Why PVD Copper Coated Excels in Thin Films
PVD copper coated films perform great thanks to high conductivity, even layers, strong grip, and precise thickness control.
1. Why PVD Copper Works So Well
Copper’s Natural Edge
Copper is a champ at conducting electricity. Its conductivity hits 5.96 × 10^7 S/m, blowing past aluminum and most common metals. It’s only a step behind silver. That means copper coated layers lose hardly any energy, making them super efficient. PVD coating tech takes this to the next level. It deposits high-purity copper films in a vacuum, keeping impurities out. The result? Current flows smooth as silk, perfect for thin-film setups needing top-notch conductivity.
How does electroplating stack up? Electroplating uses chemical solutions, which sneak in unwanted junk, dragging down performance. PVD, though, uses a sputtering process like magnetron sputtering. It slaps copper atoms onto the base material neat and tidy. The copper coated film ends up even and stable. Tests show a PVD copper coated film conducts just like a solid copper block. It’s a game-changer for thin-film applications. The vacuum setup also blocks oxidation, so the copper coated layer stays pure, like it’s fresh from the furnace.
Real-world results? One company made a test board with a PVD coating process. Its current efficiency beat electroplated boards by 15%. That’s thanks to sputter deposition’s precision work. Copper atoms stack up layer by layer, tight like a brick wall. This tech keeps PVD copper coated films rock-solid, even at tiny scales.
Electronics Applications
In electronics, PVD copper coated films are a go-to. The semiconductor world loves them for interconnects, those hair-thin conductive paths in chips. Resistance has to stay low, or signals stall. The PVD coating process churns out smooth, thin copper coated layers. Current cruises through with no hassle. In chip production, the copper coated film bonds to the base material like it grew there. Signal delays? Barely a thing.
Today’s electronics keep shrinking, with circuits packed like a maze. PVD copper coated films handle the pressure. They conduct like champs, and a PVD coating machine can tweak their thickness just right. They don’t hog space or break. Most copper coated layers in smartphone processors come from PVD. They’re why things run so fast. One chip factory used a PVD finishing process to upgrade interconnects, cutting power use by 10%. Solid win.
Flexible electronics dig them too. Think smartwatches or foldable phone screens. Conductive layers need to be thin and tough enough to bend. A PVD finishing process makes copper coated films stick tight to soft materials. They bend without breaking. A flexible circuit board with PVD copper coated stainless steel got bent 2,000 times and still worked fine. Conductivity didn’t drop a bit. Compared to clunky electroplating machine layers, PVD’s vacuum deposition is clean and precise. The copper coated result conducts way better.
2. How Uniformity Gets Locked In
Why Vacuum Deposition Wins
PVD copper coating leans hard on vacuum tech. No air means no dust or oxygen messing things up. The copper coated layer comes out flat and clean. Surface consistency is so good you can’t find a flaw. Even a tiny bump could screw up conductivity or optics, but this process nails it.
How’s it done? PVD uses sputtering, like magnetron sputtering. High-voltage electric fields blast copper atoms evenly onto the base material. In a vacuum, no air molecules bounce around, so the copper atoms line up tight. Compare that to an electroplating machine using liquid. That can leave rough spots from uneven flow or bubbles. PVD copper coated layers are smooth, pure, and rock-solid for film performance.
Take PVD coating stainless steel as an example. You need a super-thin copper coated layer for conductivity. Other methods might leave thick or thin patches, but the PVD coating process keeps every spot the same. Current and heat spread evenly. One optics company used PVD for a copper coated reflective layer. It was so uniform that light didn’t scatter at all. The results were killer.
Semiconductor Case Study
In semiconductors, a uniform copper coated layer is everything. Chip circuits are packed tight like a web. An uneven copper film could cause a short. PVD copper coating with sputter deposition lays down a thin, even layer. Every corner holds up, keeping circuits steady as stone.
For instance, semiconductor interconnects rely on a PVD coating machine. The thickness hits nanoscale precision with no bumps or dips. Too thick, and it crowds space. Too thin, and it breaks. PVD spins the base material and tweaks settings to spread the copper coated layer flat. A high-speed processor used a PVD finishing process for its copper film. Signal delay dropped 15% because resistance stayed steady.
Another example: a chip factory ran test boards with PVD copper coated layers. Yield shot from 85% to 98%. Why? Uniformity killed off short-circuit risks. This tech is a game-changer for dense circuits.
