Sputtering for Different Materials: Metals, Alloys, Compounds
Sputtering technology handles metals, alloys, and compounds efficiently, making it a go-to for semiconductor, optical, and decorative coatings. You’ve got to tweak parameters based on material properties to ensure top-notch thin film quality.
Overview of Sputtering Tech
A. What’s Sputtering All About
Sputtering is a key part of physical vapor deposition, or what people call PVD coating. Basically, you take high-energy ions and smash them into a target material. This knocks atoms off the surface, and those atoms land on whatever you’re coating, creating a thin film. It all goes down in a vacuum environment, with plasma, usually argon ions, doing the hard work. When ions hit the target, atoms fly off like tiny bullets and stick to the surface you’re working on.
At its heart, sputtering is about energy transfer. Ions hit the target, giving atoms enough push to break free. For example, magnetron sputtering for thin film deposition uses magnets to make the process faster, so the coating comes out even and smooth. This method is huge in semiconductors, where a sputtering machine puts down copper coated layers on chips with pinpoint accuracy.
Sure, sputtering sounds complicated, and it needs high-tech gear like vacuum technology and a good pvd coating machine. That can be a pain. But the upside is you get super reliable thin film coatings, whether you’re running experiments or making products. If you’re in the coating game, sputtering is something you want to understand.
B. Why Sputtering Works for All Kinds of Materials
So why choose sputtering over stuff like metal plating or thermal evaporation? It’s all about flexibility and getting the job done right.
Sputtering shines with high-melting-point materials. Take metals like tungsten or molybdenum, which don’t even flinch at 3,000°C. Thermal evaporation can’t make them vaporize; they just sit there. But with sputter deposition, you don’t need heat. Ions knock atoms loose, so it’s perfect for things like titanium nitride coating on tools or airplane parts that need to stay tough under heat.
Another big win is how sputtering keeps material mixes consistent. If you’re using alloys, like stainless steel or titanium blends, the ratios have to stay exact. An electroplating machine might mess things up, with elements sticking at different rates. But the sputtering process copies the target’s makeup to the pvd coated film almost perfectly. That’s why pvd coating stainless steel is so popular for jewelry and watches. It’s tough, resists scratches, and looks great.
Sputtering’s range is another reason it’s a go-to. It works with metals like gold, silver, and copper, alloys like stainless steel, and compounds like oxides or nitrides. In electronics, it lays down conductive layers. In optics, sputtering gold for reflective surfaces adds anti-glare coatings to lenses. For jewelry, gold pvd coating makes pieces shiny and long-lasting. Thermal evaporation struggles with high-melt materials, and metal plating doesn’t play well with non-conductive surfaces. Sputtering just handles everything.
Here’s a real example: If you’ve ever used a field-emission scanning electron microscope, you know samples need to conduct electricity to show clear images. Coating equipment can put a thin layer of gold coating or platinum on in just minutes. It’s fast, reliable, and labs depend on it.
How Sputtering Works for Different Materials
A. Metals
Sputtering metals is usually pretty straightforward. Materials like copper, gold, and aluminum have high yields and are easy to control. What’s yield? It’s how many atoms get knocked off the target when ions hit it. Data shows gold can hit a sputtering rate of 40 nanometers per minute, while chromium lags behind at about 10 nanometers per minute. So, when you’re using a sputtering machine on gold, things move a lot faster.
What does this mean for real-world use? Metal coatings are in high demand. Gold is a go-to for optical reflective layers, like in telescope lenses or fancy display screens, and it works great. Aluminum shines as a conductive thin film, often used in electronics for circuit layers, pairing perfectly with copper coated surfaces. PVD coating nails this, giving you metal layers that stick well and spread evenly.
The catch? Surface contamination can mess things up. If the target isn’t clean, your thin film might end up with junk in it. Lucky for us, vacuum technology handles this no problem. Keep the setup clean, and metal sputtering deposition gets the job done smoothly.
B. Alloys
Alloys are where things get trickier. The big challenge with alloy sputtering is uneven composition. Different elements have different yields. Take stainless steel, with its mix of iron, chromium, and nickel. Chromium might pop off easier than iron, so the thin film’s makeup doesn’t match the target. This shows up a lot in pvd coating stainless steel, and nobody wants a coating on jewelry or tools that falls short.
