Vacuum Coating: The Key to Black PVD Beauty
- Creating a sleek, stunning black PVD finish
- Giving metal a deep, rich black look
- Why black PVD coatings are tough and wear-resistant
- Customizing black PVD styles for variety
- The eco-friendly, efficient PVD process
Creating a Sleek, Stunning Black PVD Finish
Why a Dust-Free Environment Matters
Just as the screen needs to be thoroughly cleaned before applying the film to the phone, the vacuum coating needs to be done in a nearly dust-free environment. This process is usually carried out in a clean workshop with an ISO 5 level of cleanliness, because even a tiny particle of dust falling on the surface can cause defects in the coating, such as tiny pit spots. This will not only affect the appearance and texture of the product, but may also reduce its durability.
During vacuum coating, the equipment sucks out all the air from the chamber, creating a near-vacuum. This environment is not only clean, but also allows the subsequent PVD technology to maximize its effectiveness. After the air is removed, metal particles are free to deposit on the target surface without being disturbed by impurities. In this way, Educorpus the black PVD coating adheres firmly to the substrate, which is smooth and durable. This step is the cornerstone of the entire process and provides a solid guarantee for subsequent steps.
Spray Paint vs. PVD: What’s the Difference
Many people may ask: why not just spray a layer of black paint, instead of using such a complex process as vacuum coating? The answer is simple: the difference between paint and PVD technology is like a paper car and a steel car, one is just a beautiful surface, and the other is strong and durable.
Painting is simple and fast, and can be done by simply spraying the pigment on the surface of the object. However, the disadvantages of this process are also obvious – the coating is prone to scratching or even peeling. For example, a spray-painted key chain may be bright when it is first made, but after a period of use, the surface will be covered with scratches, and even reveal the underlying metal material.By contrast, PVD technology (Physical Vapor Deposition) is a whole different beast.It evaporates the metal into extremely small particles through a vacuum environment, which are then uniformly deposited onto the surface of the object to form a dense black PVD coating. This coating is not only extremely thin, but also extremely hard, and its wear resistance is far more than traditional spray paint, can withstand longer use and wear.
What’s more, the black PVD coating is not simply “covered” on the surface, but fused with the substrate. This process allows it to withstand everyday friction, such as keys colliding in your pocket, and remain shiny even after prolonged use. Simply put, spray painting is “wearing clothes”, while vacuum coating is “muscle training”, and the effect is naturally very different.
The Secret Behind Even Black Phone Frames
Crack open a high-end smartphone, and you’ll notice its black frame looks deep, uniform, and classy no matter the lighting. That’s vacuum coating doing its magic. Picture this: inside a vacuum chamber, metals like titanium get blasted into tiny bits with high energy. Then, gases like nitrogen jump in, reacting to form a dark compound—think titanium nitride (TiN)—that gives you that slick black finish.
Titanium nitride is a go-to for black PVD coatings because you can tweak its color and sheen by playing with the gas mix. More nitrogen? You get a richer, deeper black. Dial it back a bit, and you’ve got a subtle, glossy vibe. This fine-tuning ensures every phone frame matches perfectly. Plus, black PVD cuts down on fingerprint smudges—tests show about an 80% drop—keeping your phone looking fresh and clean all the time.
