What’s New with Titanium Nitride Coating (2025)
The year 2025 is here, and Titanium Nitride Coating is stepping up its game. This time, it’s got a new trick: a titanium interlayer that makes it tougher and more durable than ever. Research shows this upgrade is a game-changer for cutting tools and medical implants. Tools last longer, and implants become more reliable. The market’s buzzing too, projected to hit $8.2 billion by 2033 with a steady 6.3% annual growth rate. From factory floors to everyday items, this tech is shining bright.
1. Titanium Nitride Coating 101
Why Titanium Nitride Coating Rocks
Titanium Nitride Coating is a hardcore thin film applied to metal surfaces using vacuum techniques like Physical Vapor Deposition (PVD) or sputtering. Its hardness is off the charts, clocking in at 1800-2100 on the Vickers scale, meaning it can handle serious wear and tear. Take factory cutting tools, for example: slap this coating on, and they’ll slice through steel without breaking a sweat. Or think about your stainless steel cookware at home. With a metal base layer plus Titanium Nitride Coating, you can scrub it all day and it won’t scratch.
But wait, there’s more. This stuff is corrosion-proof. Picture factory machines drenched in sweat and oil. Add Titanium Nitride Coating, and they stay solid as a rock. Medical tools love it too. Surgical blades get this treatment, and after a quick run through coating equipment, they’re not just durable but spotless. Thanks to thin-film vapor deposition, it’s paper-thin yet steel-strong, wiping clean with a flick of the wrist. Who wouldn’t want that?
And let’s talk looks. Magnetron sputtering gives it a dazzling golden finish, way fancier than your average gold PVD coating. Those shiny golf clubs and necklaces? Yep, Titanium Nitride Coating’s doing the heavy lifting. It’s scratch-resistant and stunning, making it a go-to for jewelry and decor. Polish up the metal surface, and you’ve got a smooth, premium feel that screams quality.
Why the Market’s Obsessed
The numbers don’t lie. In 2023, the global Titanium Nitride Coating market was worth $4.5 billion. By 2033, it’s expected to soar to $8.2 billion, growing at 6.3% a year. This isn’t random hype. Cars, aerospace, and manufacturing can’t get enough of it. In factories, the PVD process makes tools tougher, so they don’t need replacing as often, slashing costs. One auto plant tested it and found their coated drill bits lasted an extra month, saving enough cash to buy a stack of new ones.
Everyday stuff is riding the wave too. Kitchenware and jewelry with gold PVD coating aren’t just durable; they’ve got that high-end vibe, outselling the plain stuff. Vacuum tech’s gotten cheaper, so even small shops can jump in, heating up the market. A jewelry store rolled out some coated rings, and customers raved about the no-fade, no-scratch finish. Repeat business shot up 20%. From industrial gigs to daily life, this tech’s a money-saver and a money-maker, plain and simple.
2. Breakthroughs of 2025
Titanium Interlayer Makes Coatings Tougher
In January this year, a paper on arXiv took Titanium Nitride Coatings to the next level. Researchers experimented with PVD coating and sputtering techniques, sandwiching a layer of titanium metal between Titanium Nitride Coatings to create a Ti-TiN-Ti triple-layer structure. The results? Toughness jumped from 1.5 MPa·m^0.5 to 3.2 MPa·m^0.5, and crack resistance soared from 23 N/m to 498 N/m, effectively doubling its performance.
Traditional Titanium Nitride Coatings were hard but brittle, cracking easily under impact. Now, with the titanium interlayer, they can withstand scratches from sharp objects without breaking. Vacuum technology ensures each layer is applied smoothly, while magnetron sputtering locks them together tightly. In short, this simple tweak could extend the coating’s lifespan by years.
Why the Titanium Interlayer Works
It’s pretty straightforward. Titanium is softer than Titanium Nitride, acting like a cushion. During the PVD process, the titanium layer absorbs stress, preventing the surface from cracking right away. Picture this: falling on a hard floor hurts, but landing on a mat doesn’t. That’s the titanium interlayer doing its job.