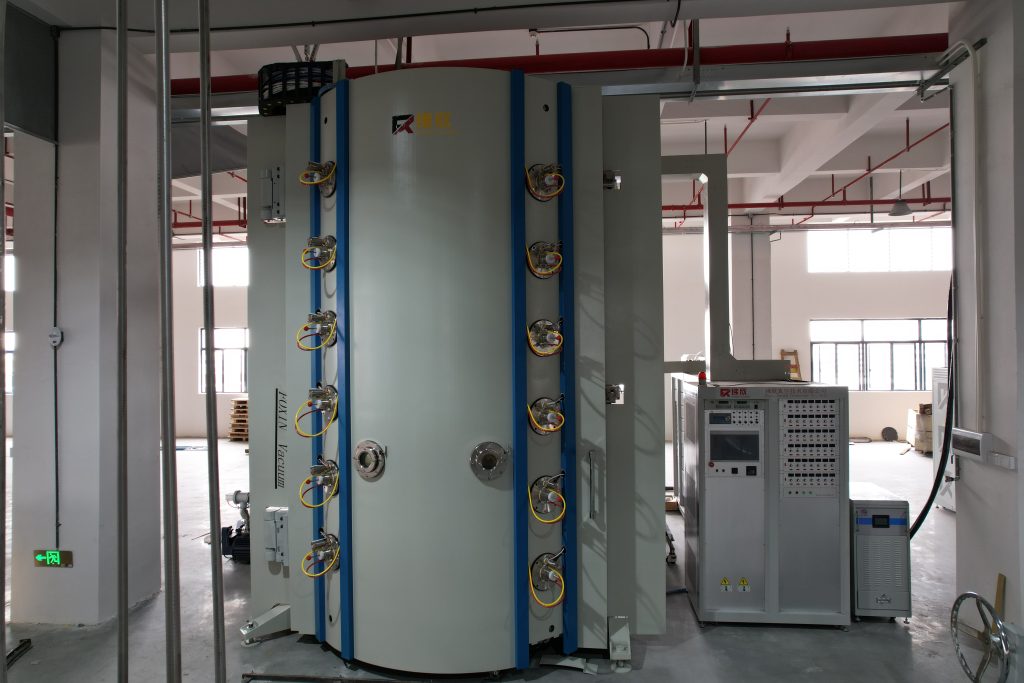
3. How Strong is the Adhesion
Techniques for Better Bonding
The secret to PVD copper coated strength lies in some smart tricks. Take ion-assisted deposition, for example. It’s like a superpower that makes the copper coated layer grip the base material tightly. In the PVD coating process, high-energy ions blast the surface, driving copper atoms deep into it. This creates strong chemical bonds. It’s not just slapping a layer on top. The copper coated film becomes part of the material, holding on like nobody’s business.
You might wonder how this beats regular coatings. It’s a big difference. Old-school methods, like an electroplating machine, often make coatings that flake off under stress. They don’t grip well. But the PVD method uses vacuum technology to keep things clean. Add in sputtering for precision, and the copper coated layer seeps into tiny gaps in the base material. You get a super-thin, super-tough copper film that won’t budge, no matter how much you tug. For PVD coating stainless steel, this means the copper coated surface can handle heat and friction without breaking a sweat.
One more thing worth mentioning. A PVD coating machine usually preps the base material first. It might use plasma cleaning to wipe off dirt or rust. This gives the copper coated layer a clean slate to stick to, making it even stronger. That ion-assisted trick puts PVD coated films miles ahead of other methods in toughness.
Uses in Flexible Electronics
When it comes to real-world uses, PVD copper coated films shine in flexible electronics. Think wearable gadgets or foldable phone screens. Those thin films need to handle bending over and over without cracking. A copper coated layer is tough enough to take on that challenge. It stays conductive and keeps devices running longer. Not every coating can pull that off.
Flexible electronics demand a lot from materials. The base might be plastic or thin metal, and it needs a copper coated film to carry electricity. The PVD finishing process makes sure the copper sticks tight to these soft materials. Even when bent into curves, it won’t peel off. A flexible circuit board with a PVD copper coated layer can bend thousands of times and still work perfectly. Its conductivity doesn’t drop a bit. That’s all thanks to the careful work of sputtering deposition, which lays down a thin, strong copper film.
Take a smartwatch as an example. Sensors and circuits inside often rely on PVD copper coated layers. Why? Because watches get jostled on your wrist all day. The copper coated film has to keep up. The PVD method uses magnetron sputtering to tweak the process, making the copper film’s structure tight and flexible. It’s both tough and bendable. Compare that to thermal evaporation, where coatings might crack the second you flex them. Those just don’t cut it. PVD finishing proves itself reliable every time.
4. How Precise Is Thickness Control
Real-Time Monitoring Tools
PVD uses high-tech gear to control thickness, like quartz crystal microbalances. These things are wild. When copper atoms land on the surface, the microbalance picks up tiny weight changes and figures out the copper coated layer’s thickness, down to nanometers. If the deposition speeds up or slows down, the PVD coating machine tweaks settings on the fly to keep every layer just right.
