
News
12 Year Pvd Coating Machine In Foxin
Why Pvd Coating can Be Used in Plastic Products?
In recent years, with the continuous development of pvd coating technology, the functions of pvd coating machinery are more comprehensive.
Professionals to the application of coating machine industry is divided into non-metallic and metal two categories. Many people will have doubts about whether plastic products can be coated. Under this circumstances our blog will introduce you in detail pvd technology in the application of plastic product.
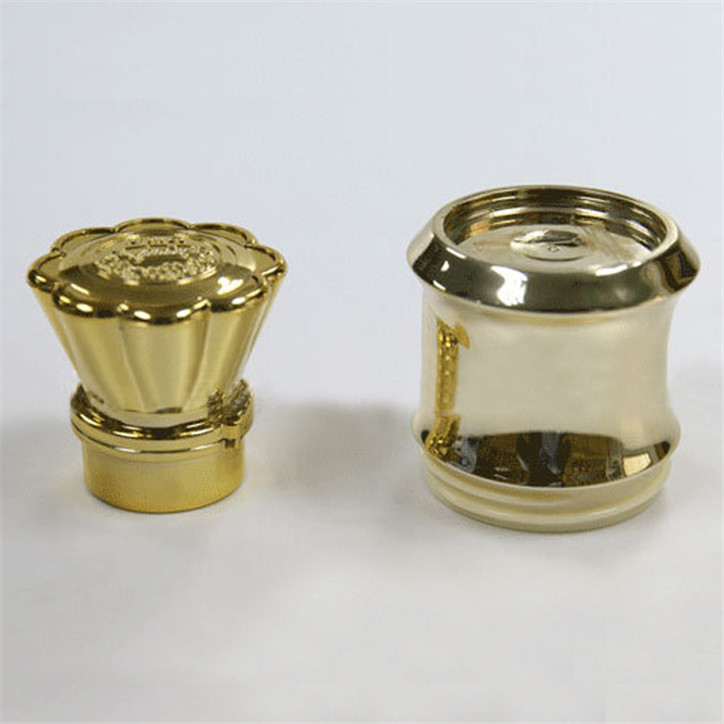
Reasons for PVD Coating application in plastic products
The main question people focus on this phenomenon is the characteristic of plastics are easy to deform at high temperatures. First step to answering this question is to understand how pvd works.
PVD is a kind of technology that transforms solid materials into gaseous state through physical process. Many kinds of plastic materials can be used as the substrate for coating deposition.
PVD technology is widely used in the manufacture of surface coating, to improve the physical and chemical properties. Because of PVD coating has high hardness, good corrosion resistance, excellent aesthetics and the characteristics of low friction.
So for the product durability, beautiful, practical purposes people apply PVD coating technology to plastic products.
Although equipment has been developed to coat plastic products at low temperatures, we still want to carefully select plastic materials that meet the coating properties.
When selecting the plastics suitable for coating, the main consideration is the thermal stability, chemical stability and adhesion with the coating. Here are some common plastic materials that can be used in coating technology:
Choose PVD coated plastic materials
1.Polycarbonate (PC)
Features: polycarbonate is a kind of transparent and high strength plastic,which has good heat stability and impact resistance.
Application: PC plastic is often used in automotive parts, electronic product shells (such as mobile phones, TVS, computer screen protectors), glasses lenses, etc. It can well withstand the treatment of PVD coating and maintain good transparency and durability.
2. Polyamide (PA, Nylon)
Features: Nylon plastic has high mechanical strength and heat resistance, suitable for use under high temperature conditions.
Applications: Polyamides are used in the manufacture of automotive parts, electrical insulation materials and industrial machinery parts, etc. And its particularly suitable for PVD coating to increase their wear and corrosion resistance.
3.Polyteflon (PTFE)
Features: PTFE is a plastic with extremely high chemical stability and high temperature resistance, but its surface energy is extremely low, resulting in difficult coating attachment.
Application: Despite the poor coating adhesion, PTFE can still be PVD coated by special surface pretreatment (such as plasma treatment). It is commonly used in high temperature corrosion resistant applications such as chemical industry equipment and aerospace.
4. Polyvinyl chloride (PVC)
Features: Polyvinyl chloride is a common plastic with good chemical stability and low cost, but its heat resistance is limited.
Application: PVC is suitable for PVD coating in some low temperature environments, which is often used in coating applications of building materials, pipes, automotive interiors, etc.
5. ABS (acrylonitrile-butadiene-styrene)
Features: ABS plastic has good impact toughness, heat resistance and processability. Its surface is easier to handle and can be well combined with the PVD coating.
Application: ABS is widely used in the manufacture of electronic equipment housing, toys, auto parts, etc. PVD coating can give ABS more durability and decorative.
The benefits of PVD coating on plastic products
- Improve wear resistance and hardness
- Plastics are soft and susceptible to scratching and wear, especially during use. If the plastic surface is coated, especially the PVD technology is used to plate hard metal films (such as aluminum, titanium, chromium, etc.), the surface hardness and wear resistance can be significantly improved. In this way, plastic products can be more durable in high-friction environments and avoid affecting the service life due to surface scratches.
- Improves appearance and decoration
- Many plastic products (especially for consumer electronics and home appliances) through the coating process, access to metallic luster or other colour effect. To promote the appearance of the product, meet the needs of high-end market of aesthetic. PVD technology can provide a different metal color have qualitative feeling looks more delicate and make plastic products more beauty.