There are two ways to tackle this:
- Uniform alloy targets: Make the target with the exact mix upfront, so sputtering keeps things consistent.
- Co-sputtering for alloy thin films: Like confocal sputtering, where you use multiple targets to deposit different elements at once, dialing in the ratios just right.
This approach is common in magnetron sputtering and helps alloy thin films match what you’re aiming for. If you’re making pvd coating for corrosion resistance, say a titanium alloy layer for car parts, multi-target co-sputtering keeps performance solid. Sure, the coating equipment costs more, but for quality, it’s worth the price. Nobody wants a coating that flakes off after a few days, right?
C. Compounds
Sputtering compounds is a whole different ballgame. Materials like titanium dioxide (TiO₂) or silicon dioxide (SiO₂) don’t work with plain sputtering because they need specific chemical makeups. That’s where reactive sputtering comes in. You bring in a reactive gas, like oxygen (O₂) or nitrogen (N₂), during the sputtering process. The target atoms mix with the gas to form the compound you want.
In practice, this is how titanium nitride coating gets made. A titanium target gets sputtered in a nitrogen environment, creating a hard, wear-resistant thin film perfect for cutting tools or medical implants. Reactive sputtering for optical coatings, like anti-glare layers on lenses, uses oxide deposition for clear, durable results.
The trick is controlling the gas mix. More oxygen makes oxides thicker; the right nitrogen balance gives tougher nitrides. Your coating machinery has to be precise, or the thin film might turn out soft or off-color. Reactive sputtering is trickier than standard sputtering, and you’ll need to tweak settings a lot. But once you nail it, you can make top-notch thin films, especially for optics or decorative stuff like that shiny gold pvd coating look.
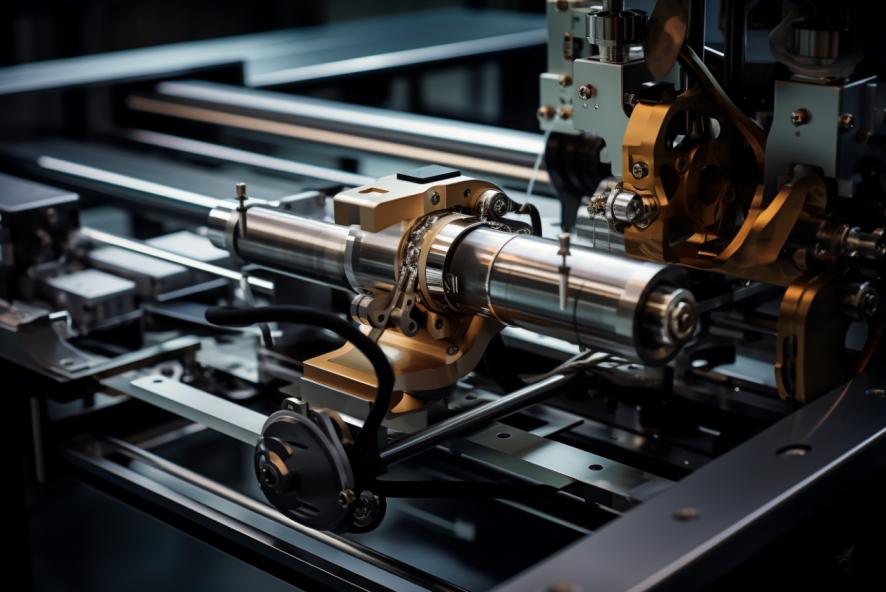
Material Properties & Sputtering Settings
A. What Affects Sputtering Yield
Sputtering yield is all about efficiency. It’s how many atoms get knocked off a target surface per ion hit. Three big factors come into play:
- Atomic bonding energy: Stronger bonds mean atoms are harder to dislodge. Gold has weak bonds, so its yield is high. Chromium’s bonds are tougher, so its yield is lower.
- Ion energy: Higher energy means harder hits, freeing more atoms. But crank it too high, and the target might overheat.
- Ion mass: Heavier ions, like argon, pack a bigger punch, boosting efficiency.
