What Are the Steps of the PVD Process
- Pre-treatment
- Vacuum Pumping
- Heating and Baking
- Sputtering or Evaporation
- Reaction Gas Introduction
- Deposition and Film Formation
- Cooling and Removal
- Post-treatment
Pre-treatment
In the process of metal coating to resist chemical corrosion, pre-treatment is the crucial first step. This step ensures that the coating adheres firmly, much like cleaning a canvas before painting. Pre-treatment typically includes the following sub-steps:
- Cleaning: Removing oil, oxides, and other impurities, usually through ultrasonic cleaning or chemical cleaning. The concentration of the cleaning solution ranges from 5%-10% to ensure efficient removal of contaminants.
- Sandblasting or Electrochemical Polishing: Increasing surface roughness or smoothness. Sand particles used in sandblasting are typically 0.1-0.5 mm in size, while the current density for electrochemical polishing ranges from 10-30 A/dm². These treatments enhance coating adhesion and eliminate micro-defects.
- Passivation: Using acidic or alkaline solutions (like nitric acid or sodium hydroxide) to form a dense oxide film on the metal surface, further improving corrosion resistance. The pH of the passivation solution usually ranges between 2-4 or 10-12, depending on the metal type.
- Drying: Drying at 60-80°C for 10-20 minutes to remove residual moisture and solvents, ensuring smooth progress of subsequent processes.
To ensure the effectiveness of pre-treatment, surface tension tests or contact angle measurements are often conducted to evaluate surface cleanliness and wettability. Surface tension typically ranges from 30-50 mN/m, and the contact angle should be controlled between 10°-30°.
Vacuum Pumping
In the process of metal coating to resist chemical corrosion, vacuum pumping is a critical step to ensure the purity of the coating process. This is usually done in a vacuum chamber, where a combination of mechanical pumps and diffusion pumps reduces the pressure to a range of 10^-3 to 10^-6 Torr.
Vacuum pumping is carried out in stages:
- Rough Pumping Stage: Using a mechanical pump to reduce pressure from atmospheric pressure to 10^-1 Torr.
- High Vacuum Stage: Further reducing pressure to 10^-6 Torr using a diffusion pump, ensuring almost no residual gas remains in the chamber.
During vacuum pumping, vacuum gauges (like Pirani gauges and ionization gauges) monitor pressure changes in real-time. Pirani gauges measure pressures from 10^-3 to 10^-1 Torr, while ionization gauges measure from 10^-6 to 10^-3 Torr. To enhance vacuum levels, cold traps or adsorption pumps are also used to remove water vapor and organic gases through condensation or adsorption.
The effectiveness of vacuum pumping directly impacts coating quality. If the vacuum level is insufficient, residual gases can form pores or inclusions during the coating process, reducing the coating’s density and corrosion resistance.
Equipment/Technology | Function | Pressure Range (Torr) | Stage |
---|---|---|---|
Mechanical Pump | Rough Pumping | 10^-1 to Atmospheric | Rough Stage |
Diffusion Pump | High Vacuum | 10^-6 to 10^-3 | High Vacuum Stage |
Pirani Gauge | Pressure Monitoring | 10^-3 to 10^-1 | Rough Stage |
Ionization Gauge | Pressure Monitoring | 10^-6 to 10^-3 | High Vacuum Stage |
Cold Trap | Remove Water Vapor | 10^-3 to 10^-6 | Auxiliary Stage |
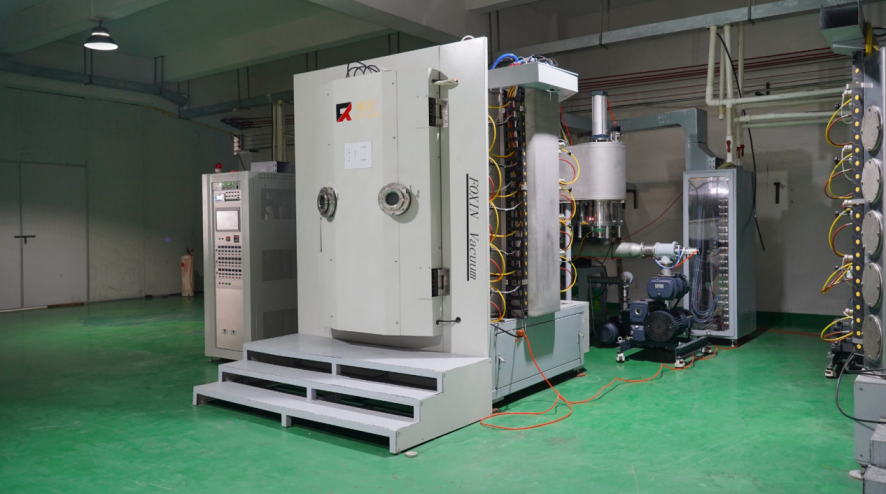
Heating and Baking
In the process of metal coating to resist chemical corrosion, heating and baking are key steps to enhance coating performance. This is typically done in a vacuum chamber, with temperatures controlled between 150-300°C, depending on the metal type and coating material.
