What Is DLC Coating (Diamond-Like Carbon): Key Facts to Know
DLC Coating (Diamond-Like Carbon) is a really tough and smooth carbon layer. It fights off wear and rust pretty well. You’ll find it in machines, cars, and regular items around the house. It helps stuff last a lot longer. They make it with PVD and CVD methods. The sp3 bonds give it strength, and sp2 bonds keep it slick. It’s useful and has a nice look too.
What Is DLC Coating
Definition
DLC Coating, full name “Diamond-Like Coating,” is a thin film coating made from carbon. It puts a super thin protective layer on surfaces and boosts durability a ton. DLC Coating works on all kinds of materials, like metal parts, plastic shells, or even glass. It covers more ground than titanium nitride coating does. Just a few microns thick, this layer stops daily wear and keeps stuff going strong.
They make DLC Coating with vacuum technology. The PVD coating process puts carbon atoms onto the material. Unlike metal plating, which needs heavy layers, DLC Coating gets the job done efficiently. Take a car part as an example: coat it with DLC Coating, and it cuts down on repair hassles. It’s big in cars, medical gear, and consumer products. Coating equipment is easy to run. It controls the layer thickness just right, fitting needs like tougher surfaces or better looks. That makes it super useful.
Core Characteristics
DLC Coating shines with two big traits: super high hardness and low friction. It’s not as hard as natural diamond, which hits 10 on the Mohs scale, but it beats most PVD coating for toughness. It fights off scratches well. Picture an iron hammer’s striking face with DLC Coating: the surface holds up better and feels reliable in your hands. Hardness is just the start, though. It also cuts friction down.
Low friction means the DLC Coating surface slides with almost no drag, reducing wear and sticking. Think of a curtain track: apply DLC Coating, and it glides so smooth you barely notice, way more practical than gold PVD coating. This mix of hardness and slickness keeps DLC Coating steady in spots needing durability and ease. PVD coating process controls carbon atom placement exactly, making sure it performs solid.
How Does DLC Coating Work
The Mix of sp2 and sp3 Bonds
The performance of DLC Coating comes from two types of carbon bonds: sp2 and sp3. The sp3 bond gives hardness. It’s tight and strong, kind of like diamond, able to handle wear. For example, a medical probe with DLC Coating can take constant use and lasts longer than metal plating. The sp2 bond makes the surface smooth, similar to graphite, cutting down friction.
This mix lets DLC Coating balance hardness and slipperiness. Take a sewing machine needle as an example: with DLC Coating, it slides through thread easier, way better than titanium nitride coating, which only offers hardness. Sputtering technology uses vacuum technology to deposit carbon atoms. Engineers can tweak the sp2 and sp3 ratio to fit specific needs. That’s where the flexibility of the PVD coating process shines.
Why Call It “Diamond-Like”
DLC Coating gets its name from a “family tie” to diamond. It’s not a crystal structure like diamond but an amorphous carbon. Still, it keeps some of diamond’s key strengths. Imagine a factory gear: equip it with DLC Coating, and its wear resistance jumps up, yet it costs much less than real diamond. Practicality beats flashy looks here.
Unlike diamond, DLC Coating also brings low friction to the table. The sputtering process arranges carbon atoms just right, protecting the surface while reducing drag. Picture a door hinge coated with DLC: it turns quietly and holds up well, outdoing gold PVD coating in function. Coating equipment makes this “diamond-like” trait easy to achieve, and the value speaks for itself.
Main Advantages of DLC Coating
Durability
DLC Coating has durability as its biggest strength. In daily life, stuff gets scratched or rusty after a while. Keys lose their shine, scissors get dull. DLC Coating fights these issues hard. Its hardness beats PVD coating. Take a fishing rod’s metal part as an example. With DLC Coating on it, seawater doesn’t eat it up. The surface stays smooth and clean.
It also holds up against chemical corrosion. Works great in wet or acidic places. The carbon layer, made by vacuum technology, is thin but tough. It takes on heavy friction no problem. Say a garden shovel gets DLC Coating. Mud and scraping won’t hurt it. Compared to titanium nitride coating, DLC Coating does better at resisting wear and rust. Coating equipment keeps it stuck on strong and long-lasting.
Versatility
DLC Coating isn’t just durable. It’s got a lot of uses too. Low friction is a big deal. Picture a curtain track with DLC Coating. You pull it, and there’s almost no resistance. Beats regular PVD coating for sure. This smoothness really helps parts that move a lot. Boosts efficiency and cuts down wear.
Plus, it’s got a deep black shine that looks good. Think of a metal picture frame with DLC Coating added. It resists scratches and looks high-end. Better than gold PVD coating. PVD coating process lets you tweak its traits. Want it slick or fancy? DLC Coating handles both. Covers all kinds of everyday needs just fine.
