PVD Coating vs Powder Coating: Which is Better
PVD coating is ideal for high-precision, high-performance needs like cutting tools and medical devices, while powder coating is better suited for large-scale, cost-effective applications such as construction and home appliances. The choice depends on your specific requirements and budget.
Introduction to PVD Coating
PVD (Physical Vapor Deposition) is a technique that deposits material onto a substrate in a vacuum environment using physical methods. Simply put, it transforms target materials like titanium, chromium, or aluminum into a gaseous state, which then forms a dense film on the substrate surface. The coating thickness typically ranges from 1-5 microns, which may seem thin but delivers impressive results.
In industrial applications, PVD coating is highly valued for its “high adhesion.” Imagine a coating that stays firmly attached to the substrate even under high temperatures or heavy loads. For example, in tool manufacturing, PVD coating significantly enhances the “wear resistance” and “corrosion resistance” of cutting tools, making them perform exceptionally well in machining tasks.
However, PVD coating requires strict process conditions. It needs to be carried out in a vacuum environment with a pressure range of 10^-3 to 10^-6 Torr, and the deposition temperature can reach 200-500°C. This high-precision process ensures the coating’s uniformity and stability but also makes PVD coating relatively expensive. Despite the cost, it remains a top choice in high-end manufacturing sectors like aerospace, medical devices, and precision molds.
Compared to traditional chemical coatings, PVD coating also has an “eco-friendly” advantage. The entire process doesn’t involve harmful chemicals, aligning with modern manufacturing’s green production standards. Additionally, PVD coatings come in various colors like gold, black, and blue, catering to different decorative needs.
In practical applications, the performance of PVD coatings is closely tied to process parameters. For instance, under load fluctuations ranging from 10-50 N, the wear resistance of PVD coatings can be 3-5 times higher than traditional coatings. This significant performance boost makes it an ideal choice for demanding industrial applications.
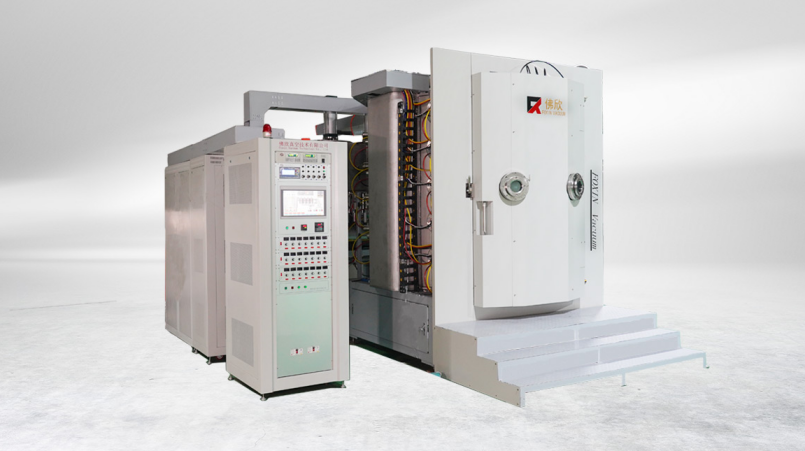
Introduction to Powder Coating
Powder coating is a technique where dry powder paint is applied to a substrate using electrostatic spraying or fluidized bed processes, followed by heating to cure the coating. This process operates at room temperature, with curing temperatures ranging from 150-200°C, making it suitable for mass production. The coating thickness typically ranges from 50-150 microns, depending on the type of powder and process parameters.
In industrial applications, powder coating is known for its “high coverage” properties. This ensures the coating evenly covers complex-shaped substrates, even in corners or recesses. For example, in appliance manufacturing, powder coating provides excellent “weather resistance” and protects against environmental factors like UV rays and acid rain.
Powder coating’s process conditions are relatively flexible, with spraying voltages ranging from 30-100 kV and curing times between 10-30 minutes. This flexibility makes powder coating ideal for large-scale production, especially in industries like construction, automotive, and furniture. Compared to traditional liquid paints, powder coating has a “zero VOC emission” advantage, meeting modern manufacturing’s environmental standards.
In practical applications, the performance of powder coatings depends on their formulation and process parameters. For instance, under temperature fluctuations ranging from -20°C to 80°C, powder coatings maintain stable “chemical resistance,” effectively preventing substrate corrosion or oxidation. Additionally, powder coatings offer a wide range of colors and textures, such as matte, gloss, and metallic finishes, catering to various decorative needs.
The cost-effectiveness of powder coating is another reason for its popularity. With a paint utilization rate of over 95% and no need for solvents, production costs are significantly reduced. This affordability makes it the go-to choice for mid-to-low-end markets, especially in large-scale coating applications.