During heating, thermal radiation and thermal conduction are the primary heat transfer methods. Heating lamps or resistance wires evenly transfer heat to the metal surface, preventing localized overheating or uneven heating. The heating rate is usually maintained at 5-10°C/min to avoid stress or deformation caused by rapid temperature increases.
Baking removes surface impurities and activates active sites on the metal surface, enhancing the bonding strength between the coating and the substrate. Baking time is typically 30-60 minutes, adjusted based on metal thickness and coating process requirements.
To ensure the effectiveness of heating and baking, thermocouples or infrared thermometers are used to monitor temperature changes in real-time. Chamber pressure is usually maintained between 10^-3 to 10^-5 Torr to avoid oxidation or other gas interference.
Parameter | Function | Range/Condition | Monitoring Equipment |
---|---|---|---|
Temperature | Remove Impurities, Activate Surface | 150-300°C | Thermocouple |
Heating Rate | Avoid Stress and Deformation | 5-10°C/min | Infrared Thermometer |
Baking Time | Ensure Thorough Treatment | 30-60 minutes | Timer |
Chamber Pressure | Avoid Oxidation and Gas Interference | 10^-3 to 10^-5 Torr | Vacuum Gauge |
Metal Thickness | Affect Baking Time | 0.5-5 mm | Thickness Gauge |
Sputtering or Evaporation
In the process of metal coating to resist chemical corrosion, sputtering and evaporation are two core coating deposition techniques. They precisely “paint” the target material onto the metal surface, forming a uniform and dense protective film.
Sputtering uses high-energy ions (usually argon ions) to bombard the target material, causing target atoms to be “knocked off” and deposited onto the workpiece surface. The advantage of sputtering is precise control over coating thickness, typically ranging from 0.1-10 microns, and it’s suitable for various materials. Sputtering power usually ranges from 100-500 W, with working pressure maintained between 10^-2 to 10^-3 Torr.
Evaporation heats the target material until it evaporates into vapor, which then condenses into a film on the workpiece surface. The advantage of evaporation is fast deposition rates, making it suitable for large-area coatings, but it typically requires higher evaporation temperatures for the material. Evaporation rates are usually controlled between 1-10 nm/s, with vacuum levels maintained between 10^-5 to 10^-6 Torr.
To ensure coating quality, plasma monitoring or quartz crystal microbalances are used to monitor deposition rates and coating thickness in real-time.
Technology | Principle | Parameter Range | Application Scenario |
---|---|---|---|
Sputtering | Ion Bombardment | Power: 100-500 W | High Precision, Multi-Material |
Pressure: 10^-2 to 10^-3 Torr | |||
Evaporation | Heating Target Material | Temperature: 1000-2000°C | Large Area, Fast Deposition |
Vacuum Level: 10^-5 to 10^-6 Torr | |||
Deposition Rate | Control Coating Thickness | Sputtering: 0.1-10 nm/s | Real-Time Monitoring |
Evaporation: 1-10 nm/s | |||
Monitoring Equipment | Ensure Process Precision | Plasma Monitoring, Quartz Crystal Microbalance | Quality Control |
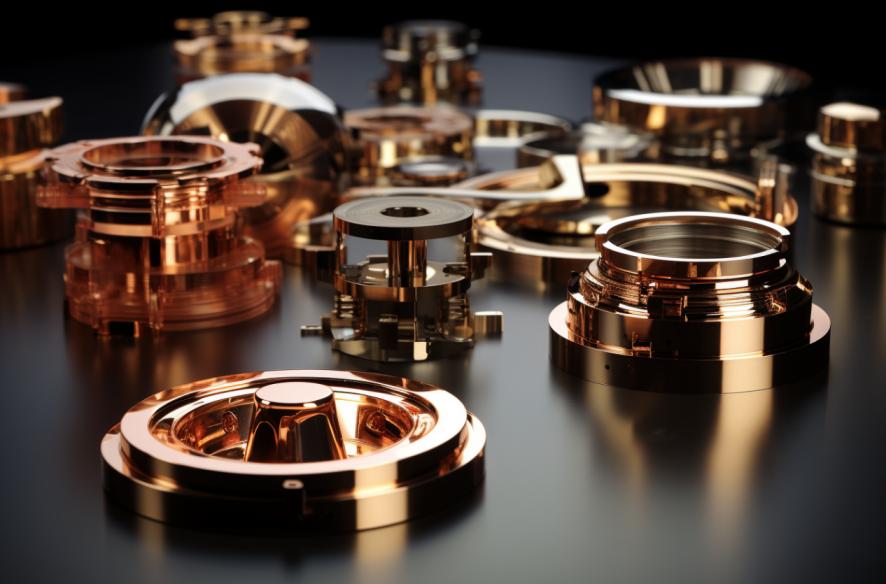
Reaction Gas Introduction
In the process of metal coating to resist chemical corrosion, introducing reaction gases is a key step to enhance coating performance. This step is usually carried out during sputtering or evaporation, where precise control of gas type and flow rate optimizes the coating’s chemical composition and structure.