What does this mean for real work? For metals, gold’s high sputtering yield makes deposition fast, perfect for laying down conductive layers or gold pvd coating, like reflective films on optical lenses. Chromium’s yield is slower, about a quarter of gold’s pace, so sputtering yield optimization techniques take longer to dial in. Want to speed things up? Bump up ion energy or tweak the sputtering machine’s power. Just watch out, because too much energy can overheat the target and mess up the thin film quality.
Alloys get more complicated. Elements have different bonding energies, so weaker-bonded atoms pop off easier. In titanium alloys, titanium might sputter faster than other elements, so you need vacuum technology to keep the environment tight for even sputtering deposition. Gold’s great for quick jobs, but low-yield materials like chromium need careful tuning. PVD coating equipment usually has the flexibility to balance speed and quality if you dial it in right.
B. Preferential Sputtering Issues
Preferential sputtering is a headache for alloys and compounds. What’s that? Some elements get sputtered away faster than others, changing the target surface and thin film composition. For example, in a silver-gold-copper mix, copper jets out fast, gold lags behind, and the surface ends up gold-heavy. You see this in pvd coating stainless steel too, where iron and chromium yields don’t match, so the thin film might not hit the mark.
Compounds have similar problems. When sputtering titanium dioxide, if oxygen isn’t controlled, titanium might outpace oxygen, leaving a thin film that’s not hard enough. This is critical for titanium nitride coating, where hardness and wear resistance depend on stable composition. If preferential sputtering kicks in, the coating could lose corrosion resistance or look off-color.
Fixes include two approaches:
- Tweak ion energy: Lower energy can slow down the fast runners, evening things out.
- Use magnetron sputtering: Magnets make ion hits more uniform, stabilizing thin film quality.
If you’re working on alloy barrier layers, like titanium-tungsten coatings, or optical coatings, these tricks make results more reliable. The key is keeping coating machinery dialed in to catch parameter slips.
Key Data Table:
Material Type | Sputtering Yield Traits | Typical Uses | Challenges |
---|---|---|---|
Metal | High yield, easy to manage | Conductive layers (e.g., gold, copper) | Surface contamination |
Alloy | Varying yields, needs balance | Barrier layers (e.g., titanium-tungsten) | Uneven composition, preferential sputtering |
Compound | Needs reactive sputtering, complex | Optical coatings (e.g., TiO₂) | Gas control, maintaining composition |
Real-World Uses and Examples
A. Semiconductors
Sputtering for semiconductor manufacturing really shines in this industry. This technology gets used a lot for making metal interconnects and barrier layers in integrated circuits. Tungsten often gets sputtered into contact holes to keep current flowing smoothly, while titanium alloys work as diffusion barriers to stop materials from mixing. These steps need super pure targets, like tungsten or titanium, and PVD coating nails it every time.
Why does this matter? Chips keep getting smaller, and performance demands keep climbing. Take AMD processors, for example. Their copper interconnect layers come from sputtering. Copper coated films conduct electricity well and let you control thickness precisely, all thanks to the stability of a sputtering machine and vacuum technology. Target purity has to be top-notch, or impurities can wreck the circuit. Good thing modern coating equipment handles this easily, making sure every thin film hits the mark.
B. Optical Coatings
Vacuum sputtering for precision optics is a big deal in this field. Want clearer lenses or displays? Reflective and anti-reflective coatings are the way to go. Silver gets used for reflective layers, like on high-end telescope mirrors, while silicon dioxide (SiO₂) makes anti-reflective layers that let light pass through better. Sputtering deposition keeps these coatings even and tough.
There’s also a technique called GLAD sputtering for building tiny structures in optical devices. Some precision instruments need thin films with specific angles and thicknesses. Anti-reflective coatings on smartphone screens often come from sputtered oxides, making them scratch-resistant and clear. You’ve got to tweak parameters just right, or the coating might mess with light. Lucky for us, magnetron sputtering’s tight control handles these challenges no problem.
C. Other Industries
Sputtering goes way beyond electronics and optics:
- Jewelry making: A sputtering machine for jewelry coatings delivers gold pvd coating that gives pieces a shiny look and scratch-proof quality, way tougher than old-school gold plating.