The Role and Advantages of PVD Coating
PVD coating plays a crucial role in modern industries, particularly in high-precision and high-performance sectors. This technique deposits materials onto a substrate in a vacuum environment, forming a dense film that significantly enhances the substrate’s properties. The coating thickness typically ranges from 1-5 microns, depending on application needs.
In tool manufacturing, PVD coating is renowned for its “high hardness,” making tools perform exceptionally well in cutting tasks. For example, under load fluctuations ranging from 10-50 N, PVD-coated tools have a significantly longer lifespan. Additionally, PVD coating improves the substrate’s “corrosion resistance,” protecting it from corrosive agents and extending its service life.
PVD coating’s process conditions are stringent, typically requiring a vacuum environment with a pressure range of 10^-3 to 10^-6 Torr and deposition temperatures of 200-500°C. This high-precision process ensures coating uniformity and stability but also makes PVD coating relatively expensive. Despite the cost, it remains a top choice in high-end manufacturing sectors like aerospace, medical devices, and precision molds.
Compared to traditional chemical coatings, PVD coating has an “eco-friendly” advantage. The entire process doesn’t involve harmful chemicals, aligning with modern manufacturing’s green production standards. Additionally, PVD coatings come in various colors, catering to different decorative needs.
In practical applications, the performance of PVD coatings is closely tied to process parameters. For instance, under temperature fluctuations ranging from -50°C to 300°C, PVD coatings maintain stable “thermal resistance,” preventing coating failure. This significant performance boost makes it an ideal choice for demanding industrial applications.
Key Advantages of PVD Coating
- High hardness: Significantly enhances wear resistance.
- Corrosion resistance: Protects substrates from corrosive agents.
- Eco-friendliness: No harmful chemicals involved in the process.
- Aesthetic appeal: Available in various colors for decorative purposes.
- Thermal resistance: Maintains stability under high temperatures.
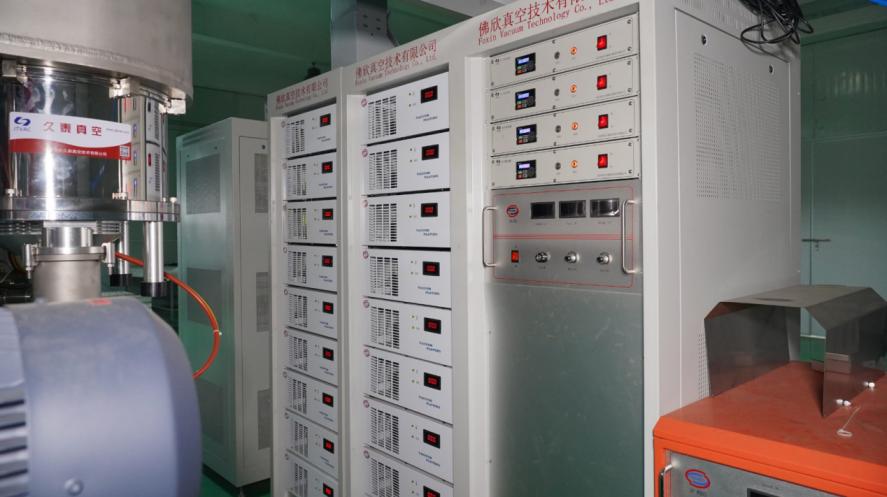
The Role and Advantages of Powder Coating
Powder coating is a widely used surface treatment technology in industrial applications, known for its efficiency, eco-friendliness, and versatility. Through electrostatic spraying or fluidized bed processes, powder paint is evenly applied to a substrate and then cured at temperatures ranging from 150-200°C, forming a dense protective layer. The coating thickness typically ranges from 50-150 microns, depending on the type of powder and process parameters.
In construction and appliance manufacturing, powder coating is known for its “high coverage,” ensuring even protection on complex-shaped substrates. For example, under temperature fluctuations ranging from -20°C to 80°C, powder coatings exhibit excellent “weather resistance,” protecting against UV rays, acid rain, and other environmental factors.
Powder coating’s process conditions are relatively flexible, with spraying voltages ranging from 30-100 kV and curing times between 10-30 minutes. This flexibility makes it ideal for large-scale production, especially in scenarios requiring quick coating. Compared to traditional liquid paints, powder coating has a “zero VOC emission” advantage, meeting modern manufacturing’s environmental standards.
In practical applications, the performance of powder coatings depends on their formulation and process parameters. For instance, under load fluctuations ranging from 5-20 N, powder coatings maintain stable “wear resistance,” effectively extending substrate lifespan. Additionally, powder coatings offer a wide range of colors and textures, catering to various decorative needs.