Common reaction gases include nitrogen, oxygen, methane, and acetylene. These gases react with target atoms during deposition, forming compounds like nitrides, oxides, or carbides. For example, introducing nitrogen can generate titanium nitride (TiN), significantly improving coating hardness and wear resistance. Reaction gas flow rates are typically controlled between 10-100 sccm (standard cubic centimeters per minute), depending on the target material and coating requirements.
The effectiveness of reaction gas introduction is closely related to plasma density and reaction activity. During sputtering, plasma energy typically ranges from 50-500 eV, effectively exciting reactions between gas molecules and target atoms.
To ensure uniform distribution and efficient use of reaction gases, mass flow controllers (MFCs) and gas distributors are often used. Reaction gas pressure is usually maintained between 10^-2 to 10^-3 Torr to ensure reaction efficiency.
Parameter | Function | Range/Condition | Monitoring Equipment |
---|---|---|---|
Gas Type | Form Compound Coating | Nitrogen, Oxygen, Methane, etc. | Mass Flow Controller |
Gas Flow Rate | Control Reaction Degree | 10-100 sccm | Gas Distributor |
Plasma Energy | Excite Reaction | 50-500 eV | Plasma Monitoring |
Gas Pressure | Ensure Reaction Efficiency | 10^-2 to 10^-3 Torr | Vacuum Gauge |
Target Material | Determine Reaction Product | Metal, Ceramic, etc. | Composition Analyzer |
Deposition and Film Formation
In the process of metal coating to resist chemical corrosion, deposition and film formation are the core steps that directly determine coating performance and quality. This step is usually carried out in a vacuum environment to ensure the coating is pure and uniform.
Deposition is primarily done through Physical Vapor Deposition (PVD) and Chemical Vapor Deposition (CVD). PVD deposits target material onto the workpiece surface through physical processes (like sputtering or evaporation), while CVD generates coatings through chemical reactions. At room temperature, PVD deposition rates are typically 0.1-10 nm/s, while CVD rates range from 1-100 nm/s.
Coating thickness is a key parameter affecting performance. Typically, coating thickness is controlled between 0.1-10 microns, adjusted based on application requirements. To ensure thickness consistency, quartz crystal microbalances or ellipsometers are often used for real-time monitoring.
During deposition, substrate temperature and bias voltage are two critical process parameters. Substrate temperature is usually controlled between 100-500°C to optimize coating crystallinity and adhesion. Bias voltage, applied as a negative voltage (ranging from 50-500 V), attracts ions to enhance coating density and bonding strength.
To ensure coating quality, post-treatment after deposition is also crucial. For example, annealing (at 200-600°C) can eliminate internal stresses in the coating, improving its stability and corrosion resistance.
Parameter | Function | Range/Condition | Monitoring Equipment |
---|---|---|---|
Deposition Method | Determine Coating Formation Mechanism | PVD, CVD | Process Control System |
Deposition Rate | Control Coating Thickness | PVD: 0.1-10 nm/s | Quartz Crystal Microbalance |
CVD: 1-100 nm/s | |||
Coating Thickness | Affect Performance | 0.1-10 microns | Ellipsometer |
Substrate Temperature | Optimize Crystallinity and Adhesion | 100-500°C | Thermocouple |
Bias Voltage | Enhance Density | 50-500 V | Voltage Controller |
Post-treatment | Improve Stability | Annealing: 200-600°C | Temperature Control System |
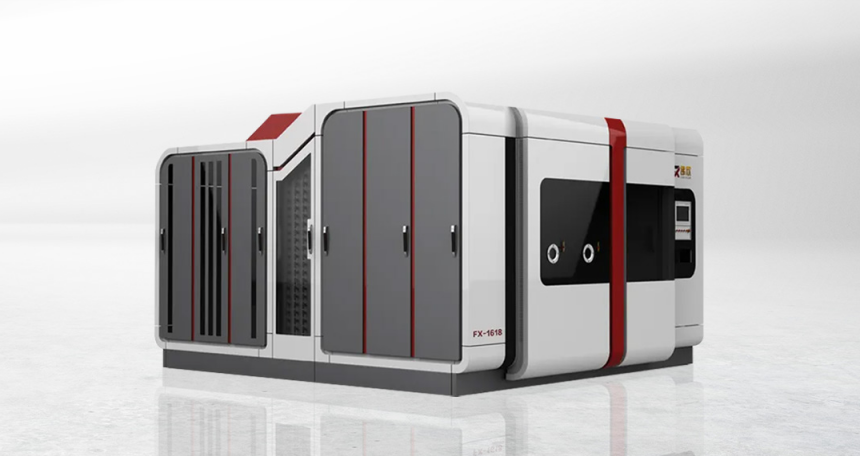
Cooling and Removal
In the process of metal coating to resist chemical corrosion, cooling and removal are the final steps but are crucial for ensuring coating stability. This step is usually carried out in a vacuum chamber to prevent the coating from oxidizing or undergoing other chemical reactions when exposed to air at high temperatures.