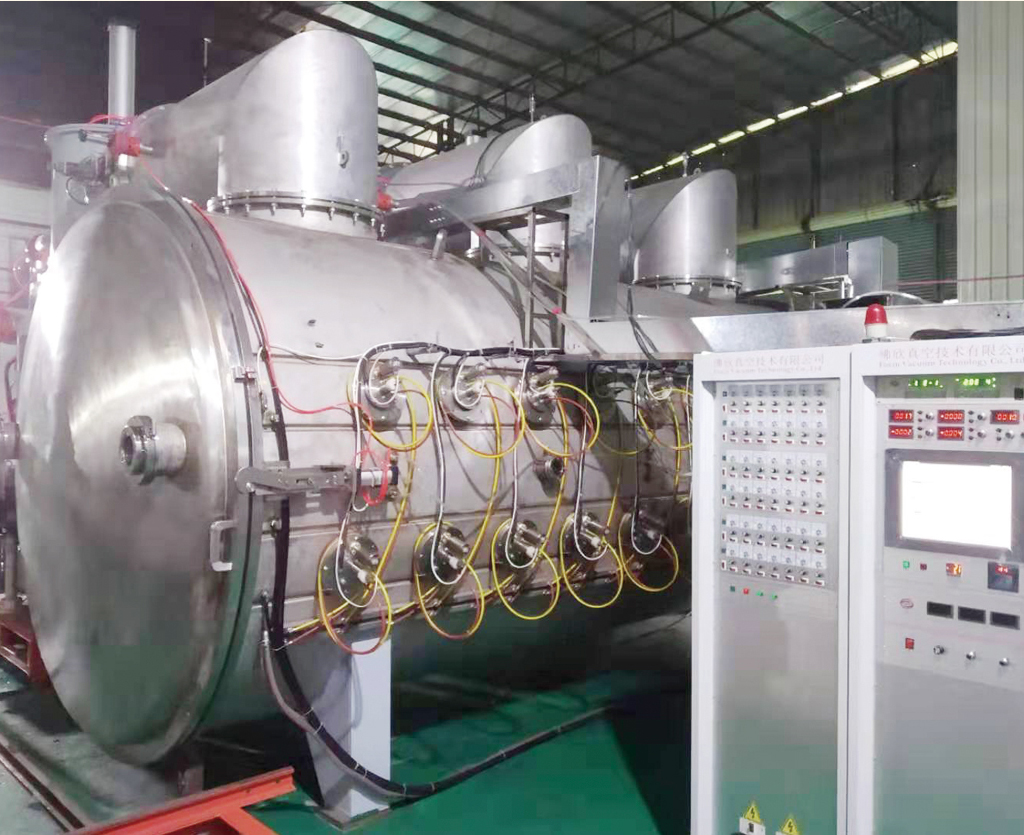
Giving Metal a Deep, Rich Black Look
The Chemistry of Metal and Gas
Vacuum coating sounds high-tech, but it’s pretty straightforward at its core. Toss a chunk of titanium into a vacuum chamber, add a splash of nitrogen, and bam—they react to form titanium nitride (TiN). This stuff naturally rocks a grayish-black tone with a low-key, classy sheen. It’s like growing a new, tougher skin on the metal—only way prettier.
By tweaking the nitrogen flow, you can shift the shade of the black PVD coating. Crank it up for a bold, dark look perfect for understated designs; ease off for a cooler, metallic edge that screams style. This reaction is the heart of PVD—simple, yet it delivers jaw-dropping results. The vacuum keeps everything clean and efficient, so the coating’s always top-notch.
How a Vacuum Makes Black Pop
In regular air, metal particles get messed with by oxygen or other junk, leaving you with uneven colors or weak adhesion. But in a vacuum chamber, the air’s gone. Metal particles can settle in peace, forming a smooth, intense black layer.
This process boosts light absorption to over 92%, cutting reflection to almost nothing. Take a vacuum-coated camera lens ring—it’s so black and matte, it barely glints, looking seriously cool. Compare that to regular spray paint, which might hit 70% absorption and end up looking gray or patchy. The vacuum’s “clean slate” amps up both the color and the durability.
How Different Metals Shape the Vibe
In vacuum coating, picking your metal is like choosing ingredients for a recipe—it changes the black PVD’s feel and performance. Here are three popular choices:
- Titanium (Ti): The crowd favorite. Mix it with nitrogen for titanium nitride, and you get a warm-toned black. Its smooth feel is perfect for phone frames or eyeglass rims, and it’s easy on the wallet.
- Zirconium (Zr): The luxury pick. Pair it with carbon for zirconium carbide (ZrC), and you’ve got a deeper black with insane hardness. It’s a staple for high-end watch cases that last forever.
- Chromium (Cr): The practical one. React it with carbon or nitrogen, and you get solid hardness and wear resistance at a decent price—think tools or kitchen gear.
Each metal brings its own spin. Titanium’s black is soft and approachable, zirconium’s is bold and icy, and chromium’s is tough and reliable. Data shows zirconium coatings outlast titanium by about 50%, though they cost 20-30% more. Your pick depends on the vibe and budget, but they all turn heads with vacuum coating.
Why Black PVD Coatings Are Tough and Wear-Resistant
Thin Coatings That Fight Scratches and Rust
Black PVD coatings are crazy thin—1-3 microns, way finer than a hair—yet they pack serious punch against scratches and rust. That’s thanks to vacuum coating: metal gets vaporized, mixes with nitrogen or carbon, and forms hardcore compounds like titanium nitride or chromium carbide. These are almost as tough as sapphire.
Tests prove it: PVD coatings can handle over 500 rubs in a friction test without a mark, while spray paint might flake after 100. Even better, they’re rust-proof. Soak PVD-treated metal in saltwater, and it’ll hold up for 240 hours without a spot; regular coatings tap out at 48. That “thin but mighty” combo makes black PVD a champ in any situation.
Real-World Durability: Knives to Car Parts
You can see black PVD’s toughness everywhere. Kitchen knives with PVD coatings stay smooth and black after hundreds of cuts, thanks to chromium carbide (CrC) doubling hardness and resisting acidic food juices.
In cars, black PVD shines too. Brake calipers or grille trims coated with it shrug off wear and dirt. After thousands of miles, they still gleam black, lasting at least 50% longer than standard coatings. That durability turns vacuum coating into a game-changer for both style and function.