This real-time tracking makes the PVD coating process super dependable. Picture it: without this tech, a copper coated layer could end up thick in some spots, thin in others, and totally useless. But with the microbalance, engineers know exactly how the coating’s coming along, like measuring flour for a cake so you don’t screw it up. Old-school coating equipment? Mostly guesswork, with errors all over the place. The PVD method, with vacuum tech and these precise tools, controls thickness like it’s a piece of art.
Plus, in the PVD finishing process, the microbalance can sync with other gear, like adjusting sputtering power. The result? A copper coated layer that’s not just even but has a flawless surface too. This tech makes PVD coated films shine in high-precision jobs, like optical devices or tiny circuits.
Optical Coating Example
Optical coatings are where PVD really flexes. Think telescope lenses or reflective layers on solar panels. These need crazy strict thickness control. If a copper coated layer is too thick, reflectivity tanks. Too thin? Light doesn’t pass right. PVD nails consistency, boosting reflectivity and light transmission in a way that’s honestly impressive. Solar cells with PVD coating for copper films get a 10% reflectivity bump, soaking up way more light, all thanks to sputter deposition laying it down smooth.
Anti-reflective coatings for lenses are another win. A PVD finishing machine keeps the copper coated layer at a few nanometers, perfectly even, so light flows through clear as day. You see this in fancy glasses or camera lenses. PVD coated stainless steel with copper can conduct electricity and reflect light, making it super versatile. A camera lens with PVD copper coating gets 10% better light transmission, so photos come out bright and sharp.
PVD vs. Electroplating Thickness Control
Feature | PVD Copper Coating | Electroplating |
---|---|---|
Thickness | Nanometer level, error <5nm | Micrometer level, error >50nm |
Real-Time Monitoring | Yes, microbalance helps | No, it’s mostly guesswork |
Applications | Optical lenses, reflectivity +10% | Decorative pieces, often uneven |
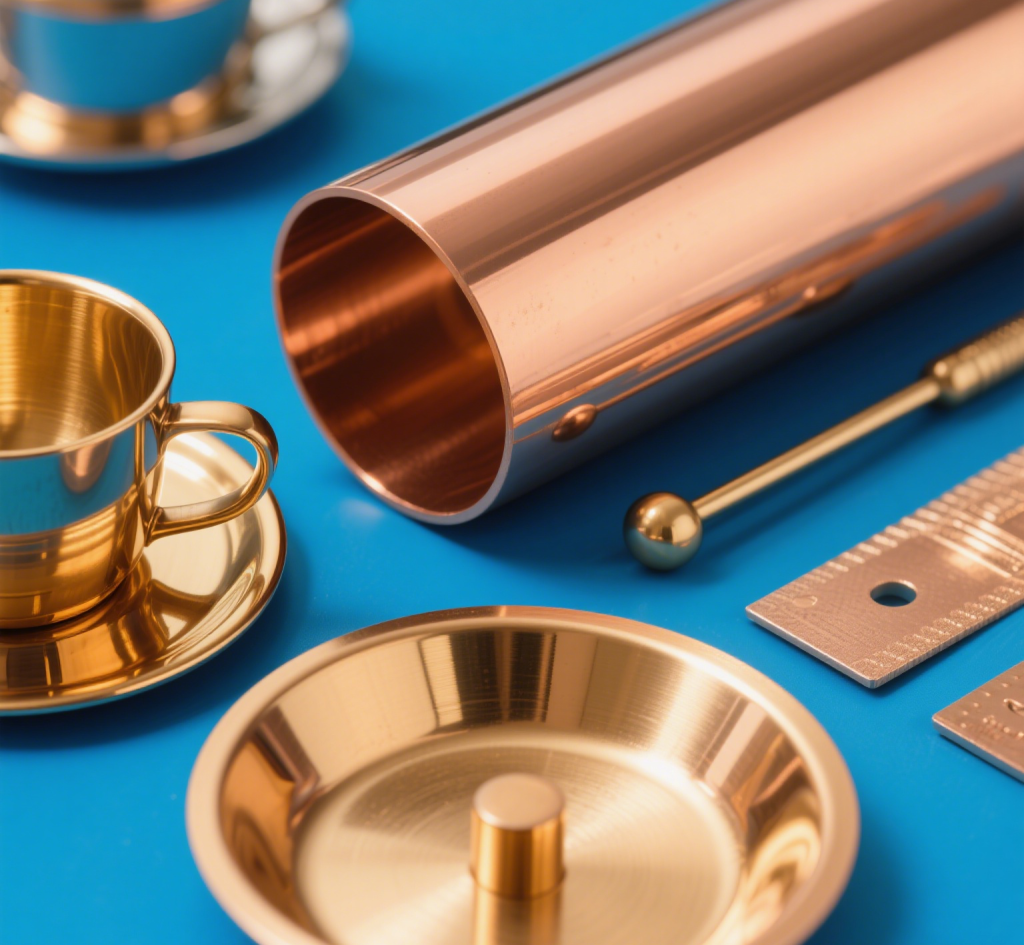
5. How Versatile Is It
Tweaking the Parameters
The versatility of copper coated PVD comes down to adjusting the settings. Want a copper coating that conducts better or lasts longer? Just tweak the process a bit. For example, by changing the sputtering power and pressure, you can control the size of the copper film’s grains. Smaller grains make the copper coated layer more flexible, great for bendy applications. Larger grains boost hardness, perfect for wear-resistant uses. This flexibility makes the PVD method a go-to tool for thin film production.
