
News
12 Year Pvd Coating Machine In Foxin
What Can Be PVD Coated
• Metal Materials
• Ceramics and Glass
• Plastics and Polymers
• Semiconductors and Electronic Materials
• Composite Materials
• Biomedical and Medical Materials
Metal Materials
Metals are some of the most common substrates for PVD coating, and almost all common metals can benefit from this technology to enhance their surface properties. For example, stainless steel is widely used in kitchenware and medical devices due to its corrosion resistance and strength. After PVD coating, its hardness can increase from around 500HV to over 2000HV (based on Vickers hardness tests at room temperature), significantly improving its scratch resistance. Another example is titanium alloy, which is favored in the aerospace industry for its lightweight and high strength. PVD coating can further boost its oxidation resistance, extending its lifespan. The watch case or knife you’re holding might already be using this technology.
The beauty of PVD lies in its flexibility. By adjusting vacuum levels and deposition parameters, coating thickness is typically controlled between 1-5 microns, with hardness ranging from 2000HV to 4000HV, depending on the substrate and process conditions. Plus, the color options are endless—from classic gold and rose gold to modern black or blue—meeting both decorative and functional needs. However, not all metals are equally suitable for PVD. Here’s a comparison of some common metals:
Metal Material | Suitability | Hardness Increase (HV) | Corrosion Resistance Increase (hours) | Recommended Coating | Typical Applications |
---|---|---|---|---|---|
Stainless Steel | High | 1500-2000 | 1000-1500 | TiN, CrN | Cutlery, faucets, door handles, watch cases |
Titanium Alloy | High | 2000-2500 | 1500-2000 | CrN, DLC | Eyeglass frames, medical devices, aerospace |
Aluminum Alloy | Medium | 800-1200 | 500-800 | Al₂O₃, DLC | Automotive parts, smartphone cases |
Tool Steel | High | 2500-3000 | 1000-1500 | TiAlN | Cutting tools, molds |
Copper & Alloys | Medium | 500-800 | 300-500 | ZrN, TiN | Electronic components, decor |
• Stainless steel and titanium alloys are star materials for PVD due to their excellent hardness and corrosion resistance.
• Beyond traditional uses, PVD is also making waves in the renewable energy sector, such as surface treatments for battery current collectors.
Ceramics and Glass
Ceramics and glass are indispensable in many fields due to their unique physical and chemical properties. However, they sometimes need enhanced wear resistance or decorative effects, and that’s where PVD coating comes in.
In aerospace or precision instruments, ceramic components often endure high mechanical stress or harsh environments. Using PVD techniques like magnetron sputtering, a 1-3 micron coating can be deposited on ceramic surfaces, increasing hardness from 1300-1700HV to 2000-2500HV (room temperature tests) while improving lubrication and reducing friction. For instance, silicon nitride ceramic bearing balls see a 40%-60% boost in wear resistance after coating. Glass is more common in everyday life—architectural glass treated with PVD not only gains a metallic sheen but also becomes heat-insulating and UV-resistant. The anti-fingerprint coating on your smartphone screen? That’s often PVD technology at work.
Ceramics focus more on wear resistance and high-temperature stability, while glass is often used for optical or decorative purposes, requiring slightly different process parameters. Here’s a detailed comparison:
Material Type | Original Hardness (HV) | Coated Hardness (HV) | Common Coating | Typical Applications |
---|---|---|---|---|
Alumina Ceramic (Al₂O₃) | 1300-1500 | 2000-2200 | TiN, DLC | Cutting tools, medical implants |
Silicon Nitride (Si₃N₄) | 1500-1700 | 2300-2500 | TiN, DLC | Bearing balls, turbine blades |
Soda-Lime Glass | 500-600 | 1000-1200 | Al₂O₃, Si₃N₄ | Decorative glass, phone screens, windows |
Borosilicate Glass | 600-700 | 1200-1300 | Al₂O₃, Si₃N₄ | Heat-resistant cups, labware |
Glass coatings are typically 0.5-2 microns thick, sufficient for most needs. As the table shows, PVD applications for ceramics and glass vary—material selection should be adjusted based on specific scenarios.
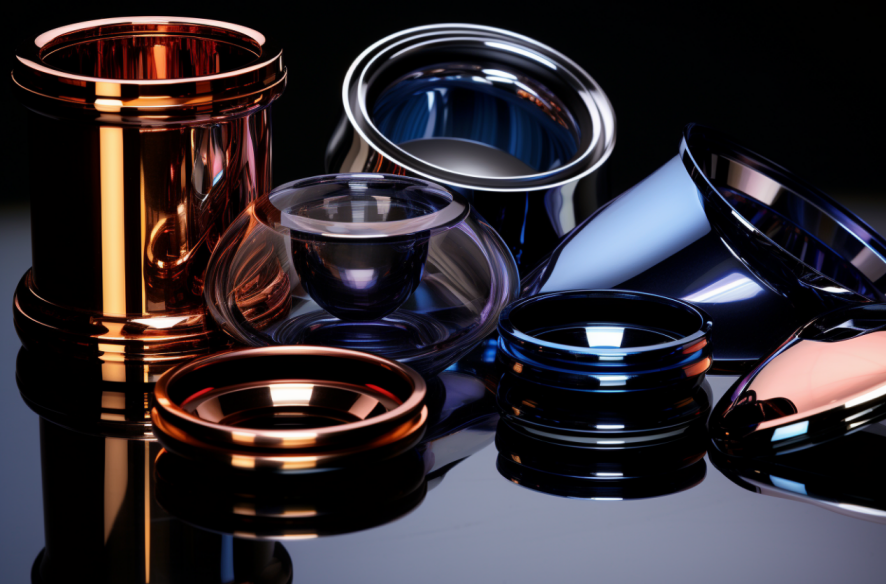
Plastics and Polymers
Plastics are widely used for their lightweight, easy processing, and low cost, but their surface properties often fall short of high-end requirements. PVD coating offers a solution for plastics, enhancing wear and corrosion resistance while adding aesthetic appeal—like that sleek, durable coating on your phone case.