PVD vs. Regular Coatings: The Breakdown
So, what sets black PVD apart from old-school coatings? Check this out:
- Stickiness: Vacuum coating fuses with the base material, with five times the grip of spray paint—no peeling here.
- Hardness: PVD hits 2000 HV, while spray paint’s lucky to reach double digits. Wear resistance isn’t even a fair fight.
- Heat Resistance: PVD stays black after two days at 150°C; spray paint fades in hours.
- Eco-Friendliness: Traditional electroplating pumps out toxic sludge, but vacuum coating’s clean, slashing carbon emissions by 60%.
These perks make black PVD the go-to for looks and longevity across industries.
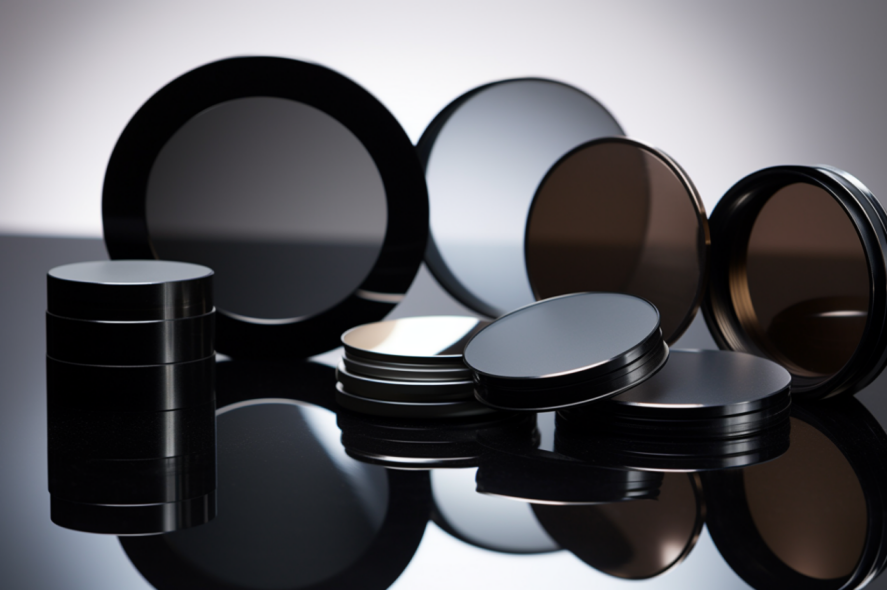
Customizing Black PVD Styles for Variety
Matte or Glossy? You Choose
Vacuum coating’s cool because it lets you switch up the black PVD vibe. Want a chill matte finish or a shiny gloss? It’s all in the process.
- Matte Look: Slow the deposition to create tiny surface bumps, keeping roughness between Ra 0.1-0.4 microns. This scatters light for a soft, non-reflective finish—great for fingerprint-proof parts.
- Glossy Look: Polish the surface post-coating to a slick Ra 0.02 microns or less. Light bounces right off, giving you a mirror-like black shine perfect for blingy decor.
- How to Switch: Tweak the gas (like adding acetylene) and power. Low power roughs it up for matte; high power smooths it out for gloss.
Design Wins: Eyeglass Frames to Car Interiors
Black PVD pops up everywhere. Here’s a couple of examples:
- Eyeglass Frames: Titanium gets a matte black PVD finish—scratch-resistant, fingerprint-proof, and five times more corrosion-resistant than regular coatings. Subtle but sharp.
- Car Interiors: Matte black PVD on dashboard buttons resists wear and smudges; glossy black PVD on trim pieces sparkles under lights, bumping up the luxe feel by 30%.
The Eco-Friendly, Efficient PVD Process
Why a Non-Toxic Process Rocks
Old-school electroplating uses nasty chemicals like hexavalent chromium that trash water supplies and health. Vacuum coating? It’s a green dream. In the chamber, metal vaporizes, reacts with nitrogen, and forms black PVD coatings—no toxic waste, no nasty fumes. It cuts carbon emissions by 62% compared to electroplating.
This clean vibe keeps the planet happy and workers safe—no handling sketchy stuff. Factories save on waste cleanup too. Feels good knowing your gear’s made this way, right?
Fast and Wallet-Friendly
Vacuum coating’s not just green—it’s quick and cheap. Spray painting takes a day with multiple layers, drying, and polishing. PVD? Done in 2-4 hours. Parts go in as plain metal and come out as sleek black stunners.
The savings stack up:
- Less Material: At 1-3 microns thick, it uses 90% of the material efficiently.
- Low Energy: Drops from 10 kWh to 3.5 kWh per square meter—half the cost.
- Recyclable: Strip old coatings and reuse them, cutting waste.
For manufacturers, it’s fast production and bigger profits. For you, it’s high-quality gear at a fair price. Win-win.