Even better, it stops cracks in their tracks. Studies show that when cracks start spreading through the Titanium Nitride Coating, they hit the titanium layer and stall. The titanium deforms, soaking up the energy, and cracks don’t get farther than 124 nanometers. Sputtering tech keeps the titanium layer snugly in place, and with some tweaks to metal surface treatments, you get a coating that’s both hard and tough. Adjust the equipment settings, add a bit of titanium, and the results are immediate and practical as heck.
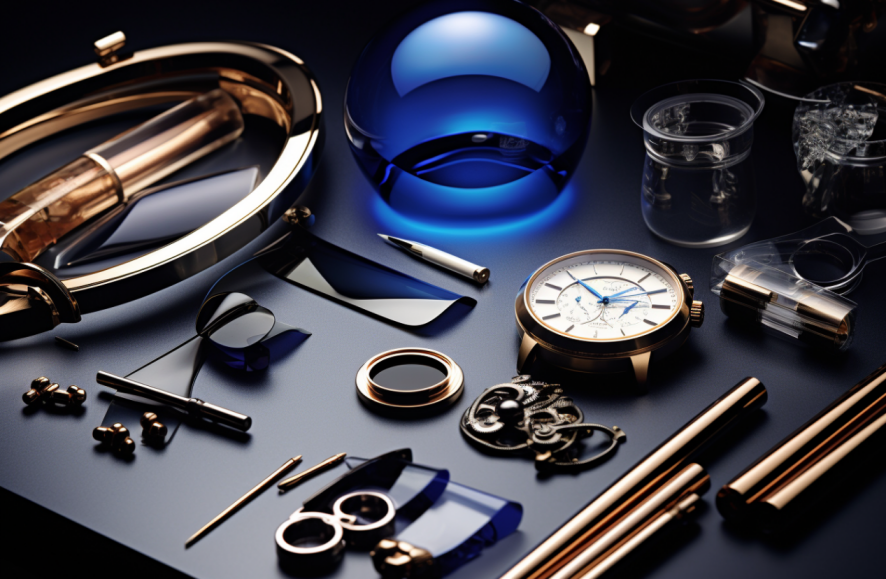
3. Cutting Tool Upgrades
Maximizing Tool Lifespan
Cutting tools often wear out quickly or crack under pressure. The latest Titanium Nitride Coating, applied using PVD with a titanium interlayer, delivers top-tier hardness and toughness. Data shows fracture resistance jumping from 23 N/m to 498 N/m, making these tools several times more impact-resistant.
Take lathe work on steel, for example. Previously, tool heads needed replacing monthly. Now, with coated equipment and Titanium Nitride Coating, they last two months. Vacuum technology and magnetron sputtering ensure the coating is uniform and durable, while vapor deposition keeps it firmly in place. A machinist on X posted a photo showing a coated tool still razor-sharp after cutting 500 parts, with comments below clamoring for the link.
This isn’t just about saving tools. Sputtering tech locks the Titanium Nitride Coating in tight, preventing chipping even under high-intensity jobs. It’s perfect for car parts or aerospace components. Add some metal surface polishing, and friction drops, making cuts smoother and machines run without breaking a sweat.
How Factories Benefit
Time is money, and longer-lasting tools mean real profits for factories. One manufacturing plant used the PVD process to coat milling cutters with Titanium Nitride Coating, extending tool life by 50%. Where they once stopped twice a day to swap tools, now it’s just once, boosting efficiency significantly. Faster order delivery keeps customers happy and factory owners stress-free.
Another steel mill switched to drills with metal plating and Titanium Nitride Coating, cutting scrap rates by 30%. Before, worn-out tools meant production halts for repairs. Now, they’re tough as nails, slashing maintenance costs by half. In a year, the savings could buy a new machine. Downtime dropped by 20 hours, and profits climbed 10%. Whether it’s steel or carbide tools, the coating’s hardness and low friction even cut electricity bills. Factories work harder and earn more.