However, plastics have lower heat resistance, so PVD processes require special handling. Common pre-treatments include plasma cleaning (for PEEK, 80°C-120°C), chemical etching (ABS with 30%-40% chromic acid), or primer coating (PC, 5-10 microns thick). These steps ensure proper coating adhesion. Here’s a comparison of some plastics:
Material Type | Heat Resistance (°C) | Surface Treatment Difficulty | Coating Adhesion | Typical Applications |
---|---|---|---|---|
PEEK | 250-300 | Medium | High | Aerospace, medical equipment |
ABS | 80-100 | High | Medium | Appliance casings, car interiors |
PC | 120-140 | Low | Medium-High | Phone cases, eyeglass lenses |
• PEEK performs best due to its high heat resistance and strong adhesion, while ABS is slightly trickier to treat.
• From fashion accessories to car interiors, PVD expands the applications of plastics.
Semiconductors and Electronic Materials
Semiconductors and electronic materials are a key stage for PVD processes. Common semiconductors like silicon (Si), silicon carbide (SiC), and gallium nitride (GaN) are used in integrated circuits and power devices, while electronic materials like copper (Cu), aluminum (Al), and gold (Au) are found in circuit boards and sensors.
In lithography, PVD coatings can reduce light scattering, improving resolution; in packaging, they prevent moisture ingress, extending device lifespan. Here’s a comparison:
Material Type | Original Conductivity (S/m) | Coated Conductivity (S/m) | Temperature Range (°C) | Main Applications |
---|---|---|---|---|
Silicon (Si) | 1-100 | 100-500 | 200-400 | Integrated circuits, sensors, solar panels |
Silicon Carbide (SiC) | 100-500 | 500-1000 | 600-1000 | Power electronics, high-temperature environments |
Gallium Nitride (GaN) | 500-1000 | 1000-2000 | 800-1200 | RF devices, optoelectronic devices |
Copper (Cu) | 5.8×10⁷ | 5.8×10⁷ | 200-400 | Circuit boards, connectors |
• SiC and GaN excel in high-temperature environments, while gold and copper shine in conductivity.
• PVD deposition temperatures are typically controlled between 200-500°C to preserve material integrity.
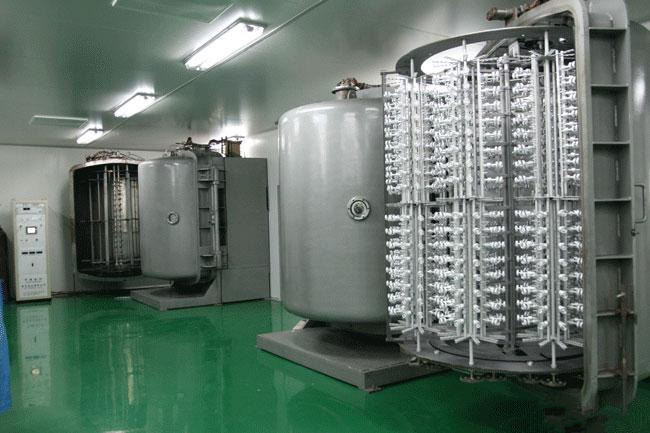
Composite Materials
Composite materials like carbon fiber-reinforced polymer (CFRP), glass fiber-reinforced polymer (GFRP), and metal matrix composites (MMC) are widely used for their high strength and lightweight properties. PVD coatings can further enhance their performance.
Take CFRP, for example—commonly used in aerospace, it gains improved hardness and wear resistance through PVD coatings (1-3 microns thick, adhesion 40-50N). GFRP benefits from corrosion protection in construction, while MMC excels in electronic heat sinks due to its high-temperature resistance and thermal conductivity. Here’s a comparison:
Material Type | Mechanical Strength (MPa) | Temperature Range (°C) | Main Applications |
---|---|---|---|
CFRP | 1000-2000 | 200-300 | Aerospace, high-performance cars |
GFRP | 500-1000 | 150-250 | Construction, automotive manufacturing |
MMC | 800-1500 | 300-500 | Electronic heat sinks, mechanical parts |
• CFRP has the highest strength, ideal for high-end applications.
• MMC stands out in temperature resistance.
Biomedical and Medical Materials
In the medical field, PVD coatings are widely used to enhance the performance of instruments and implants. Surgical blades, dental tools, and more can see their hardness increase to 20-30GPa with coatings (1-2 microns thick), significantly improving wear resistance and sharpness while gaining antibacterial properties to reduce infection risks.
For implants like orthopedic devices or cardiovascular stents, PVD coatings provide biocompatibility and corrosion protection. Here’s a comparison of common coatings:
Coating Material | Hardness Range (GPa) | Friction Coefficient | Corrosion Resistance | Main Applications |
---|---|---|---|---|
TiN | 20-30 | 0.4-0.6 | High | Surgical tools, orthopedic implants |
ZrN | 18-25 | 0.3-0.5 | Very High | Cardiovascular stents, dental tools |
DLC | 10-80 | 0.1-0.2 | Medium-High | Joint implants, minimally invasive tools |
• DLC’s low friction makes it ideal for joint implants, while ZrN’s excellent corrosion resistance suits cardiovascular applications.
• PVD deposition temperatures are typically kept below 200°C to protect biomaterials.