test results to adjust coating thickness, deposition speed, or target material like chromium or titanium to hit your performance goals.
Wrap-Up and Next Steps
PVD coating is a green, high-performance, and versatile way to beat out chrome plating. From cars to aerospace, PVD makes parts tougher, prettier, and saves cash and hassle. Want more info on PVD coating machines? Hit us up for a free consultation on your custom plan!