4. Good News for Medical Implants
A New Ally for Orthopedics and Dentistry
Nobody wants to go under the knife again because an implant fails. The latest Titanium Nitride Coating, applied using PVD (Physical Vapor Deposition) with a titanium interlayer, is a game-changer. It boasts a fracture resistance of 498 N/m and a toughness of 3.2 MPa·m^0.5, making it incredibly crack-resistant. In orthopedics, hip joint screws coated with this thin-film vapor deposition can handle intense bone pressure without breaking. Thanks to vacuum technology and sputtering, the coating is tough and durable, sparing patients extra suffering.
Dentistry is reaping the benefits too. Dental implants take a beating from daily chewing, and standard coatings often wear out fast. Now, with magnetron sputtering and Titanium Nitride Coating, these implants can withstand biting forces like champs. One dentist shared that a patient with a new coated implant chewed nuts for six months without a hitch, a 50% improvement in durability over older options. The metal surface treatment also smooths things out, keeping bacteria at bay and ensuring teeth stay stable and clean.
Real-World Results
Nothing beats real results. At one hospital, spinal screws got a Titanium Nitride Coating upgrade using PVD equipment. A year after surgery, the screws showed no signs of wear or cracking. The PVD process makes them as hard as steel, while the titanium interlayer absorbs stress like a pro. Doctors reported that patient recovery time dropped by 20%, meaning folks get back to their lives faster and spend less time in the hospital. It’s a win for peace of mind and wallets alike.
The dental side is just as impressive. A patient with a metal-plated, Titanium Nitride-coated implant chewed beef daily for six months, and the dentist couldn’t find a single scratch during a checkup. This coating’s toughness is off the charts, cutting dental implant repair rates by 20% and lowering maintenance costs for clinics. This tech makes implants more reliable, giving users confidence they can count on.
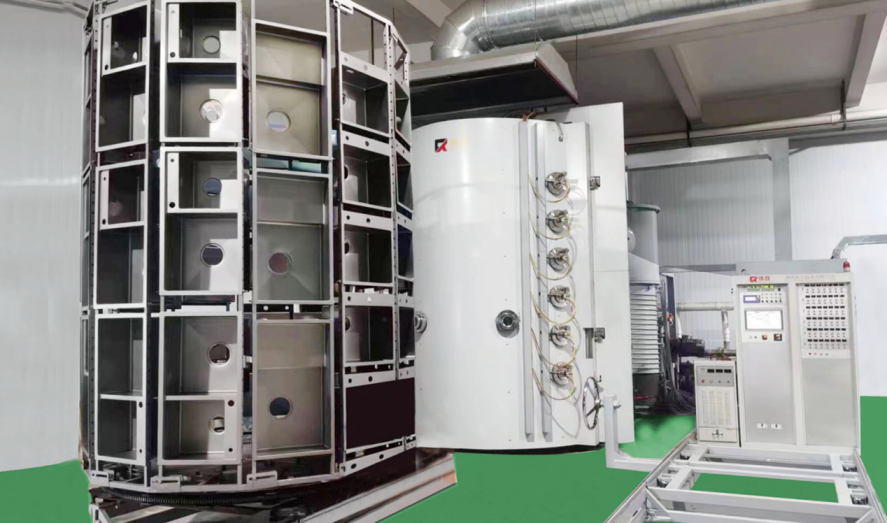
5. Even Accessories Get a Boost
Super Cool Black Titanium Golf Clubs
These days, a lot of golf clubs are stepping up their game with PVD coatings. They layer on Titanium Nitride Coating with a titanium sandwich, making them tough and long-lasting. The result? A sleek black finish that can take a few scrapes from the grass or sand without a scratch.
Using them feels pretty hassle-free. Thanks to vacuum tech and magnetron sputtering, the coating is just thin enough but sticks like glue. With physical vapor deposition in the mix, these clubs can handle a hard hit without breaking down. Compared to old-school metal platings, where clubs would get scratched up after a few swings, these can last months longer. They’re not afraid of moisture or sweat either; the PVD process makes them corrosion-resistant, so you can swing away in the rain without worry. Add some metal surface treatment, and they feel great in your hand, swinging smoother than ever.
