Why Choose PVD Coating for Surface Treatment
After using PVD coating for surface treatment, its hardness can reach 2000-3000 HV, adhesion can reach 40-60 MPa, high temperature resistance exceeds 600°C, friction coefficient is below 0.1, and carbon emissions are reduced by 30%-50% compared to traditional processes. While improving material performance, it also meets environmental protection demands.
Fundamentals of PVD Coating Technology
PVD, or Physical Vapor Deposition, is a surface treatment technology carried out in a vacuum environment, typically with a working temperature range of 200°C to 500°C. To ensure the coating’s adhesion strength with the substrate reaches 40-60 MPa, the process conditions need to be strictly controlled. Using methods such as evaporation, sputtering, or arc ion plating, materials are deposited onto the workpiece surface in atomic or molecular form, forming a thin film just a few microns thick. In sputtering, argon ions strike the target material at speeds of hundreds of meters per second, releasing metal atoms that deposit uniformly on the substrate.
From a scientific perspective, the PVD process excels in controlling the microstructure. By adjusting deposition parameters, such as controlling the vacuum level to 10^-3 Pa, nanometer-sized grains can be achieved, resulting in coatings with hardness up to 2000-3000 HV. Additionally, the friction coefficient of the coating is typically reduced to below 0.1, allowing the workpiece to maintain excellent wear resistance even under extreme conditions. In aerospace, the application of PVD coatings extends the service life of key components, typically by 3-5 times, and significantly reduces maintenance costs.
Since the porosity of PVD coatings is below 1%, they effectively prevent the intrusion of external corrosive media, giving PVD coatings excellent corrosion resistance. Our tests show that stainless steel surfaces treated with PVD can resist over 1000 hours of corrosion in salt spray tests, while untreated samples only last 24 hours. The environmental impact of the PVD process is also minimal, with energy consumption approximately 40% lower than traditional electroplating, fully meeting modern industrial green manufacturing requirements.
Enhanced Material Properties
The advantages of PVD coatings in improving material performance stem from their precise control over microstructure and chemical composition. For hardness, PVD coatings can achieve a microhardness of 2000-3000 HV by depositing compounds such as nitrides, carbides, or oxides. This high hardness is primarily due to the nanocrystalline structure inside the coating, typically with grain sizes of 5-20 nanometers. For example, titanium nitride (TiN) coatings, due to their face-centered cubic crystal structure, exhibit excellent resistance to plastic deformation and good oxidation resistance, remaining stable at temperatures up to 600°C.
Corrosion resistance is another key feature of PVD coatings, and it relies on the coating’s density and chemical inertness. Studies show that the PVD process can control coating porosity to below 1%, reducing the penetration path for corrosive media. For example, after depositing a chromium nitride (CrN) coating on a stainless steel surface, the coating can resist over 1000 hours of corrosion in salt spray tests due to the high chemical stability of CrN. Additionally, the residual compressive stress in the coating (typically 1-3 GPa) further suppresses crack initiation and propagation, enhancing durability.
Optimization of tribological properties relies on the combination of low surface energy and high hardness. PVD coatings typically achieve a friction coefficient of below 0.1 due to their surface smoothness and chemical inertness. For example, diamond-like carbon (DLC) coatings, due to the presence of sp³ hybridized bonds, not only have an extremely low friction coefficient but also perform excellently under dry friction conditions. Experimental data shows that, under high-load conditions, the wear rate of DLC coatings can be as low as 10^-16 m³/N·m, far better than traditional hard alloys.
PVD processes can also optimize performance by adjusting deposition parameters. During magnetron sputtering, argon gas pressure is typically controlled between 0.1-1 Pa to ensure moderate ion energy and avoid excessive defects inside the coating. Additionally, adjusting the substrate bias (usually between -50 to -200 V) enhances the coating’s adhesion to the substrate and introduces appropriate compressive stress.