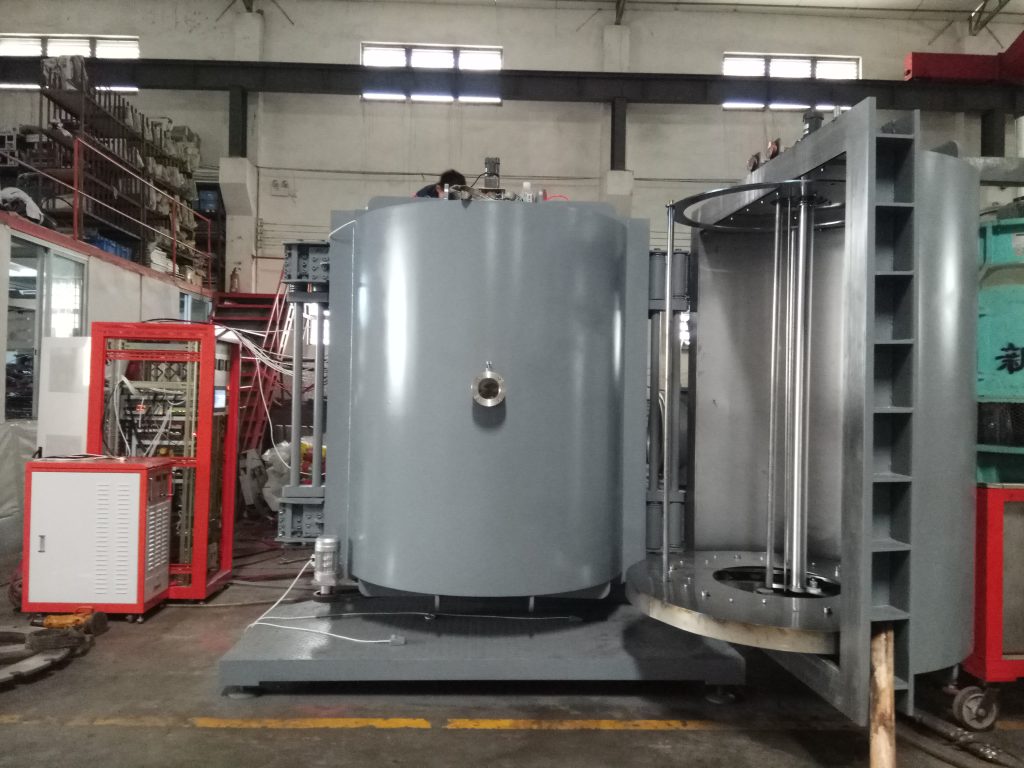
How DLC Coating Gets Made
Common Techniques
DLC Coating production relies mostly on PVD and CVD techniques. PVD coating uses vacuum technology to sputter carbon atoms onto a surface. It forms a thin, tough protective layer. Take a steel bolt, for instance. Add DLC Coating with PVD, and its durability goes up fast. Sputtering is the key step in PVD. High-energy particles deposit the carbon material, making the coating even and cleaner than metal plating.
CVD works differently. It uses gas reactions to create DLC Coating. Carbon-rich gas breaks down at high heat, and carbon atoms stick to the surface. This fits well for complex shapes. Say you have a pipe joint. CVD applies DLC Coating to cover every edge, boosting hardness. Costs more, sure, but the results stand out. Coating equipment handles both methods, tweaking DLC Coating performance based on what you need.
New Trends
Modern tech makes DLC Coating better. Magnetron sputtering uses a magnetic field to pack the carbon layer tighter. Picture a toothbrush with metal parts. Coat it with DLC Coating this way, and it gets harder and won’t peel off easy. PVD and CVD mixed processes boost wear resistance, outdoing titanium nitride coating. Think of a dental tool. With hybrid DLC Coating, it cuts smoother and fights bacteria too.
Eco-friendliness is improving. Vacuum technology cuts down waste, skipping the chemical mess of gold PVD coating. PVD coating process gets streamlined, so DLC Coating production saves energy. It works for big-scale use now, blending practicality with sustainability.
Applications of DLC Coating
Industrial Uses
DLC extends the life of parts in industry. For example, a drill bit with DLC stays sharp when cutting hard metal. It cuts down on the hassle of frequent replacements. The PVD coating process uses sputtering to make the carbon layer stick tight. This gives it better wear resistance than titanium nitride coating, especially under heavy loads.
Car engines often use DLC too. When pistons get DLC on their surface, friction drops. That boosts power output and cuts fuel use. Parts made of PVD coated stainless steel with DLC can handle oil stains and high heat. Coating equipment brings this tech to production lines, making everything more reliable.
Everyday Scenarios
DLC works great in daily life too. Take dental drills: with DLC, they’re hard and don’t stick to debris. This makes them easier to use, and vacuum technology keeps the coating clean. High-end camera lens frames made of PVD coated stainless steel plus DLC resist scratches and look sharp. They beat gold PVD coating in durability. Laptop hinges with DLC move smoothly and wear less, improving how they feel to use.