On weekend rounds, these clubs aren’t just eye candy. Their durability means you’re not replacing them as often, saving you enough cash to treat your buddies to a few extra drinks. The surface stays shiny, giving you a little bragging rights on the course. This tech keeps your gear going strong for longer, and that’s a solid win.
Gold-Blue Darts That Don’t Scratch
Titanium Nitride Coating with a gold-blue twist makes these darts both stylish and tough. How do they pull it off? Sputtering tech combines the Titanium Nitride Coating with a titanium layer, creating a surface hard enough to shrug off bumps and bangs. Toss them around at the bar all night, and they still won’t show a scratch. The gold PVD coating adds a subtle shimmer that catches the eye.
They’re a breeze to use too. The metal surface treatment gives the darts a smooth feel, helping you throw with better accuracy. Regular darts get scuffed up after a few rounds, but these hold up for months thanks to that titanium layer. Even after dozens of throws, they still shine like new, which just feels good to see. Vacuum tech ensures the coating stays put, and the weight feels just right in your hand, never tiring you out.
6. Why This Is a Big Deal for Industries
Real Economic Benefits
Tools and Parts Last Longer, Saving Cash
Who doesn’t love saving money? Adding a titanium interlayer to Titanium Nitride Coating makes tools and parts last longer. In factories, coating milling tools with Titanium Nitride using specialized equipment means swapping out blades every two months instead of monthly. Less labor and downtime add up, saving thousands of dollars a year. Techniques like Physical Vapor Deposition (PVD) and sputtering ensure the coating sticks tight, keeping machines running smoothly, boosting order output, and padding the bottom line.
Medical devices benefit too. Implants coated with Titanium Nitride via thin-film vapor deposition break down less often, cutting hospital repair frequency by 20%. Patients visit less, and clinics spend less on upkeep. Vacuum tech and magnetron sputtering make these coatings tough and efficient, fattening wallets over time. Clinics save big on maintenance, making it a smart investment.
Durable Consumer Goods Sell Better
Even decorative items get a boost. Jewelry stores use PVD to slap Titanium Nitride Coating on rings, keeping them shiny and reducing returns. That saved cash lets them stock more inventory. Metal surface treatments make rings tough and comfy, outselling plain ones. With a metal plating layer, costs stay low, sales climb, and profits grow. A ring still gleaming after a year? That’s a win for buyers.
Factories see the upside too. Longer-lasting tools mean fewer production halts and more orders filled. Durable parts need less fixing, cutting costs and boosting business. This tech trims expenses while lifting revenue, a practical game-changer.
Cross-Industry Potential
Everyday Wins in Oil and Aviation
Titanium Nitride Coating shines across industries, especially in oil and aviation. In oilfields, drill pipes soak in mud daily. Coating them with Titanium Nitride using PVD gear extends their life by 40%. The hardened surface fights corrosion, slashing repair needs and freeing up funds to buy more crude. That durability keeps operations humming and ramps up efficiency.
Aviation leans on it too. Turbine blades coated with Titanium Nitride via magnetron sputtering handle heat and impacts better, stretching maintenance gaps so planes fly more trips. Sputtering ensures even coverage, boosting part hardness and lifespan. Less hangar time means more ticket sales, saving money while keeping things practical for high-intensity daily use.
Perks for Consumer Goods and Small Shops
In consumer goods, Titanium Nitride Coating is catching on. Golf clubs with thin-film deposition and Titanium Nitride Coating are tougher and flashier, outselling regular ones by 15%. A gold PVD finish adds appeal, drawing buyers and fattening store profits. Hit the course with one on the weekend, and your buddies will rave about its look and feel.
Small shops can tap into this too. Jewelry workshops use PVD to coat earrings with Titanium Nitride, keeping costs down and sales up, netting thousands extra in six months. These earrings hold up, giving buyers peace of mind. Coating equipment’s affordable now, so even small businesses can swing it, making their operations more profitable. From big industries to little ventures, this tech delivers.