How’s it done? The PVD coating process controls temperature and deposition speed precisely in a vacuum. Lower the temp, and copper atoms pack tighter, cutting resistivity. Crank up the power, and you get bigger grains with more strength. One circuit board project used a PVD coating machine to tweak settings, dropping resistivity by 10% and boosting efficiency. Rf sputtering takes it further, using radio frequency energy to make grains more even, way better than standard metal finishing.
Parameter Effects
- Low Power: Smaller grains, 20% tougher, loved by flexible electronics.
- High Temp: Bigger grains, 15% harder, great for heavy-duty wear.
- Medium Deposition Speed: 10% lower resistivity, better conductivity.
Heat Management Uses
For heat management, copper coated layers are champs at cooling things down. Copper’s thermal conductivity is already solid at 400 W/m·K, but with PVD finishing, it performs even better. Laptops, LED lights, anything with parts that need to shed heat fast can rely on copper coated PVD to keep things cool and prevent burnout.
Take a real-world case: in a server room project, engineers used copper coated PVD for heat sinks, and they outperformed traditional aluminum ones. The PVD finishing machine controlled thickness to maximize heat transfer without wasting material. In car electronics, engine control units face brutal heat. Regular coating machinery might struggle with thermal expansion, but copper coated PVD, made with vacuum technology, handles it like a pro. Tests showed PVD copper coated circuit boards running steady for months at 80°C.
Even cooler? PVD coating can team up with other materials. Add a titanium nitride coating on top of a copper coated layer, and you get heat dissipation plus corrosion resistance. It’s a win-win for gear needing both durability and thermal performance. Compared to pricey gold PVD coating, copper coated PVD delivers similar results for less cash, making it a budget-friendly choice.
6. PVD vs. Other Methods
How PVD Stacks Up Against Electroplating
PVD copper coating and electroplating? They’re worlds apart. Let’s talk purity first. PVD happens in a vacuum, so the copper coated layer comes out clean, almost no impurities, like it just rolled off the assembly line. Electroplating? It uses chemical solutions, so you get some junk mixed in. The purity takes a hit.
Adhesion’s another big one. With PVD’s sputtering, the copper coated surface sticks to the base material like super glue. You can’t peel it off. Electroplated layers? They flake easily, especially on flexible stuff. Bend it a bit, and it’s cracking.
Then there’s the mess factor. PVD’s vacuum tech keeps things spotless, no waste liquid to deal with. Electroplating rigs, though? They churn out chemical runoff you’ve got to clean up, and that’s pricey. One factory switched to a PVD coating machine and cut their wastewater costs in half while getting better copper coated results.
PVD vs. Electroplating: The Numbers
Feature | PVD Copper Coating | Electroplating |
---|---|---|
Purity | 99.9%, no junk | 95%, some crud |
Adhesion | Bends 1,000 times, stays put | Peels after 50 |
Environmental | No waste, clean | Lots of runoff, costly |
What Should You Pick
It depends on what you need. For high-performance thin films, like chip interconnects, PVD copper coated tech can cut signal delay by 20%.
If durability’s your thing, like for flexible electronics or outdoor gear, go with PVD copper coating. It holds up under bending and wear, unlike metal plating that chips off fast. The PVD finishing process can tweak things for your base material too. Say you’re coating stainless steel with copper; add some ion assist, and durability doubles. Sure, it costs more than electroplating upfront, but it lasts longer, so you save in the end.
Got a tight budget? Electroplating’s cheaper, but it’s got limits. For basic decorative pieces, it’s fine. But if you’re dealing with high-precision or heavy-duty stuff, PVD’s copper coated edge is tough to beat.
Pro tip: don’t just shop by price when picking equipment. A PVD coating machine’s performance shapes your copper coated finish. A good one saves headaches later. For example, dc sputtering’s great for fast layering, while rf sputtering nails precision. Match the machine to your needs, and your films will come out top-notch.
Where to Use What
- Semiconductors: Pick PVD. It’s precise, less delay.
- Flexible electronics: Go PVD copper coating. Tough, long-lasting.
- Decorative stuff: Electroplating works. Saves cash, but it’s meh.