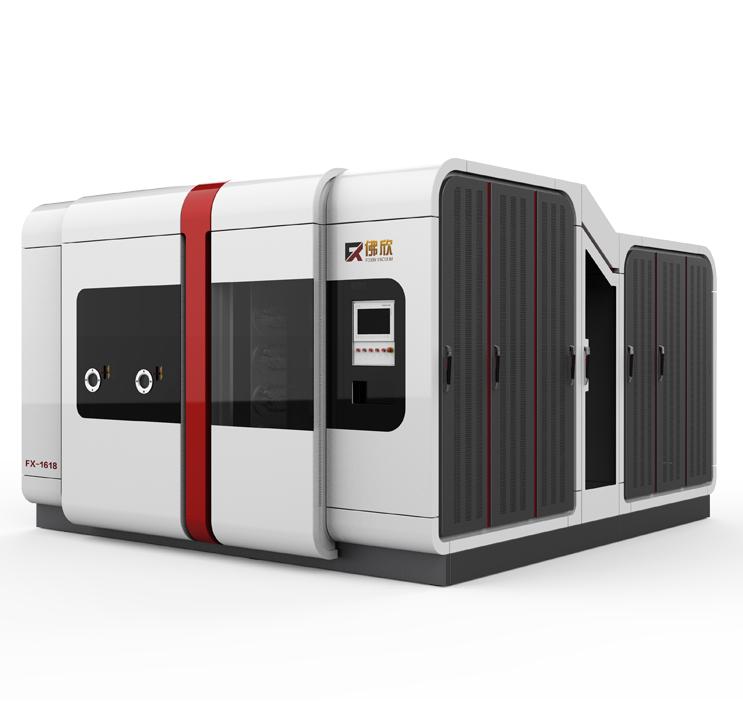
Surface Microstructure and Adhesion Characteristics
The adhesion strength of PVD coatings is crucial to their performance, and it mainly depends on the interfacial bonding mechanisms between the coating and the substrate. This bonding typically involves three forms: mechanical interlocking, chemical bonding, and diffusion. Mechanical interlocking occurs when the substrate surface is treated with sandblasting or etching to form a microscopic rough structure, allowing the coating to embed into it. Chemical bonding occurs when active atoms in the coating (such as Ti or Cr) form covalent or metallic bonds with the oxide or metal atoms on the substrate surface, enhancing adhesion strength.
In the PVD process, the effect of substrate bias on adhesion is particularly significant. Applying a negative bias between -50 to -200 V provides enough energy for deposited ions to strike the substrate surface, promoting the following effects:
- Increased coating density, reducing porosity.
- Enhanced atomic diffusion at the interface, forming metallurgical bonds.
- Introduction of appropriate residual compressive stress, preventing crack propagation.
When depositing a TiN coating on a stainless steel substrate, the chromium oxide layer on the stainless steel reacts with TiN to form a stable transition layer, further enhancing adhesion. This transition layer is typically a few tens of nanometers thick, effectively mitigating the stress concentration caused by differences in thermal expansion coefficients. However, if the substrate surface is contaminated (e.g., with grease or oxides), adhesion strength will significantly decrease, so pre-treatment steps should not be overlooked.
The adhesion strength of PVD coatings is also affected by the deposition temperature. Typically, deposition temperatures of 200°C to 500°C can activate atomic diffusion behavior on the substrate surface, enhancing interfacial bonding strength. However, excessively high temperatures may soften or deform the substrate, so suitable process parameters should be selected based on the specific material.
Thermal and Mechanical Performance
The thermal and mechanical properties of PVD coatings are key to their excellent performance under extreme conditions. From a thermal perspective, PVD coatings typically remain stable in high-temperature environments ranging from 200°C to 600°C. For example, TiN coatings have an oxidation resistance temperature of up to 600°C, while CrN coatings can withstand higher temperatures of over 700°C. This high-temperature stability is primarily due to the coating’s high density and chemical inertness, making it resistant to oxidation or decomposition at elevated temperatures.
In terms of mechanical properties, PVD coatings exhibit extremely high hardness and wear resistance, typically ranging from 2000-3000 HV. This is attributed to the nanocrystalline structure within the coating, with grain sizes generally between 5-20 nanometers, effectively resisting plastic deformation. Additionally, the residual compressive stress in the coating (1-3 GPa) further enhances resistance to crack propagation. The key mechanical advantages of PVD coatings are:
- Low friction coefficient (typically below 0.1), reducing wear.