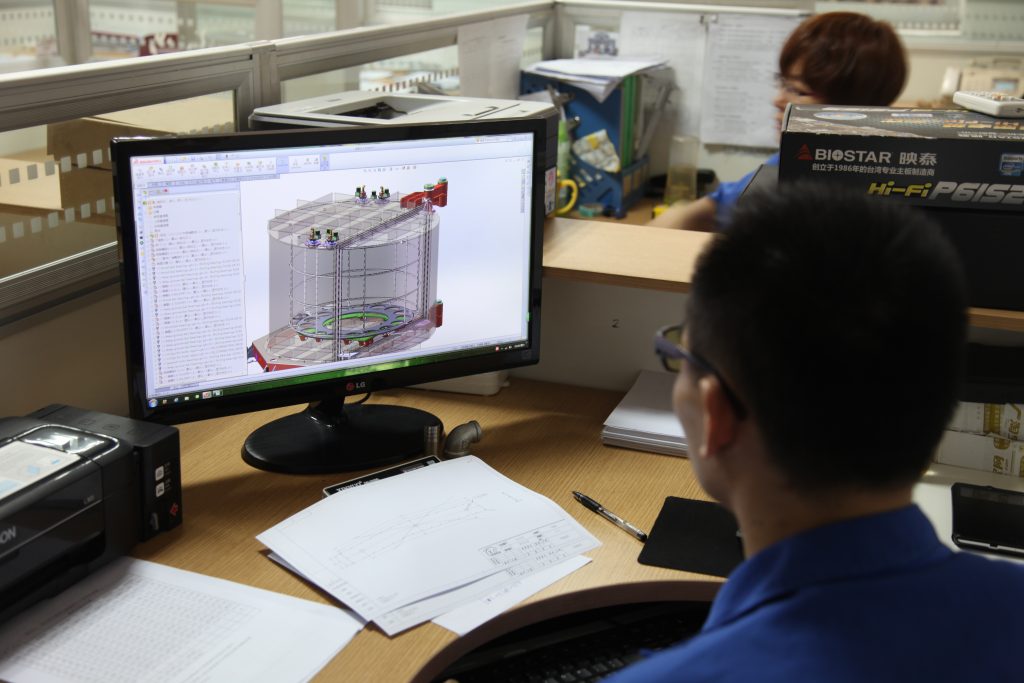
When Should You Pick DLC Coating
DLC Coating is a solid choice, but it’s not something you need every time. Figuring out when to go with it or stick to another coating can save you some headaches. Whether it’s industrial gear or stuff you use daily, picking the right coating is what solves problems.
High Wear & Low Friction Needs
- When Mechanical Parts Wear Out Fast: In factories, bearings and gears spin all day, and wear hits hard. Regular PVD coating might hold up for a bit before needing a swap, but DLC Coating has higher hardness. It keeps those parts running for years without breaking. Take a bearing with DLC Coating: it resists wear and cuts down on repair downtime, beating out titanium nitride coating in practicality.
- When Sliding Gets Sticky: Big friction makes things tough to move, sometimes even jamming them up. DLC Coating uses the sputtering process to create a smooth surface, letting parts slide easy. Picture a bike chain coated with DLC Coating; pedaling feels lighter, and the ride gets better. Compared to basic metal plating, DLC’s low friction lasts longer, so you don’t worry about it sticking after a while.
- Tough Spots with Heat and Pressure: Some places get hot and heavy, and normal coatings can’t take it. DLC Coating stands strong in those conditions. Think of an engine piston with DLC Coating: less friction, more power, and better fuel use. PVD coating process works fine, but under extreme stress, DLC Coating outlasts PVD coating and keeps equipment from failing.
Special Conditions & Looks
- When Corrosion Is a Problem: Kitchen knives hit water or acidic stuff a lot, and plain metal plating rusts quick. DLC Coating, made with vacuum technology, fights corrosion and stays hard. It cuts smooth and holds up well. Same goes for medical tools like surgical blades; they handle sterilization without damage.
- When You Want Tough and Pretty: Watches and jewelry need to look good and take a beating. PVD coated stainless steel with DLC Coating gives a sleek black shine that doesn’t scratch easy. It’s tougher than gold PVD coating and won’t fade fast.
- Extra Help in Rough Environments: PVD coating machine is simple and covers basic decoration or protection. But if it’s harsh out there, like outdoor gear facing sweat or salt, DLC Coating steps up. A pen nib with DLC Coating writes smooth and doesn’t wear down.
Choosing DLC Coating depends on what’s bugging you. Is wear and friction driving you nuts, or do you need it for tough conditions and style? DLC beats PVD coating in those areas, but PVD is solid too, especially for cost and simple jobs. Coating equipment handles both just fine; the trick is knowing what you need.