Cooling rate is a key parameter affecting coating quality. Typically, cooling rates are controlled between 1-10°C/min, depending on the coating material and substrate characteristics. At room temperature, cooling time is usually 30-60 minutes to ensure uniform cooling.
To optimize cooling, inert gases (like nitrogen or argon) are often used for assisted cooling. Inert gas flow rates are typically controlled between 10-50 L/min, with chamber pressure maintained between 10^-2 to 10^-3 Torr.
After cooling, the removal of workpieces also requires careful handling. Typically, removal is done through stepwise pressure reduction, gradually restoring chamber pressure to atmospheric levels to minimize stress impact on the coating.
To ensure safety during cooling and removal, temperature sensors and pressure monitors are used to monitor process parameters in real-time.
Parameter | Function | Range/Condition | Monitoring Equipment |
---|---|---|---|
Cooling Rate | Avoid Thermal Stress and Grain Coarsening | 1-10°C/min | Temperature Sensor |
Cooling Time | Ensure Uniform Cooling | 30-60 minutes | Timer |
Inert Gas | Accelerate Cooling, Avoid Oxidation | Nitrogen, Argon | Mass Flow Controller |
Gas Flow Rate | Control Cooling Efficiency | 10-50 L/min | Pressure Monitor |
Chamber Pressure | Minimize Stress Impact | 10^-2 to 10^-3 Torr | Vacuum Gauge |
Stepwise Pressure Reduction | Avoid Mechanical Shock | Gradually Restore Atmospheric Pressure | Pressure Controller |
Post-treatment
In the process of metal coating to resist chemical corrosion, post-treatment is the final step to enhance coating performance and stability. This step is usually carried out after coating deposition, aiming to eliminate internal defects and improve functionality.
Annealing is one of the most common post-treatment processes. By heating the coated workpiece to 200-600°C and maintaining it for a certain time (usually 30-120 minutes), residual stresses within the coating can be effectively eliminated, improving its crystallinity and adhesion. During annealing, inert gases (like nitrogen or argon) are often used for protection to prevent oxidation or contamination of the coating.
To further improve surface quality, polishing is also essential. Through mechanical or chemical polishing, tiny protrusions or defects on the coating surface can be removed, making it smoother and more uniform. Post-polishing surface roughness is usually controlled between 0.01-0.1 microns, depending on application requirements.
In some special applications, passivation is also an important part of post-treatment. Using acidic or alkaline solutions (like nitric acid or sodium hydroxide), a dense oxide film is formed on the coating surface, further enhancing its corrosion resistance. The pH of passivation solutions usually ranges between 2-4 or 10-12, depending on the coating material.
To ensure post-treatment effectiveness, surface inspection or performance testing is often conducted. For example, scanning electron microscopy (SEM) is used to observe the coating’s microstructure, or salt spray testing is performed to evaluate its corrosion resistance.
Process | Function | Parameter Range/Condition | Application Scenario |
---|---|---|---|
Annealing | Eliminate Residual Stresses | Temperature: 200-600°C | Improve Crystallinity |
Time: 30-120 minutes | |||
Polishing | Improve Surface Quality | Roughness: 0.01-0.1 microns | Enhance Appearance and Performance |
Passivation | Enhance Corrosion Resistance | pH: 2-4 or 10-12 | Special Application Scenarios |
Surface Inspection | Verify Coating Quality | SEM, Salt Spray Testing | Quality Control |
Inert Gas | Protect Coating from Oxidation | Nitrogen, Argon | Annealing and Passivation Processes |