- Auto parts: Chromium coatings boost wear resistance, making engine components last longer.
- Biomedical: Sputtering titanium alloys for biomedical implants, like artificial joints, adds a titanium nitride coating to improve hardness and make them body-friendly.
- Mass spectrometry: Sputtering helps scientists analyze surface composition, super handy for research.
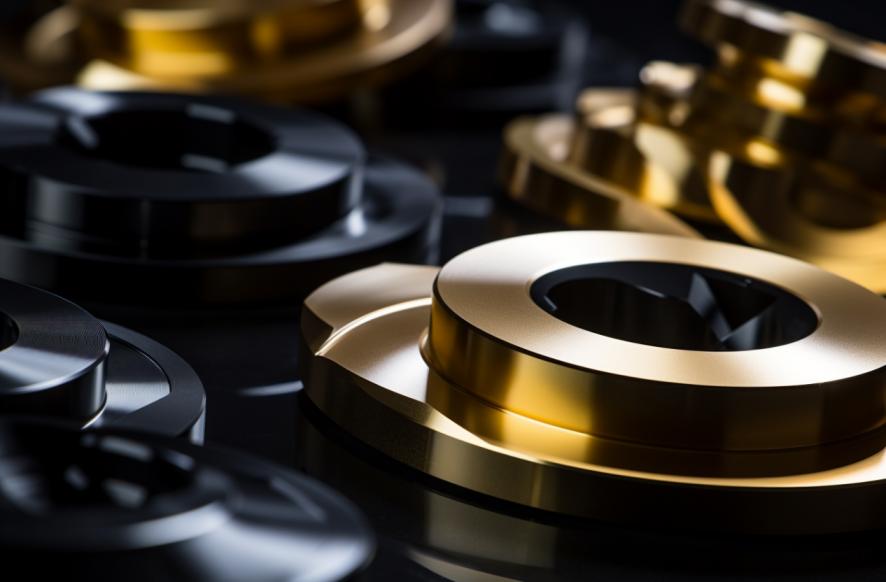
Best Practices & Tips for Sputtering
A. Picking the Right Target
Different thin films need different targets. Here’s a quick guide:
- Pure metal targets: Great for simple conductive layers, like copper coated films, since they deposit fast and easy.
- Uniform alloy targets: Use these for pvd coating stainless steel to keep the composition consistent.
- Composite targets: Perfect for compounds like titanium nitride coating, making reactive sputtering more stable.
The target has to match the substrate, or you might get chemical reactions that ruin the thin film. In practice, check the substrate’s properties, like conductivity or heat resistance, then pair it with the right PVD coating plan. This makes sputtering deposition smoother and the final product more reliable. Targets aren’t cheap, but choosing wisely cuts down on do-overs, saving money in the long run.
B. Tuning Parameters
Good settings make sputtering results shine. Three big ones to watch:
- Power: Higher power boosts sputtering yield, but it can overheat the target.
- Pressure: Low pressure sharpens ion hits, but too low hurts efficiency.
- Gas mix: Adding oxygen or nitrogen for reactive sputtering helps compounds form just right.
Sputtering different materials calls for different tricks. Insulating materials, like oxides, work well with RF sputtering, which handles non-conductive targets easily. Metals or alloys do better with magnetron sputtering, letting you drop pressure while speeding up deposition, ideal for tasks like gold pvd coating that need to move fast. Generally, start with a vacuum below 10⁻³ mbar, add argon, then adjust power to control yield. Tuning takes patience. Run a few tests, log the results, and you’ll find the sputtering machine’s sweet spot quick.
C. Monitoring & Maintenance
Sputtering isn’t a set-it-and-forget-it deal. Keeping an eye on things and staying on top of upkeep is crucial. Here’s what to do:
- Monitoring: Use an ellipsometer to check thickness and XRD to analyze composition, so you know what’s happening in real time.
- Cleaning: Wipe down target surfaces regularly to stop junk from building up. Vacuum technology is a lifesaver here, cutting down on stray air particles sneaking in.
- Maintenance: Check targets for wear monthly. Pits or discoloration mean it’s time to swap them out. Worn targets tank the coating equipment’s efficiency and can wreck a whole batch.