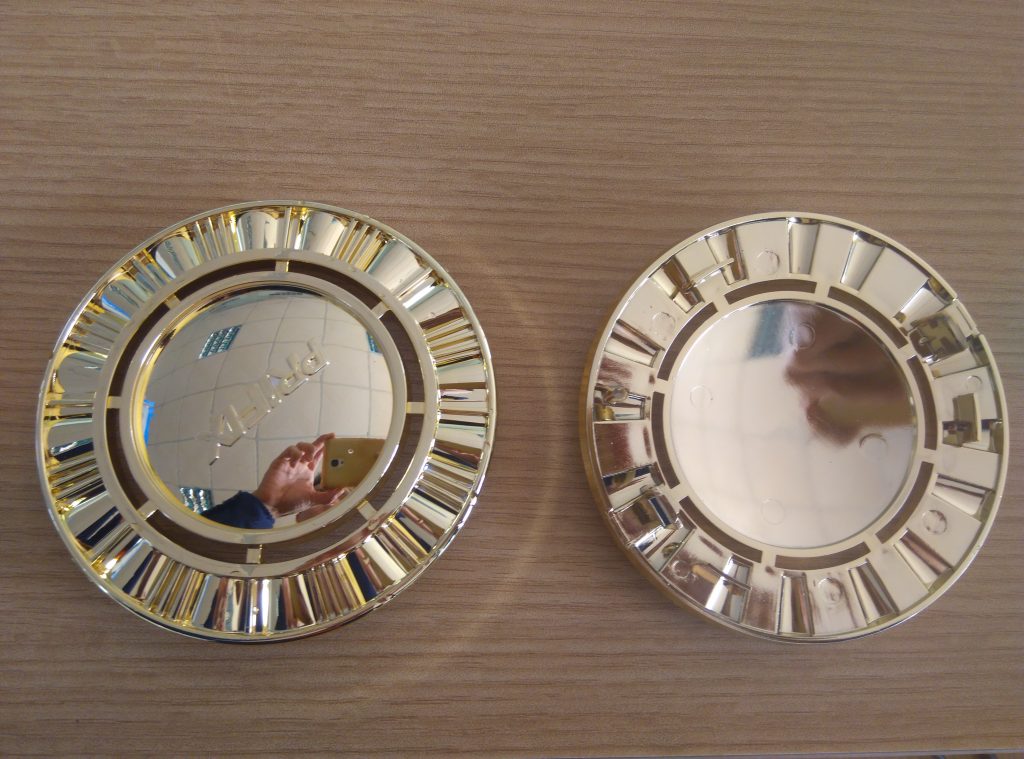
- Enhance corrosion resistance
- Plastics are usually chemically stable, but under certain special circumstances (such as humidity, high temperature or exposure to chemicals), plastics may suffer from corrosion or aging. By coating, an additional protective layer can be provided to the plastic, making it more resistant to corrosion and extending its service life.
- Improved optical performance
- PVD coating technology can provide optical enhancement effects on their surfaces, such as improving surface reflectance or reducing light transmittance. Such coating treatment can not only enhance the aesthetics, but also improve the functionality of the material.
- Increased ultraviolet (UV) resistance
- Especially clear plastics are susceptible to discoloration or degradation due to prolonged exposure to sunlight.
The main purpose of the PVD technology application in plastic products is to improve the aesthetic appearance of products, making them more high-end and artistic. Through the PVD coating, the plastic surface can present metallic luster, imitate the metal texture, add color and unique visual effects to meet the individual needs of consumers.
The special rainbow effect can present different colors at different angles to add visual impact, which is commonly seen in high-end accessories and limited edition electronic devices.
Provide Plastic PVD Coating Machinery
To achieve high-quality PVD coatings on plastic products, specialized plastic coating machinery is required. Modern PVD machinery for plastic applications are equipped with advanced technologies that enable low-temperature coatings, precise deposition, and uniform coverage. These machines can handle a variety of plastic substrates, ensuring high adhesion and durability of the coating.
Our Foxin focus on the characteristics of plastic high temperature easy to dissolve developed a suitable for low temperature coating machinery:
- Low-Temperature Coating Capability: Our advanced coating technology is specifically designed to preserve the integrity of heat-sensitive plastics. By operating at lower temperatures, it ensures that materials like polycarbonate, ABS, and other delicate plastics are coated without risk of deformation or warping, maintaining their original structural and aesthetic properties.
- High Precision: The precision of our coating process guarantees a consistent and even application across the surface of the material. This uniform coating thickness ensures long-lasting durability, excellent performance and perfect adhesion. Making it ideal for functional and decorative applications in a wide range of industries.
- Multiple choices:We specialize in the production of coating machines for more than ten years. According to different coating materials produced coating Machinery like Multi Arc Ion Coating Machinery and Magnetron Ion Supttering Coating Machinery. Our coating solutions are highly adaptable, compatible with a broad spectrum of plastics. Including but not limited to polycarbonate, ABS, PVC, and acrylic.
- Customization Options:Our coating service offers a wide range of options, from striking metallic finishes and color variations to sleek mirror-like gloss surfaces. This flexibility allows businesses to meet the your needs of the market, ensuring your products stand out while providing superior quality and performance.
By utilizing advanced PVD coating machinery, manufacturers can enhance the performance and aesthetics of plastic products, making them more competitive in high-end markets. Whether you’re producing automotive parts, electronics, or decorative items, our equipment provides the perfect solution for coating plastics with exceptional results.
If you want to learn more about the knowledge of the coating machine, welcome to contact us!