- High fatigue resistance, extending component life.
- Good impact resistance, suitable for dynamic load environments.
Matching the thermal expansion coefficients is also an important factor affecting PVD coating performance. Differences in thermal expansion between the coating and substrate can lead to interfacial stress concentration, reducing adhesion strength. For instance, the thermal expansion coefficient of TiN is approximately 9×10^-6/°C, while that of steel is 12×10^-6/°C. To alleviate this, PVD processes often introduce multilayer structures, such as alternating Ti/TiN deposition, to reduce the impact of thermal stresses through gradient transition layers.
The thermal and mechanical properties of PVD coatings are also closely related to their deposition parameters. In magnetron sputtering, controlling the argon pressure within the range of 0.1-1 Pa optimizes ion energy, improving the coating’s density and adhesion. Additionally, appropriate substrate bias (between -50 and -200 V) can enhance the uniformity of the coating’s internal stress distribution, preventing delamination caused by excessive localized stress.
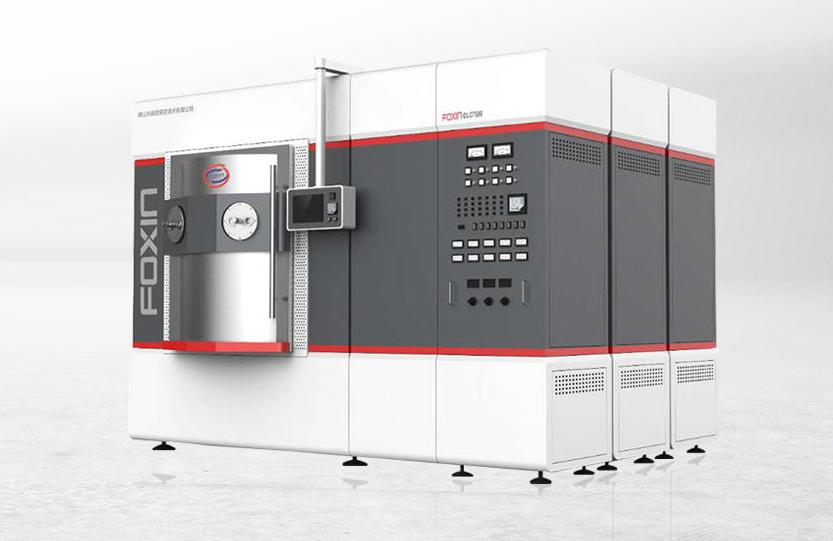
Environmental and Economic Advantages
PVD coatings, as an environmentally friendly surface treatment technology, are green due to their low pollution and high resource utilization. Compared to traditional electroplating, PVD processes do not require harmful chemicals like hexavalent chromium or cyanides, significantly reducing wastewater and exhaust emissions. Furthermore, PVD is conducted in a vacuum environment, achieving a material utilization rate of over 90%, while traditional electroplating typically achieves a metal deposition efficiency of only 50%-60%.
The main environmental advantages of PVD coatings include:
- No harmful chemical waste discharge, reducing water pollution.
- Coating materials are recyclable, reducing resource waste.
- Energy consumption is approximately 40% lower than traditional electroplating, meeting energy-saving and emission-reduction requirements.
The environmental friendliness of the PVD process is also related to its low-temperature operating conditions. With working temperatures ranging from 200°C to 500°C, PVD does not produce high-temperature combustion byproducts, such as carbon monoxide or nitrogen oxides. Additionally, PVD equipment is typically equipped with efficient vacuum pump systems that recycle process gases (e.g., argon), further reducing greenhouse gas emissions. After adopting PVD technology, carbon emissions per square meter of coating can be reduced by 30%-50%.
To visually compare the environmental performance of PVD with other surface treatment technologies, the following data can be referenced:
Technology Type | Energy Consumption (kWh/m²) | Chemical Waste Discharge (L/m²) | Carbon Emission (kg CO₂/m²) |
---|---|---|---|
PVD | 10-20 | 0 | 5-10 |
Electroplating | 30-40 | 5-10 | 15-20 |
Thermal Spraying | 25-35 | 2-5 | 12-18 |