PVD Coating Stainless Steel: Process & Benefits
PVD coating, also known as physical vapor deposition, has become a popular and effective way to coat metals. This cutting-edge technology offers a way to significantly enhance the properties of stainless steel, providing a myriad of benefits. But what exactly is PVD coating? PVD coating is a process that involves the deposition of a thin film of material onto the surface of a substrate, in this case, stainless steel. Let’s delve deeper into the purpose and advantages of PVD coating on stainless steel.
Purpose of PVD Coating on Stainless Steel
Stainless steel is renowned for its corrosion resistance and durability. However, it can still benefit from additional enhancements, especially when used in demanding applications. PVD coating serves several crucial purposes when applied to stainless steel. First and foremost, it enhances the aesthetic appeal of stainless steel surfaces, offering a range of colors and finishes. Beyond aesthetics, PVD Coating Stainless Steel also improves the material’s hardness, wear resistance, and overall performance, making it an ideal choice for various industries, including automotive, architecture, and electronics.
PVD Coating Stainless Steel: Advantages of PVD Coating
PVD coating on stainless steel provides an array of advantages that make it a popular choice in many applications:
1. Enhanced Aesthetics: PVD coatings can create visually stunning finishes on stainless steel, including gold, rose gold, black, and more. This opens up new design possibilities in architecture and product manufacturing.
2. Increased Hardness: The coating process significantly increases the hardness of the stainless steel, making it more resistant to scratches, wear, and damage. This is particularly valuable in high-traffic areas or components subject to abrasive forces.
3. Improved Corrosion Resistance: While stainless steel is naturally corrosion-resistant, PVD coatings can enhance this property, making it even more impervious to environmental factors, such as saltwater or harsh chemicals.
4. Temperature and Chemical Resistance: PVD coatings can be tailored to withstand extreme temperatures and exposure to various chemicals, further expanding the potential applications of coated stainless steel.
5. Reduced Friction: Coated stainless steel surfaces exhibit reduced friction, making them ideal for sliding or moving parts where smooth operation is critical.
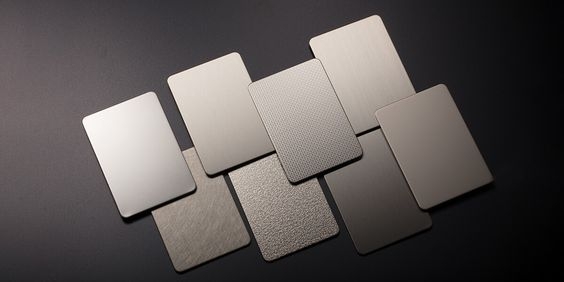
PVD Coating Stainless Steel: Process of PVD Coating
Now that we understand the purpose and advantages of PVD coating, let’s explore the intricate process behind it:
I. Vacuum Chamber Setup
PVD coating begins in a controlled environment inside a vacuum chamber. In this sealed chamber, air is removed to create a low-pressure environment conducive to the deposition process. Foxin Vacuum Technology Company is a renowned manufacturer of PVD coating machines, ensuring precise and reliable equipment for this crucial step.
II. Selection of Coating Material
The choice of coating material is a pivotal decision in the PVD process. Common materials used for PVD coating on stainless steel include titanium nitride, chromium nitride, and zirconium nitride, each offering unique properties and aesthetic possibilities.
III. Cleaning and Preparation of the Stainless Steel Substrate
Before coating, the stainless steel substrate undergoes rigorous cleaning and preparation to remove any contaminants, ensuring optimal adhesion of the PVD film.
IV. Deposition Process
The deposition of the thin film material onto the stainless steel substrate occurs through two primary methods:
1. Evaporation: This process involves heating the coating material in a vacuum until it vaporizes. The vaporized material then condenses on the stainless steel surface, forming a thin film.
2. Sputtering: In sputtering, gas ions bombard a solid target made of the coating material, causing atoms to be ejected from the target and deposited onto the substrate.
V. Film Growth and Adherence to the Substrate
During the deposition process, the vaporized or sputtered material gradually forms a thin film on the stainless steel substrate. The film adheres tightly to the substrate, ensuring the durability and longevity of the coating.
PVD Coating on Stainless Steel: Considerations and Limitations
I. Thickness of the PVD Coating
One crucial aspect to consider when opting for PVD Coating Stainless Steel is the thickness of the coating. PVD coatings are typically thin films, with thicknesses ranging from 0.2 to 5 microns. While this thinness can offer benefits such as preserving the material’s original dimensions and surface finish, it also means that PVD coatings may not be suitable for applications where a thicker layer is required for added protection or wear resistance. Users must carefully assess the intended purpose of the coated stainless steel component to determine if the PVD coating thickness meets their requirements.
II. Surface Preparation Requirements
Achieving a successful PVD coating on stainless steel necessitates meticulous surface preparation. The surface must be free from contaminants, oxides, and imperfections to ensure proper adhesion of the PVD coating. Manufacturers often employ techniques like abrasive blasting, chemical cleaning, and ion bombardment to prepare the surface. The quality of the surface preparation can significantly impact the coating’s adhesion and longevity, making it imperative to entrust this process to experienced professionals.
III. Cost Considerations
Cost is a critical factor in any coating decision. PVD coating on stainless steel can be more expensive than some alternative methods, such as electroplating or painting. The cost depends on various factors, including the size of the component, the complexity of the design, the choice of coating material, and the quality of surface preparation. While PVD coatings offer excellent longevity and quality, potential users should weigh these benefits against the initial investment to determine if they align with their budget.
IV. Limited Coating Size and Geometry Options
PVD coating technology has certain limitations regarding the size and geometry of the components that can be coated effectively. Complex shapes or components with intricate internal features may pose challenges in achieving uniform coating coverage. Moreover, large components may require specialized equipment, which can increase the cost and complexity of the coating process. Users should consult with experienced PVD coating providers, such as Foxin Vacuum Technology Company, to assess the feasibility of coating specific stainless steel parts.
V. Wear and Maintenance Considerations
PVD coatings on stainless steel offer excellent wear resistance and can prolong the lifespan of components subjected to abrasive or corrosive environments. However, it’s essential to acknowledge that all coatings will eventually wear down over time, especially in high-stress applications. Regular maintenance and proper care are necessary to maximize the lifespan of PVD-coated stainless steel components. Understanding the expected wear patterns and having a maintenance plan in place are crucial aspects of ensuring the long-term performance of coated materials.
Conclusion
PVD Coating Stainless Steel is a transformative process that elevates both the aesthetics and performance of this already impressive material. Thanks to manufacturers like Foxin Vacuum Technology Company and their state-of-the-art machines, the PVD coating industry continues to push boundaries, opening up new possibilities for a wide range of industries. Whether it’s enhancing the appearance of architectural structures or improving the durability of precision components, PVD coating on stainless steel is a technology that’s here to stay, shaping the future of material engineering.