The cost-effectiveness of powder coating is another reason for its popularity. With a paint utilization rate of over 95% and no need for solvents, production costs are significantly reduced. This affordability makes it the go-to choice for mid-to-low-end markets, especially in large-scale coating applications.
Key Advantages of Powder Coating
- High coverage: Ensures even protection on complex shapes.
- Weather resistance: Maintains performance in harsh environments.
- Eco-friendliness: Zero VOC emissions, aligning with green production.
- Versatility: Available in various colors and textures for decorative needs.
- Cost-effectiveness: High paint utilization and low production costs.
Comparative Analysis of Both Coatings
PVD coating and powder coating are two widely used surface treatment technologies in industrial applications, each with unique advantages and suitable scenarios. By comparing their performance, processes, and cost-effectiveness, we can better understand which technology suits specific needs.
From a performance perspective, PVD coating is known for its “high hardness” and “corrosion resistance.” Under load fluctuations ranging from 10-50 N, PVD coatings can be 3-5 times more wear-resistant than traditional coatings, making them ideal for high-precision and high-performance industrial components. Powder coating excels in “weather resistance” and “chemical resistance,” effectively protecting against environmental factors like UV rays and acid rain under temperature fluctuations ranging from -20°C to 80°C.
In terms of process conditions, PVD coating requires a vacuum environment with a pressure range of 10^-3 to 10^-6 Torr and deposition temperatures of 200-500°C. This high-precision process ensures coating uniformity and stability but also makes PVD coating relatively expensive. Powder coating’s process conditions are more flexible, with spraying voltages ranging from 30-100 kV and curing times between 10-30 minutes, making it ideal for large-scale production.
From a cost perspective, powder coating’s “high coverage” and “zero VOC emission” advantages make it the preferred choice for mid-to-low-end markets. With a paint utilization rate of over 95%, production costs are significantly lower. PVD coating, while more expensive, offers “eco-friendliness” and “aesthetic appeal,” making it a top choice in high-end manufacturing sectors like aerospace, medical devices, and precision molds.
Parameter Comparison Table
Parameter | PVD Coating | Powder Coating |
---|---|---|
Thickness Range | 1-5 microns | 50-150 microns |
Process Environment | Vacuum (10^-3-10^-6 Torr) | Room temperature |
Temperature Range | 200-500°C | 150-200°C |
Wear Resistance | 3-5 times higher | Moderate |
Weather Resistance | Moderate | Excellent |
Eco-friendliness | No harmful chemicals | Zero VOC emissions |
Cost-effectiveness | High cost | Low cost |
Key Comparison Points
- Performance: PVD coating excels in hardness and corrosion resistance, while powder coating performs better in weather and chemical resistance.
- Process: PVD coating’s process is complex and costly, while powder coating’s process is simple and suitable for mass production.
- Cost-effectiveness: Powder coating is cost-effective for mid-to-low-end markets, while PVD coating is more expensive but ideal for high-end manufacturing.
Conclusion and Selection Advice
PVD coating and powder coating each have unique advantages and suitable scenarios. The choice depends on your specific application needs, budget, and performance requirements. Here are some practical tips to help you make an informed decision.
If you need high-precision, high-performance coatings, especially with strict requirements for “hardness” and “corrosion resistance,” PVD coating is the better choice. For example, under load fluctuations ranging from 10-50 N, PVD coatings can be 3-5 times more wear-resistant, making them ideal for cutting tools, precision molds, and medical devices. Additionally, PVD coating’s “eco-friendliness” and “aesthetic appeal” make it a popular choice for decorative products.
For large-scale, high-volume coating applications, powder coating is more advantageous. Its “high coverage” ensures even protection on complex-shaped substrates, making it ideal for construction, appliances, and automotive parts. Under temperature fluctuations ranging from -20°C to 80°C, powder coatings exhibit excellent “weather resistance,” protecting against environmental factors. Additionally, powder coating’s “cost-effectiveness” and “zero VOC emission” make it the go-to choice for mid-to-low-end markets.
Selection Advice
- High-precision, high-performance needs: Choose PVD coating for high-end manufacturing and decorative products.
- Large-scale, high-volume production: Opt for powder coating for construction, appliances, and automotive parts.
- Limited budget: Powder coating is more cost-effective for mid-to-low-end markets.
- High environmental standards: Both coatings are eco-friendly, but PVD coating has an edge in high-end applications.
Application Scenario Comparison
Application | PVD Coating | Powder Coating |
---|---|---|
High-end manufacturing | Cutting tools, precision molds, medical devices | Not suitable |
Construction & appliances | Not suitable | Structural components, appliance exteriors |
Automotive parts | High-precision components | Large-scale coating parts |
Decorative products | High-end decorative items | Mid-to-low-end decorative items |